Improved AR Bolt Engineering
Designing an improved bolt for the AR platform, that reduces jamming by making the system less sensitive to carbon buildup.
Sharps Rifle Co
Firearms Engineering, Finite Element Analysis, Mechanical Engineering
2014
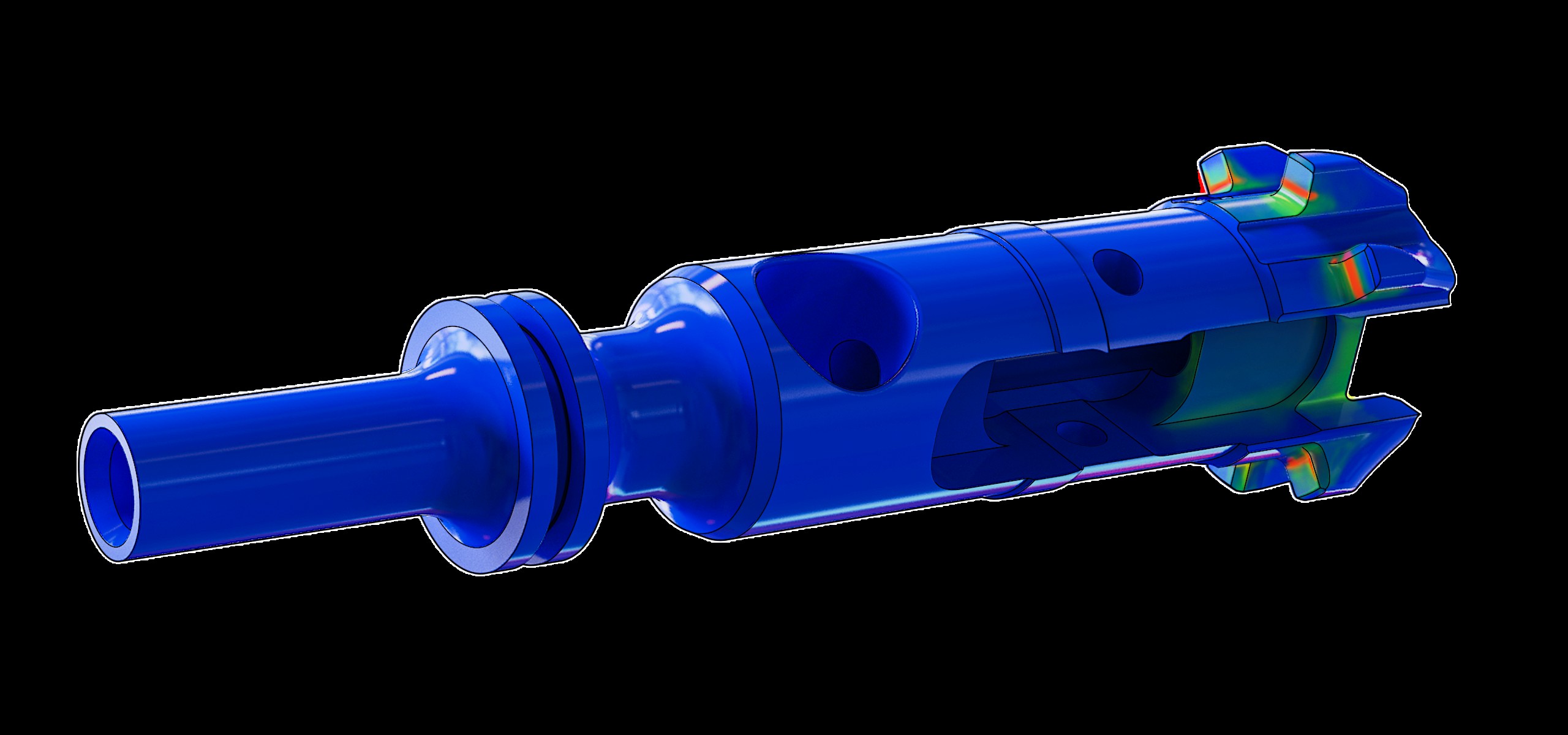
