"You do not need to be Alan Greenspan to understand that the more things a machine can do, the bigger the market.”
- Fred Hapgood, Discover Magazine, June 2008
As we develop product prototypes in today’s modern world, it is crucial that we understand our capabilities — especially when producing parts for a project. It means that, as industrial designers and developers, we must understand our tools well enough to make a part. These processes apply to prototyping and contract manufacturing of many different types of products, including those with embedded systems. And if we can’t build it, we should understand the process well enough to defer to another resource who can.
For those who may not understand the ins and the outs of machining and how it relates to mechanical design, we’ve compiled a list of several machine shop tools and processes that we as product developers employ. We think the technology behind these is pretty cool, and we think you will, too.
Machine Shop Manufacturing
For the sake of brevity, we will provide a high-level view of the most commonly used machines in the industry, particularly when creating product prototypes. Although there are several types of machines that have widely different applications, most machines today have been replaced by advanced computerized machines that can perform multiple tasks.
In each instance when we refer to machine shop equipment, we are focusing on subtractive manufacturing. This means that, just as it sounds, we are removing material from something to make a shape. A perfect example is Michelangelo’s David.
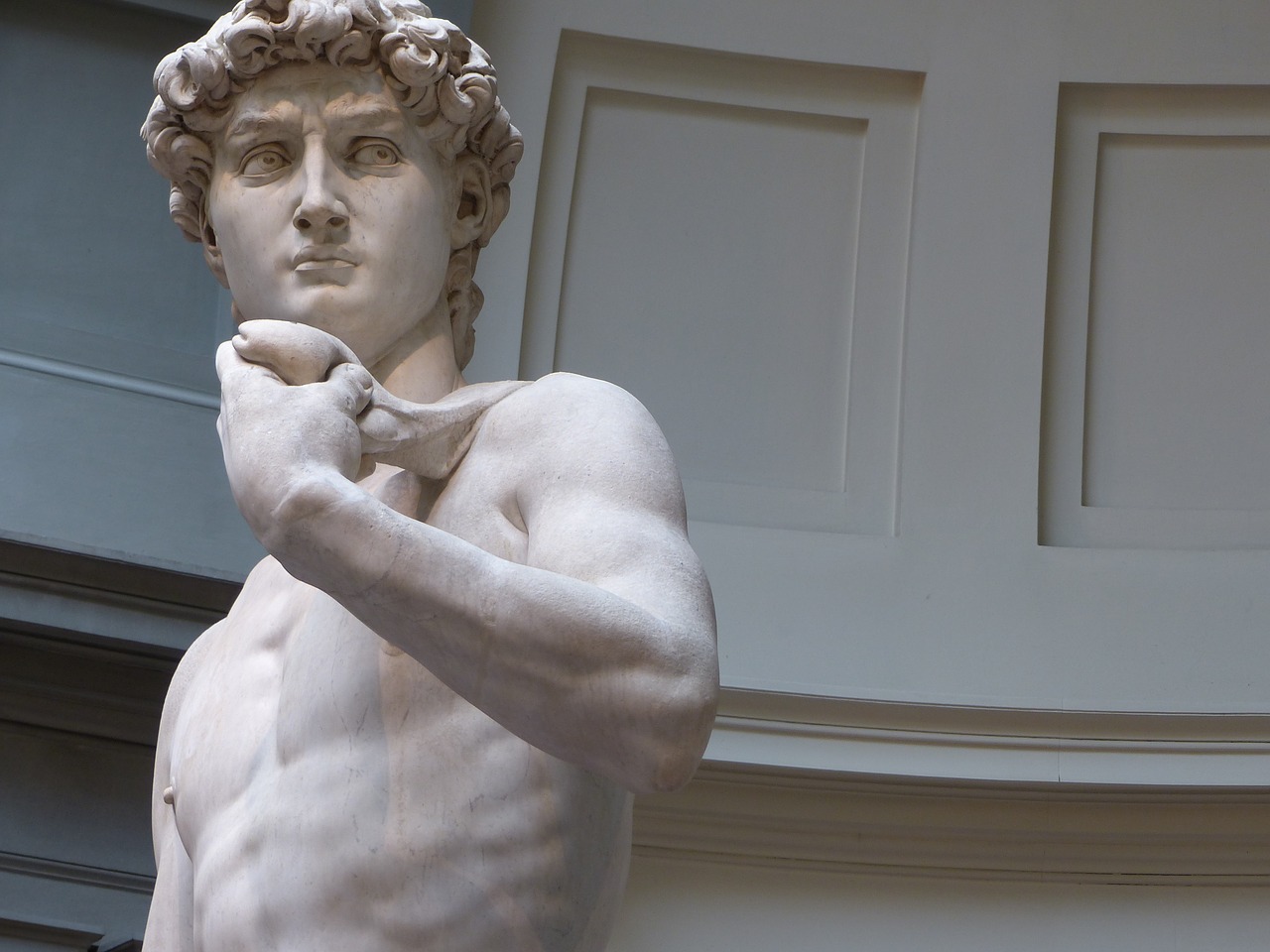
Michelangelo carefully chipped away at a gigantic block of stone with a chisel and hammer to create the lifelike statue. Machine shop processes work the same way. They take off little bits of material until a shape is made.
