Pivot Irrigation Drive Unit
Design, engineering, and optimization of an innovative new ag-tech product for pivot irrigation systems
Ag tech startup
Mechanical Engineering, Injection Molded Part Design, Design for Manufacture
2019
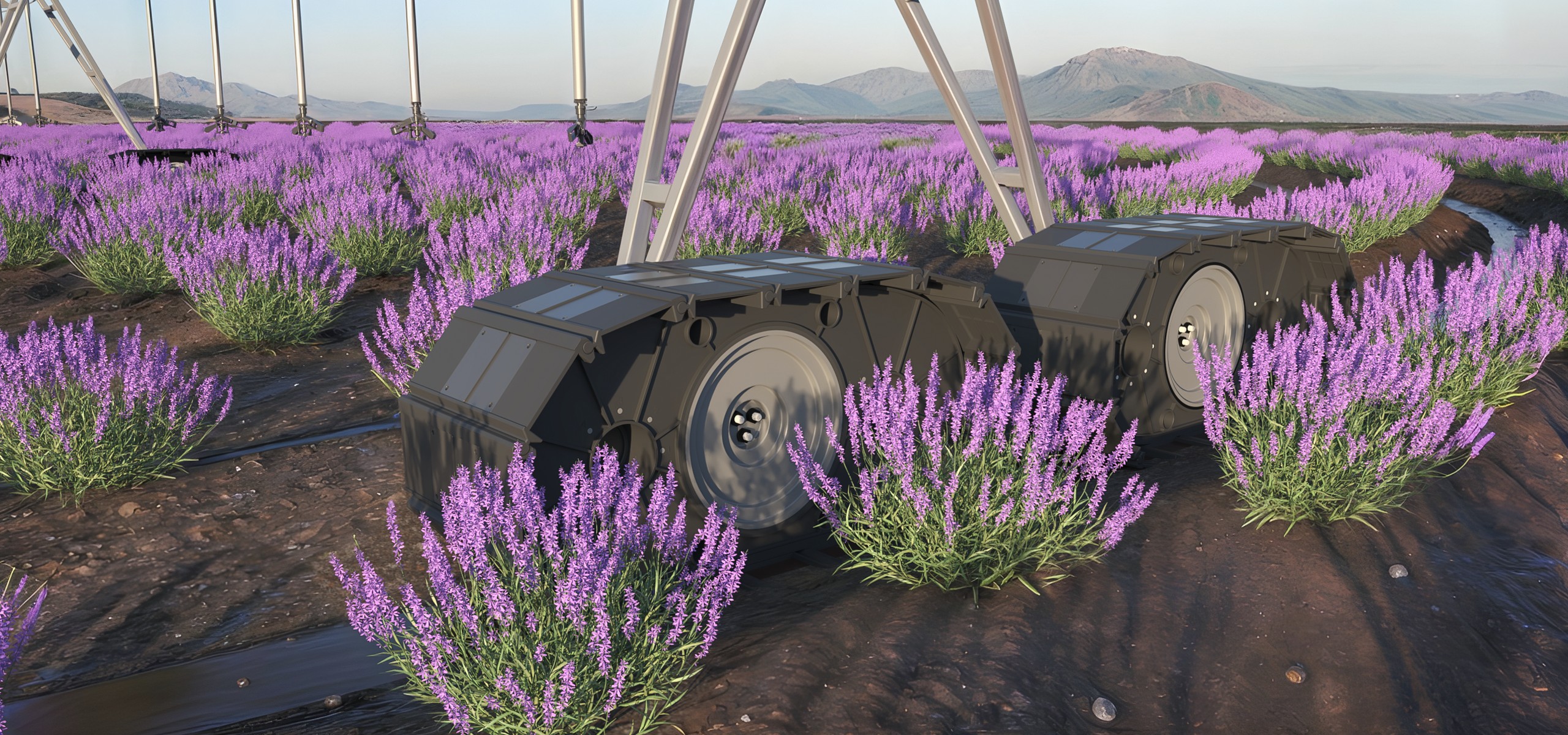