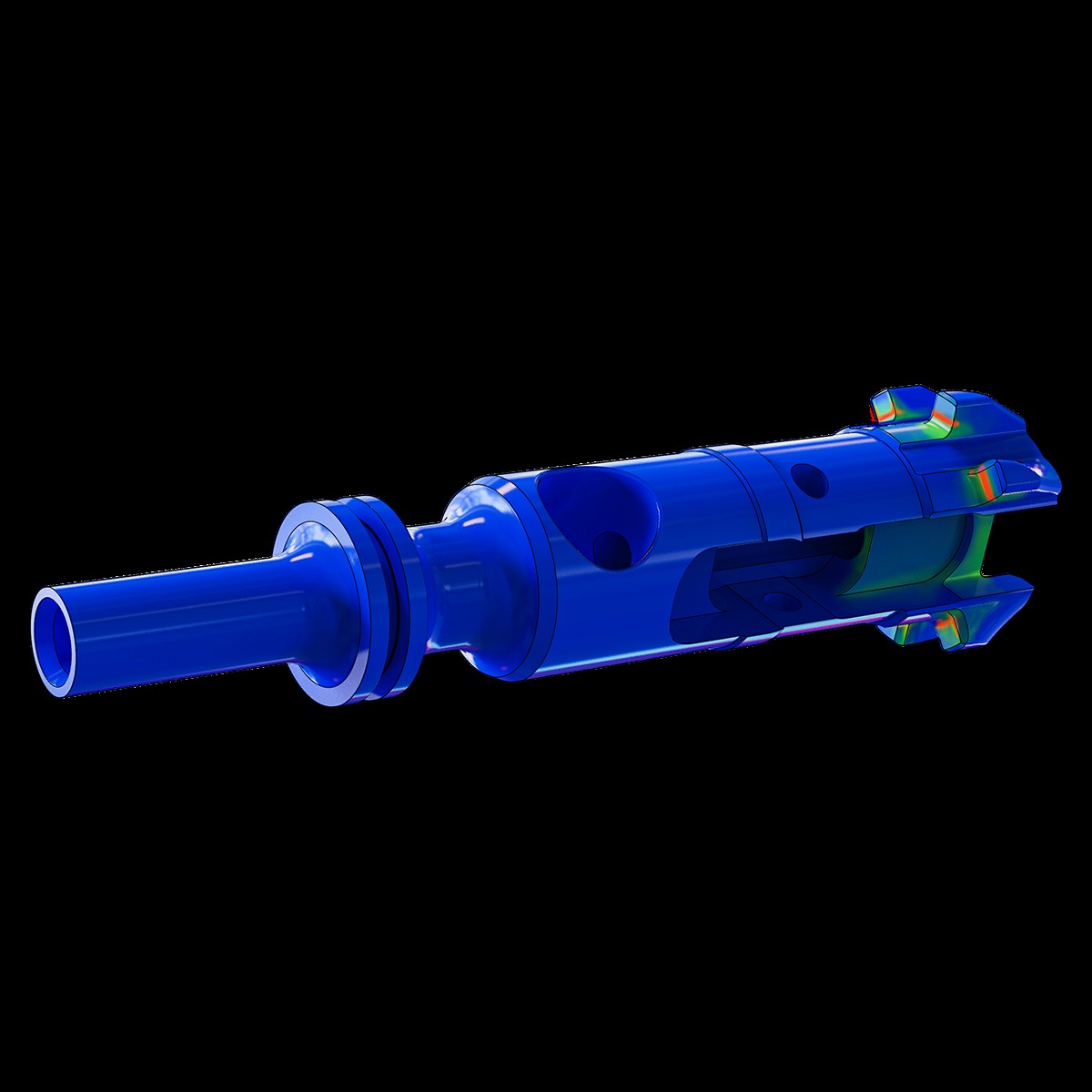
Sharps Rifle Co hired SGW Designworks to: 1) Develop lug geometry for the bolt that would tend to push away powder residue, 2) Ensure that the new lug geometry would withstand the extreme forces in prolonged, repetitive use.
