Durability is one of many categories to consider when your team is s developing a new product.
For many products, it’s right up there with production cost, ergonomics, and functionality in terms of importance.
But it can be tricky to get ruggedization right because the definition of ‘rugged’ is different depending on the user and the application. The product needs to withstand use in harsh environments. Or the product may need to be impact-resistant, incorporating rugged electronics. In some cases, the product needs to resist extreme temperatures and high pressure.
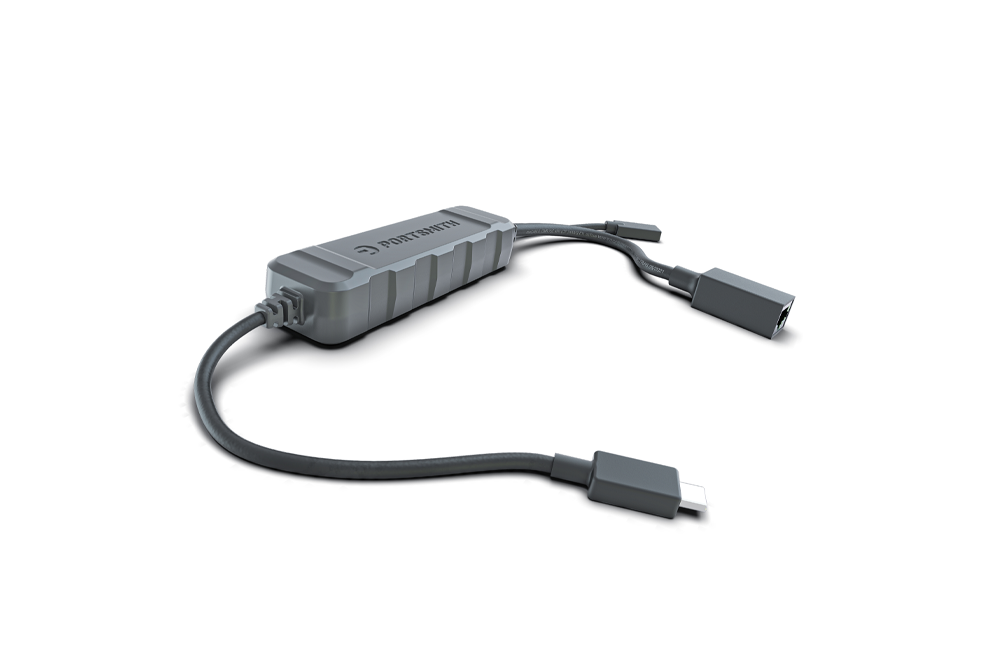
It’s important to understand exactly what will be “rugged enough” because adding more rugged design considerations than necessary can have a negative impact on production costs and the usability of the product.
Creating a rugged product usually means protecting parts of the product from specific aspects of the intended (or sometimes even unintended) use case.
A few examples:
- A user accidentally drops the product onto concrete – or the product is subjected to other types of impact
- The product is exposed to extreme temperatures or a wide temperature range
- Electromagnetic pulses may exist where the product is used or stored
- Possible exposure to weather, blowing dust, humidity variation
- Exposure to various types of radiation
- Exposure to corrosive substances
Each of these items (and countless others) require special consideration.
For some products, rugged design may focus on the enclosure — or product exterior. In other cases, the selection of specialty rugged electronics components will provide the durability needed. Many times, a combination of design approaches is needed.
Determine What “Rugged” Means for Your Targeted Use Case
The term “rugged” means different things in different markets.
A rugged design for an ag-tech product will have nothing in common with a rugged design for a hiking boot. And a rugged product for consumer use will have a different level of rugged design than a product used in an industrial setting.
Your product development team needs to have a deep understanding of what the term “rugged” really means for the people that will buy and use the product.
In consumer product development, the term “rugged” is typically used as part of a marketing message. As consumers, we don’t have a set of criteria by which we decide whether something is rugged or not. But we do have a set of expectations that a product will work reliably in certain use cases. So how does a product design team figure out what rugged really means to consumer users? Like so many things in consumer products, the secret is to ask and validate. Ask representative users what a rugged design will look and feel like. Then prototype it and have users test it to see if it performs as needed.