So let’s talk machines.
Using Mills to Make Product Prototypes
There are several types of mills in use today, all of which use a spinning tool to remove material. The most common type is the vertical mill. This machine’s tool is positioned vertically and moves material around the tool (or vice versa). Many simple mills allow material to be worked on three axes: X, Y, and Z. (Think of these as left and right, forward and back, up and down.) This allows the operator to make simple two-dimensional parts such as engine covers, airplane ribs, gaskets, and metal cases.
Mills have a huge range of tools and uses that are helpful for creating product prototypes. They can do anything from cutting off large chunks of material and drilling holes to making threading and much more. They are a very useful tool for machine design projects.
Most modern industrial mills are fully computerized. A piece of material is placed in the machine, then the design is loaded. The mill will then make the part by itself. These are called CNC mills (CNC stands for Computer Numeric Control). Although very powerful, they still need a skilled operator to ensure the job gets done right.
Some mills (most used at the industrial level) are capable of five or six axes of movement. Think X, Y, and Z but with the ability to turn on any of those axes. Their method of cutting does not change, but movement on more axes enables the machine to cut a significantly more complicated part. This allows a greater level of freedom for the designer.
Because these complex machines are fully automated, they are capable of producing more parts, more quickly and with greater accuracy. Without these machines, it would take an operator much longer to make complex parts.
Five or six-axis machines are also capable of performing turning tasks. This makes them extremely versatile and helps save time and money while increasing their capabilities. They can produce three-dimensional parts like crankshafts, propellers, or even engine heads.
Let’s say you wanted to make a reproduction of the David statue on a three-axis mill. You could probably accomplish this by repositioning your part many times to accommodate the movement of the machine and using specialized tools. But it would take a very long time. Conversely, a six-axis machine could reproduce the statue in just one run since it has the ability to access the complicated features of the statue.
Manually operated mills are still useful for making parts, namely when a part doesn’t need to be reproduced several times. Simple manual mills are also perfect for beginners to learn on.
Lathes
The lathe is a long-established and useful machine used for creating product prototypes. Lathes are used to make cylindrical parts and parts with curvature. Think about drive shafts, chess pieces, cannons, bowls, and similar objects — these are typically made using a lathe. This type of machine comes in many sizes, from tiny watchmaker’s lathes to heavy industrial lathes that spin gigantic parts for supply ships and power plants.
How the lathe works is relatively simple: it turns either clockwise or counterclockwise, and unnecessary material is removed from the object as the machine spins.
Lathes can be manual or CNC-controlled. On smaller machines (typically only machines meant for turning wood) the tool is actually held in the operator’s hand. At the machine shop level, a lathe is useful for making pins, dowels, and other components. At a more industrial level, they can be used to crank out staircase banisters.
One key distinction between the lathe and the mill is that the lathe turns the part around the tooling, where a mill moves the tooling around the part.
Plasma Cutters, Waterjet Cutters, and Routers
When working with sheet metal, wooden boards, or long pieces of material, it is easy to make holes, cuts, or apply designs by using a type of two-dimensional cutter. This can be particularly useful for custom enclosure designs. The type of cutter needed usually depends on the material being cut. A board can be cut on a router that spins a cutting tool (very similar to a mill), but a thick aluminum part might be more easily handled by a waterjet cutter. A plasma cutter is well-suited for heavier materials such as steel.