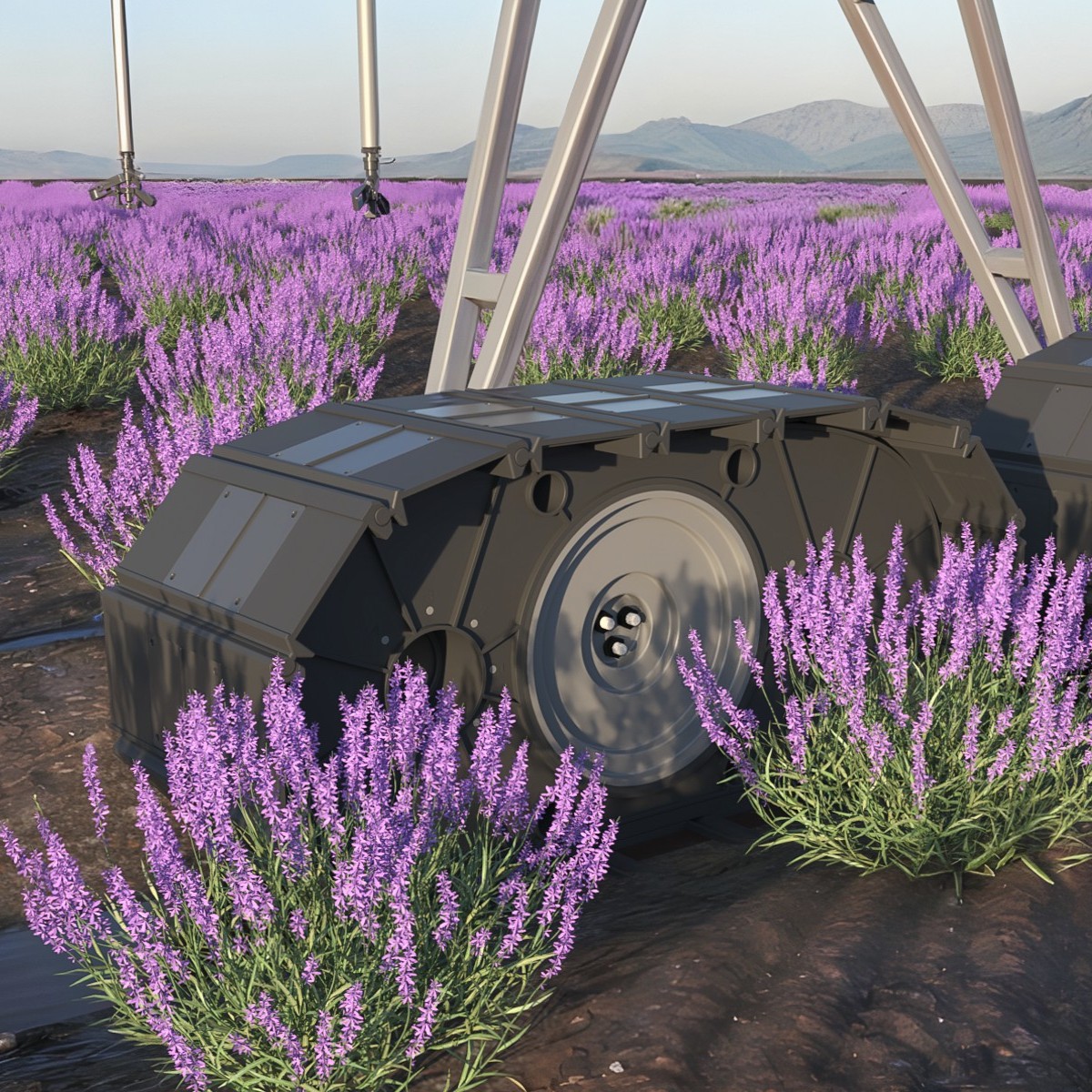
The vision was to make pivot irrigation systems easier to live with. By replacing wheels with a large tread, loads would be distributed over a larger area, solving a number of problems for farm owners.