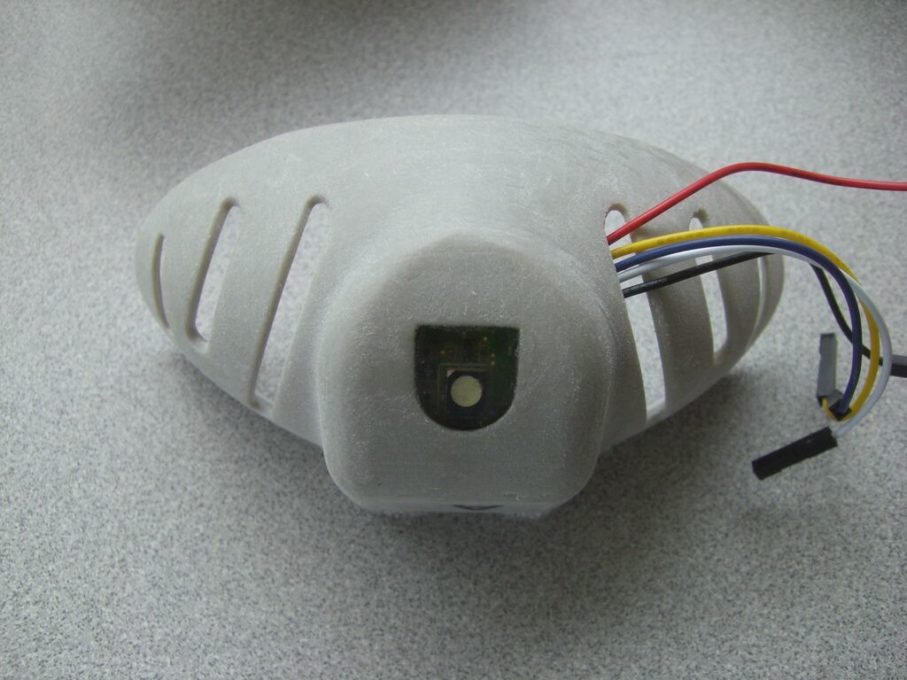
In industrial equipment or industrial product development, rugged design is defined by things like IP (Ingress Protection) ratings. As an example, let’s look at the standards for IP-rated design. To meet IP-69K, the product must:
- Be Dust Tight (6)
- Provide protection from Powerful high-temperature water jets (9K)
For military- / defense-related products, a specific set of standards and requirements for durability are well-defined. For example, MIL-STD 810 defines in a lot of detail the environmental conditions that a product must work in, and the testing that needs to happen to validate the rugged design. Some of the tests defined in standard cover:
- Low Pressure (altitude)
- Temperature (high and low)
- Fluid Contamination
- Salt Fog
- Acceleration
- Ballistic Shock
But what does it mean to “be dust tight”, “provide protection from water jets”, or “resist salt fog”? The design standards don’t tell us how to design a product that meets these criteria. But it does tell us the specific tests that need to be passed to meet the standard. With the tests in mind, an experienced development team can produce a design likely to pass the tests.
Rugged Design Considerations
Based on the preferences and standards that your product needs to meet, the design effort will focus on a few areas to achieve the right level of ruggedness. These four areas have a big impact on the overall durability of a product:
Materials Selection:
Selection of the right material for all critical components is perhaps the most basic step in rugged design.
- When designing a rugged injection molded part, choosing a material with a low durometer may add impact resistance, but it also may reduce abrasion resistance.
- Perhaps bent and welded sheet metal would add the right durability performance — but in high volumes, sheet metal enclosures may not be cost-effective.
- Material analysis is a balance between cost, manufacture-ability, and durability.
- Over-engineering a product by choosing ultra-durable material may be an easy way out, but also may add too much cost to the product.