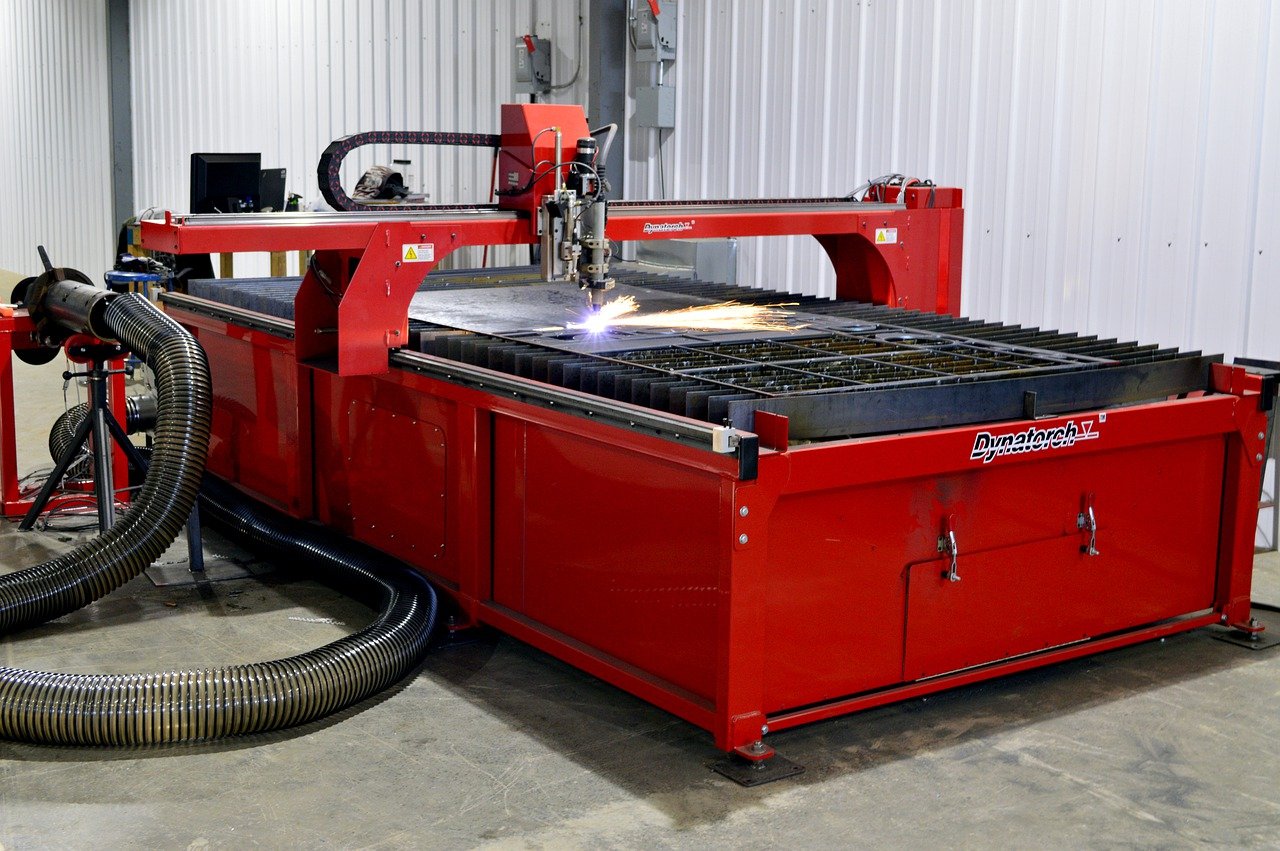
Cutters can be used to cut a large piece of material into a more maneuverable piece that can be put on a mill or other tool. But more often, they are used to apply text or design (again using CNC guidance).
One application of a plasma cutter would be to make a detailed sign for a business storefront. Another common use of routers is to put holes in sheet metal, a task which could take a lot longer if performed on a drill press or other machine. Routers are also popular with woodworkers to easily apply a design to a panel of wood.