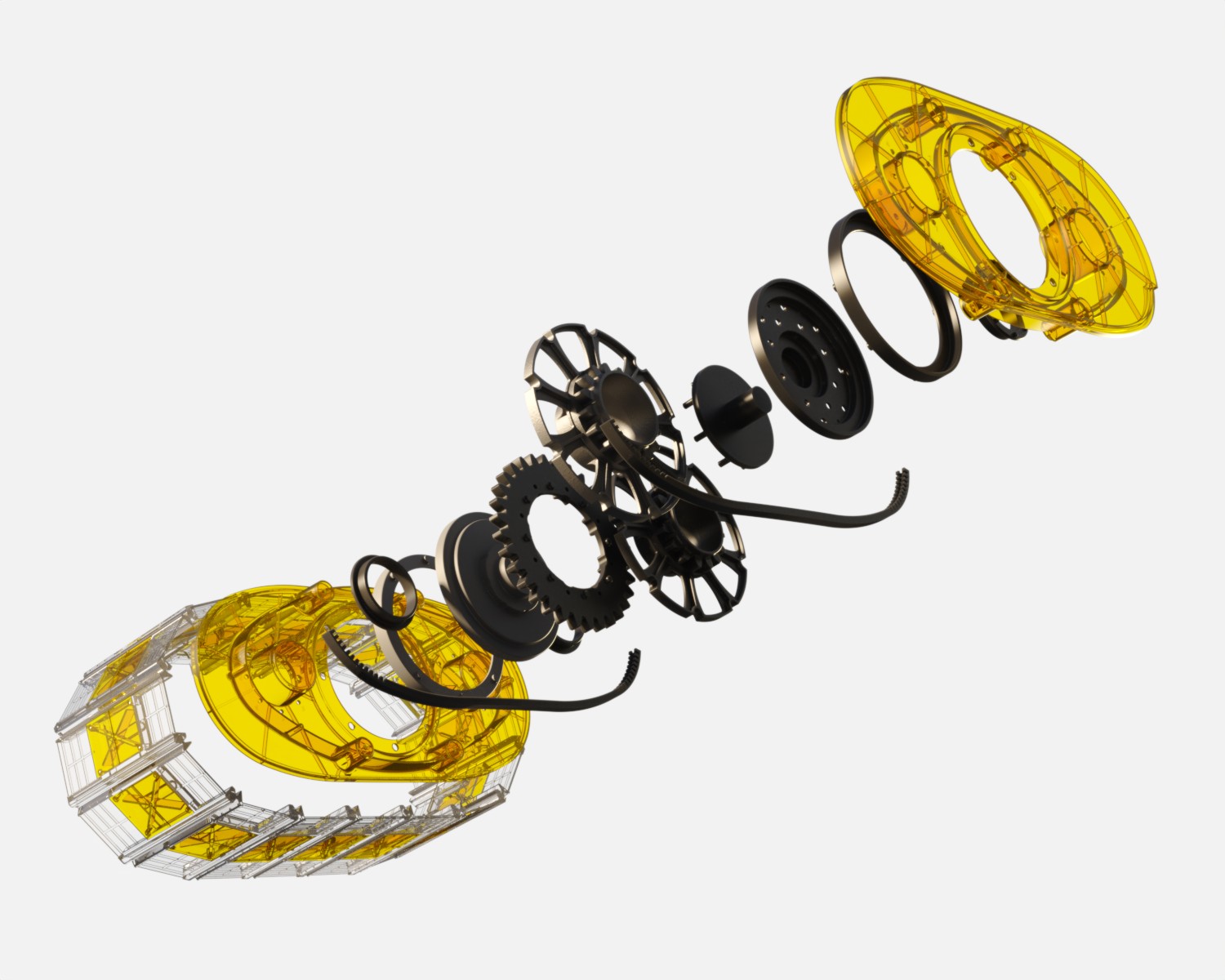
Product Vision
Solving a problem that farmers have lived with for decades, with a totally new approach.
The drive wheels commonly used in pivot irrigation systems create some specific problems for land owners. The narrow wheels and tires tend to leave deep ruts in the field, which slows down harvest equipment. To eliminate this problem, a tread could be used in place of the typical wheel and tire, which would spread the heavy load of the irrigation system across a greater surface area. This would reduce or eliminate the problematic ruts. But the tread system would need to be extremely tough, carry huge loads, and be ultra reliable.
Final Outcome
The extreme loads that the tread would need to support as well as the need to keep system weight in check required an innovative engineering approach.