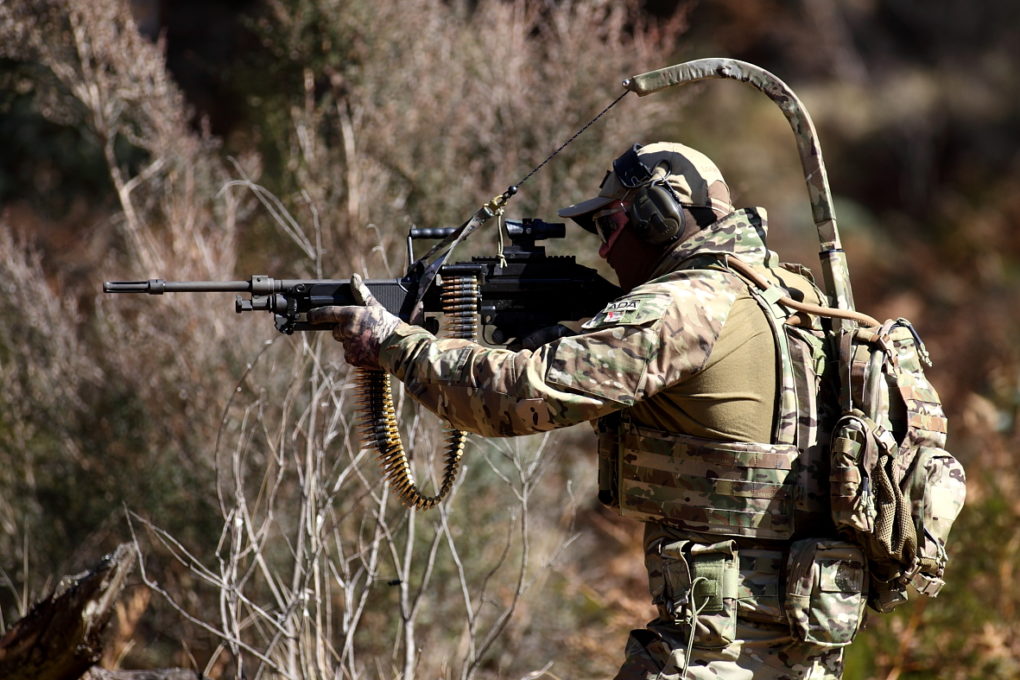
Electronics Design:
Component selection and PCB layout choices play a direct role in durable design.
- The board should be designed and mounted in a way that ensures impact loads aren’t transferred by the board itself.
- Critical components should generally be located inboard, or in a location with as much mechanical protection as possible.
- Potting the electronics can add impact resistance, but may create thermal management issues.
- And of course, the incorporation of specific shielding to meet the application’s standards is important.
Enclosure Design:
For electronics products, the enclosure typically provides the first line of defense for the internals.
- High levels of resistance to impact, vibration, and ingress can be achieved with over-molding or even double-over-molding the internals. For example, a PCBA may first be over-molded with a sealing thermoplastic, then that assembly may be over-molded with a shock-resistant material.
- Thermal management matters. Overmolding can induce stresses to the PCBA during temperature swings – such as in-process cooling. The forces can be high enough to pull components off the PCBA, causing product failures.
- The design team may find that the enclosure design solution requires specific manufacturing process considerations – such as increased dwell time in the mold to allow slower cooling, and therefore lower internal stresses.
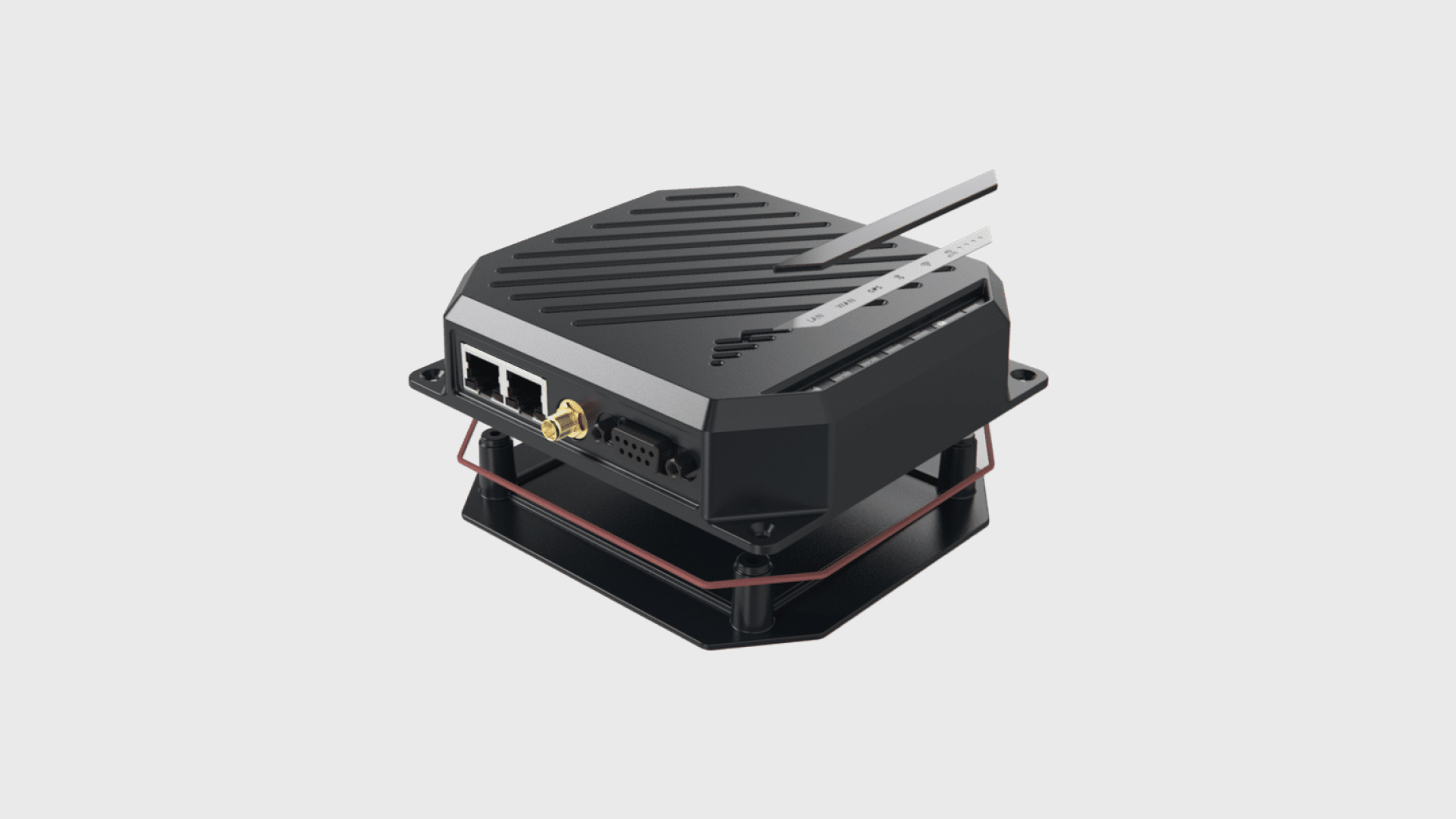
Mechanical Design:
Hinges, plugs, actuators, and other moving parts need special attention in rugged products. Good machine design and mechanism engineering principles apply here.
- Consider how parts will interact as temperature changes, as parts wear over time, and even when they are misused.
- One classic application of rugged mechanism design is firearms – look to classic firearms mechanisms for inspiration.
- Consider serviceability as a durability feature. For example, make parts that wear easy to replace. Make preventative maintenance easy so that it is more likely to happen.
- Clever mechanical design approaches will allow components to ‘self-clean’ as the system cycles, rather than allowing the buildup of dirt and grime.
Test, Tweak, and Test Again
Iteration is a development tool. It should be used in durable product design projects.
Engineers will apply theory and simulation during design to meet the durability requirements. But real testing uncovers the unexpected issues.