Power Saw
Often, when producing parts for product prototypes, we start with much bigger pieces of material than we need. For long parts such as bars, tubes, or extrusions, the best way to get them to the right size is to cut them on a power saw.
There are several different types of saws, but one of the more common in a machine shop is a powered bandsaw. This saw can be fitted with specialized blades to cut metals.
The process is pretty simple. The material is first moved under the saw, sometimes supported by a long table or line of rollers to avoid deflection, and then the cutting head is lowered down into the material.
The power saw is mostly a tool used to prepare materials for more accurate manufacturing processes since the cuts are usually too rough for final products.
Brakes and Shears
Sheet metal is very useful when building product prototypes. Although there are many tools specifically for sheet metal parts, brakes and shears are some of the more common ones.
A brake can bend sheets or bars of material to a desired angle either by lifting a bar manually, or using a control console. Shears cut metal by dropping a heavy cutting head down on the material. Shears are usually electric, hydraulic, or powered by compressed air.
Sheet Metal Processes Used to Make Product Prototypes
Usually a machine shop doesn’t have much specialized sheet metal equipment. Instead, because there is so much that can be done with sheet metal, there are entire factories dedicated exclusively to sheet metal production.
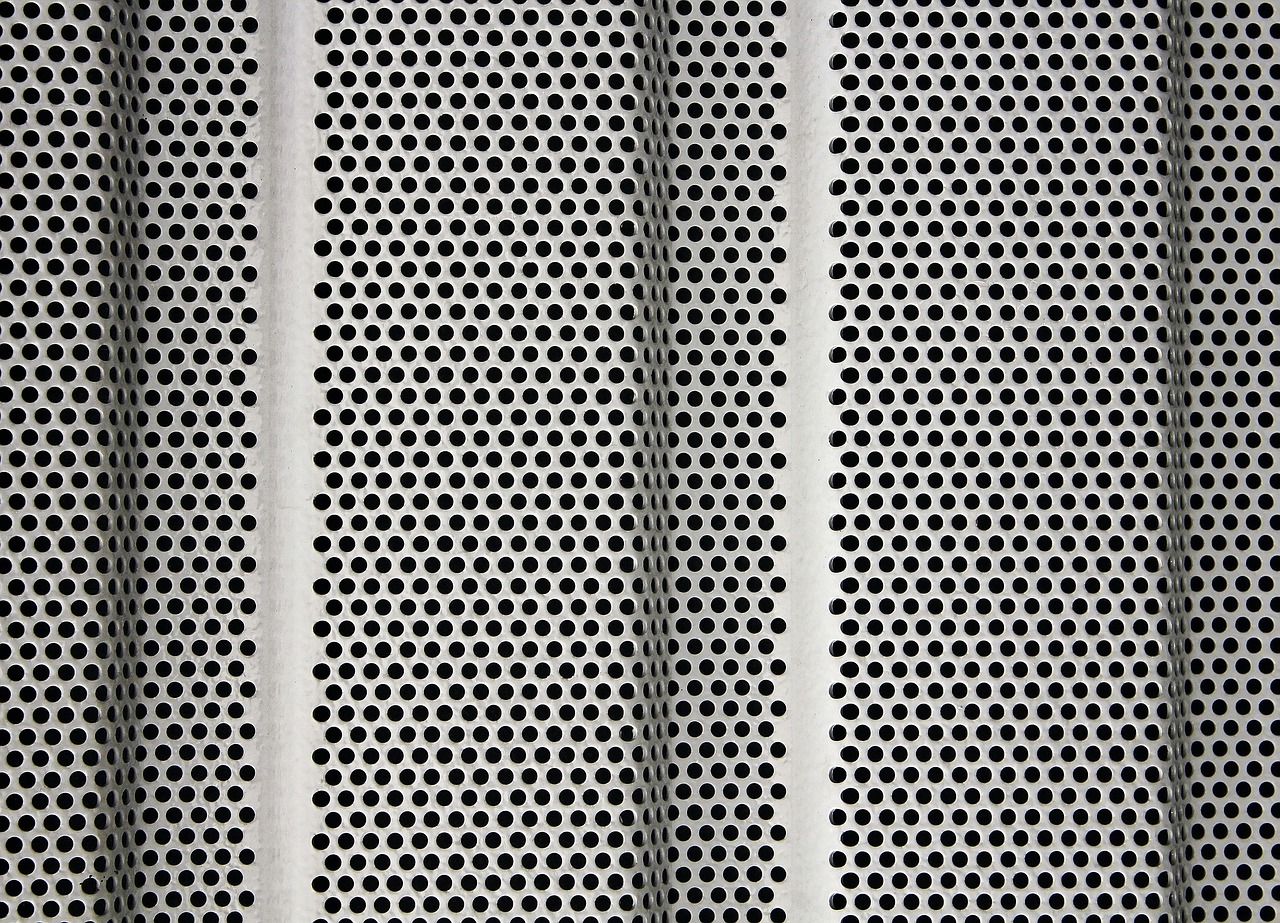
But understanding how sheet metal parts are made is critical for a successful design. Parts can be punched out using dies, and stamps can bend flat sheets into sinks or car parts.