Low production cost and light weight were critical to the commercial success of the concept, as was the ability to support massive loads. For various reasons, injection-molded plastic needed to be the primary material used in this large, robust assembly. The loads that the drive system must support push the entire drive assembly to the limit. Advanced finite element analysis, simulation, and geometry iteration were required to define designs that will provide reliable service in a critical application. This drive assembly was analyzed and engineered by SGW Designworks to be manufactured entirely from injection-molded glass-filled nylon. DuPont joined the project team to help with the specific custom formulation. The final design was comprised entirely of injection-molded plastic, with the exception of the hub. Through multiple design iterations and prototype cycles the engineering team was able to develop a system design that was robust, light weight, and cost effective to manufacture.
The product went in to production in 2019, and is being adopted in agricultural operations across the US.
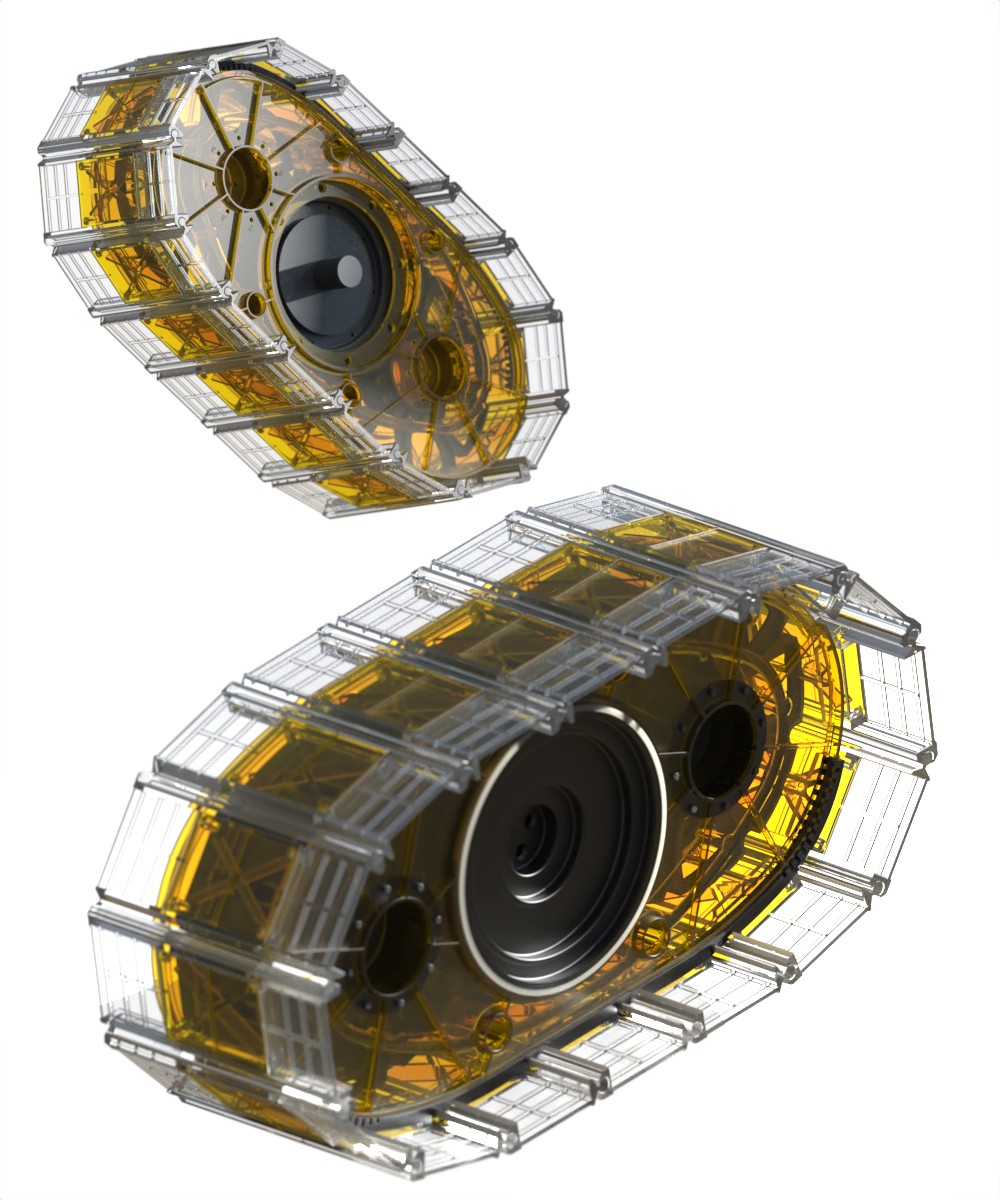
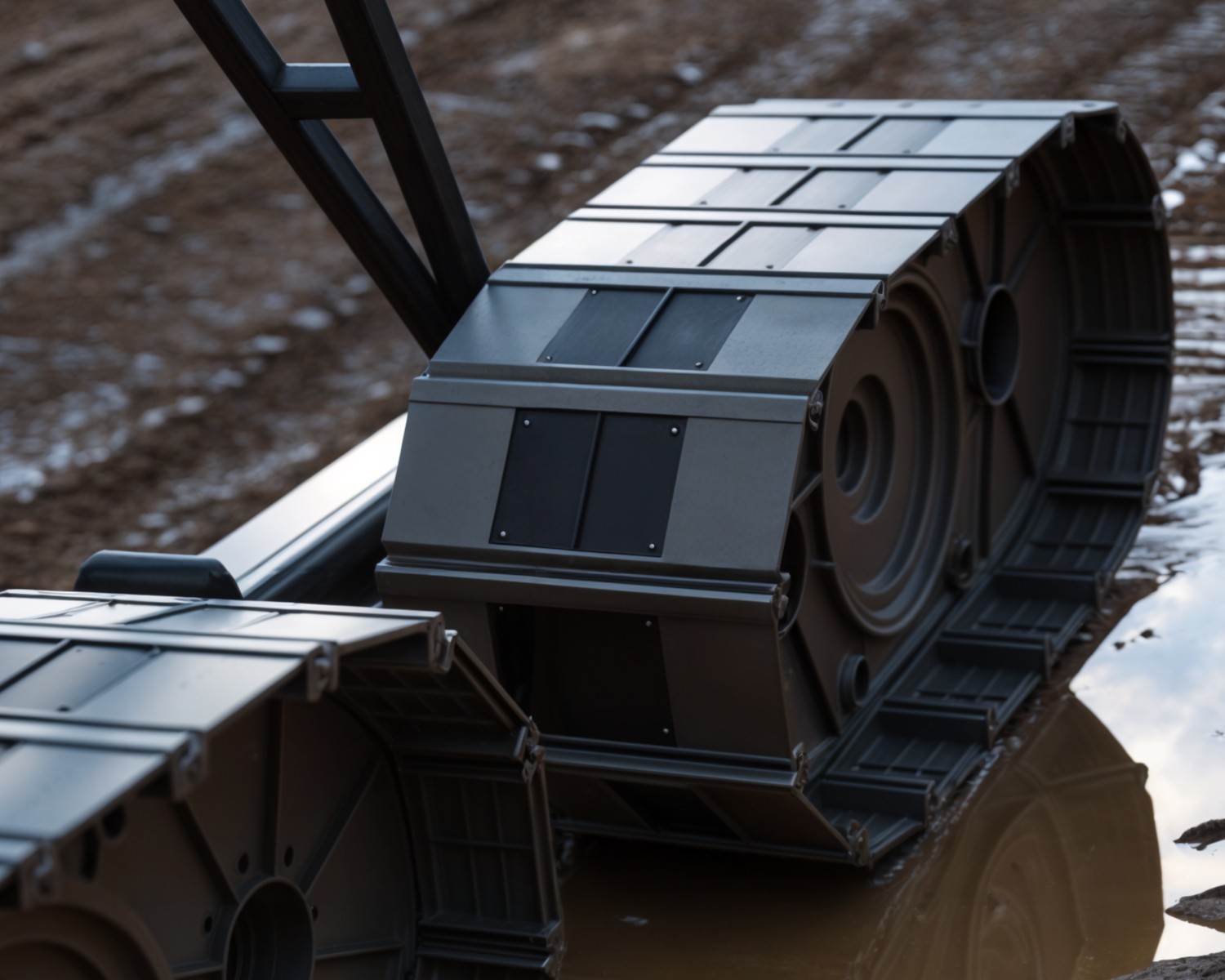
What the client said.
|