Use rapid development cycles and solid data capture techniques to iterate the product design for durability.
A healthy ecosystem of third-party testing labs exists to help with validation testing and planning. Take advantage of these labs – they have put a lot of capital into their test equipment, and the reputable ones are a wealth of information about the design specifications as well as the testing. But there are limitations to how much they can help.
As independent third parties, their primary goal is to objectively test your products, as opposed to ensuring your product passes their tests. People at the testing labs are experts in setting up the tests and running them. But don’t expect them to define which tests apply to your product, or how to pass them.
Sometimes products do not pass the third-party lab testing. This is a costly outcome for these reasons:
- Usually, this means the product must be redesigned and resubmitted for testing.
- Since this testing typically happens with the first production runs, product changes are expensive at this point.
- You will need to re-test the product, which means more time from your team, plus lab fees
As your development team becomes more accustomed to designing rugged products, they will develop a feel for which tests are harder to pass and which are easier.
For the riskier tests, it is smart to develop an in-house pretest process that mimics the actual lab test. This will help avoid failed tests at the lab.
Next Steps
- Determine whether your internal team has the bandwidth to take on rugged product design
- Task your development engineers with fully understanding the applicable design standards, testing standards, and market preferences that apply to your products
- Build relationships with third-party testing labs for final testing
- Build in-house pre-testing capabilities
- Consider getting help from an outside firm with experience in rugged product design
- Determine ‘what kind of rugged’ the product you’re working on really needs (marketing message, IP rating, MIL-STD, etc.)
- Get intimately familiar with the standards that apply – or if it’s a marketing message, get intimately familiar with what the user’s expectations and desires are (that will take the place of a standard).
- Come up with your test plan, and then work backward into your product features: which features are the ones that deliver (or hinder) alignment with the standard identified?
- Consider engaging a rugged product design firm to make sure this is all done right.