Sheet metal fabricators can turn a two-dimensional design into a three-dimensional part. To this end, there is a huge range of toolings available and a wide range of machine sizes that can accomplish different bends and tolerances to make sheet metal parts.
Grinders and Sanders
One way to think about grinders and sanders is as smaller, gentler, subtractive manufacturing machines. They can usually fit on a bench, and are used to grind down parts, sand down sharp edges, sharpen blades, and can reach very fine tolerances on certain parts.
Larger sanders and grinders are often used to remove more material. For example, a large, circular sander is strong enough to round off the edge of a steel pipe for welding. This is faster than cutting the pipe some other way, however it is less accurate (which is fine for certain projects).
Some grinders such as angle grinders can be used to grind down bolts or bulges produced from welding. This can be a good way to finish parts and help prepare them for other steps in manufacturing.
Polishing wheels are also considered an abrasive tool in the same family as grinders and sanders. These allow us to buff out scratches or polish something into a mirrored finish.
Welding Product Prototypes
There are numerous types of welding machines meant for different types of jobs — and most are useful when making product prototypes. Welding is used to fuse together metal parts. Generally, the way this process works is metal is heated up, then material is added to the location you want to weld, and presto! Two parts become one.
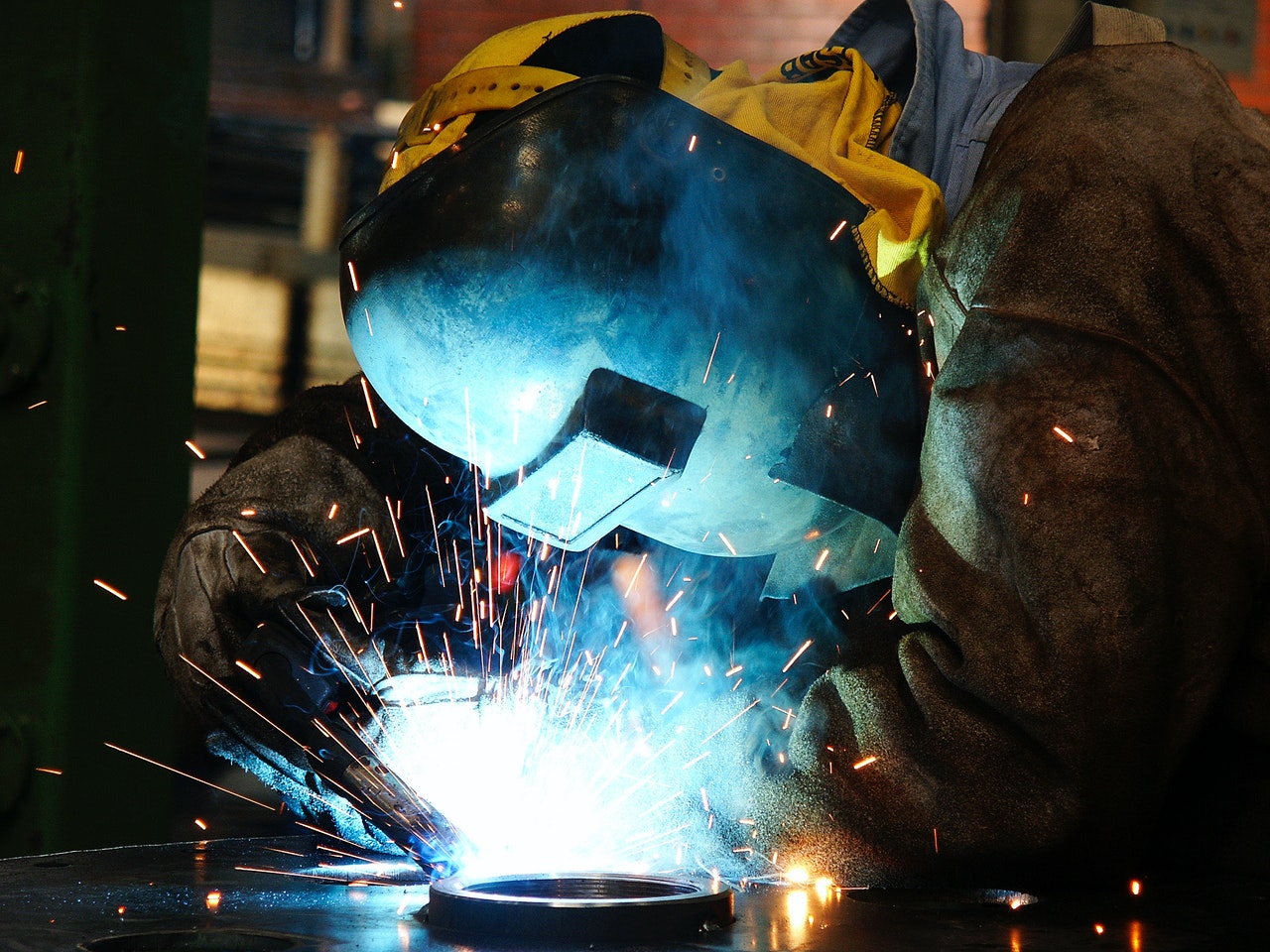
In its simplest form, welding uses two gases to accomplish the process of fusing metals. Modern welding machines use high-voltage arcs and shielding gas to make faster, cleaner welds. Heavy industries such as railroads use other methods like friction welding and thermite welding. These are techniques suitable for very large, thick parts.
Unlike most machine shop processes, welding is additive. This means, rather than substracting material, it adds fill material to a location in order to keep components together. Welding often calls for preparation work such as cutting and cleaning in order to achieve a good, strong finish.
Drill Press
A drill press, like the name suggests, is a drill that has been mounted on a lever and it can be lowered into the part. Drill presses are used primarily for making holes, but they can also put threading into parts. Drill presses provide accuracy and leverage that you cannot get with a handheld drill.
Other Tools Used to Make Product Prototypes
Although larger machines do most of the work, there are a myriad of other tools that machines shops use — or could use — to build product prototypes. These include wrenches, die presses, screwdrivers, handheld plasma cutters, angle grinders, files, shovels, sandpaper, hand drills, and anything else the shop might need.
Typically, these tools are dependent on what kind of work is being done. For instance, if a machine shop specializes in making hot rods, they probably have rivet tools and polishing tools available. A gun shop might have baths of chemicals to treat metals in order to get just the right look or function from them. These are also common in engine shops to clean off grimy parts.
Forging and Extrusions
When building product prototypes, forging is a technique used for making larger metal shapes which can then be cut by other machines. This process allows us to make parts that would normally be cost-prohibitive or impractical to make out of a single piece of metal. Sometimes material isn’t even available in the sizes an extrusion can produce.
Forging sometimes involves making a mold of some kind that can withstand very high temperatures (in the range of 2,000 degrees Fahrenheit) and pouring molten metal into the mold to make a shape. After the metal cools and hardens, the mold is broken away and the part is removed. From there, the part can be put on other machines to make engine blocks or any wide range of parts.
Heavy industry, as well as blacksmiths, use a technique called hammer forging. This process entails using a hammer to pound a gigantic lump of malleable (not molten) metal into a shape very close to the final product.
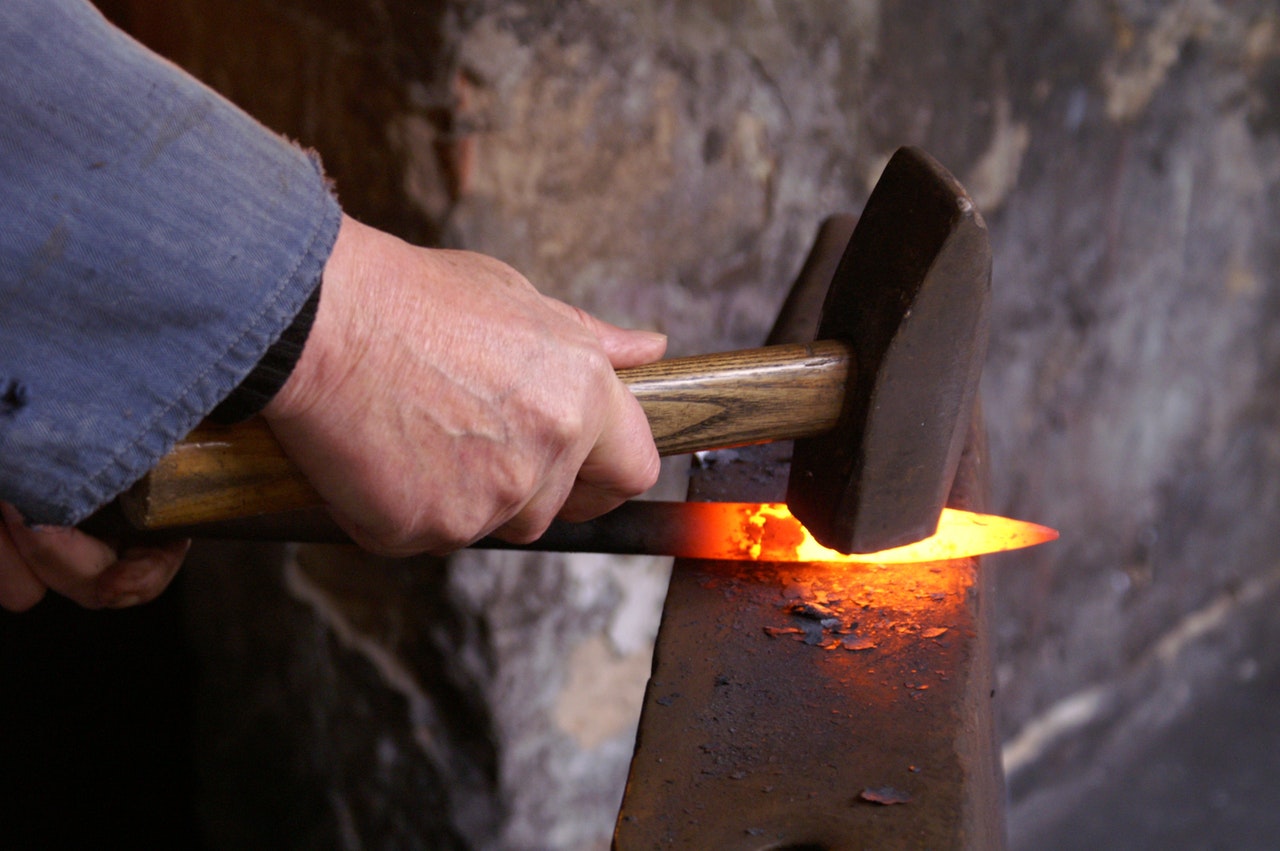
Extrusion machines force materials through a tooling which forms the material into a shape. By combining toolings and changing the direction the material is pushed, elaborate shapes can be made. A very common extruded product is 80/20 tubing.
Extrusions usually only need to be cut, drilled and given coatings to be ready for use.
Aluminum is one of the most common materials used in extrusions because of its relative flexibility as a material. Plastics and other metals can also be used in extrusions. Pasta and sausage are also made using an extrusion process, and they are by far the best-tasting extrusion products available.
What Machine Processes Are Right for Your Product?
We hope you enjoyed this inside look at the machines and processes we employ in product design and building product prototypes. Are you developing a product, and trying to decide which processes are appropriate for prototyping your product? Or long term manufacturing? Give us a call to talk to a development engineer.