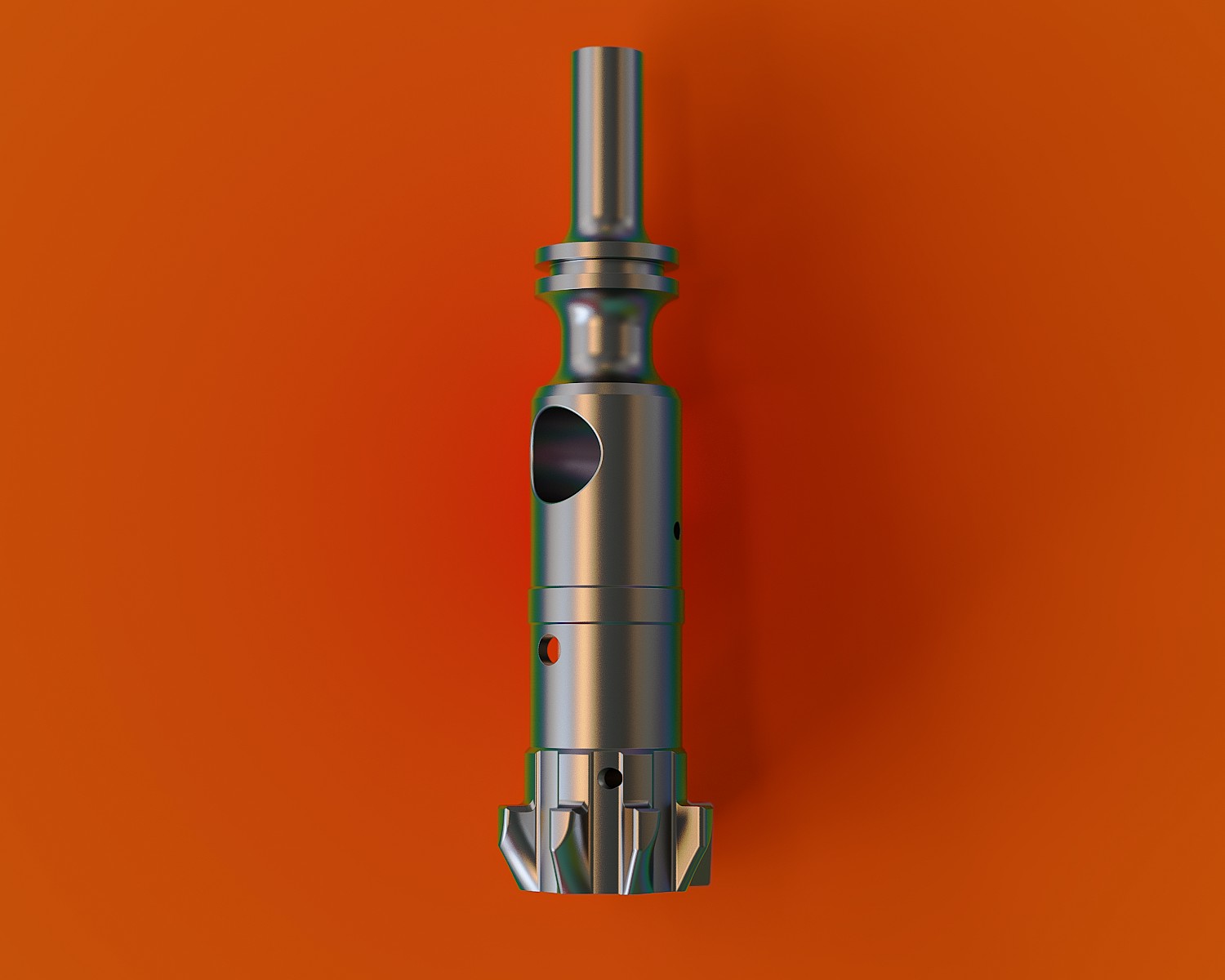
Developing an Improved AR Bolt
Sharps Rifle Co was interested in offering an improved AR bolt that would improve system reliability by providing reducing sensitivity to carbon buildup at the bolt / barrel extension interface. Because of the extreme forces involved and the need for absolute functional certainty, Sharps hired SGW Designworks to make it happen.
Sharps Rifle Company is a brand with history dating back to 1848 when the original Sharps Rifle was patented. Though the brand has changed hands over the years, the market still expects quality and innovation from Sharps products.
The team at Sharps Rifle Company reached out to SGW Designworks because they had a vision for a product, but needed help making it real. Sharps wanted to develop a new bolt design that would reduce the likelihood of jamming and failure to fire due to carbon / grime build up at the interface between the bolt and the barrel extension. They believed that new lug geometry could be designed that would tend to displace the powder residue, and operate effectively even with significant buildup present. But any change to typical lug geometry could impact the bolt's ability to resist the massive forces endured when firing. The design would need to strike a balance, and extensive engineering analysis using state-of-the-art tool s would be required to get it right.
Design Iteration, Deep Analysis, and Design Finalization
The SGW team defined a disciplned approach to design development for the bolt. This included concept development, initial engineering analysis, Finite Element Analysis, prototyping, testing, and design finalization for production.
SGW Designworks has a long history of firearms related development projects. The team is familiar with how firearms products are used, manufacturing norms in the industry, firearms development testing protocols, and engineering best-practices for firearms design. This means the team was comfortable stepping in to execute this AR bolt design effort.
Initial work focused on possible geometries for the lugs. The team was able to define geometry that would in theory function as desired without requiring changes to the barrel extension geometry. This is important because while any AR owner can swap out a bolt, changing out a barrel extension requires special tools that most owners do not own.
With the geometry defined, engineering analysis would begin. The SGW team started with a full metallurgical analysis of benchmark bolts from top tier manufacturers. This allowed the SGW firearms engineers to calculate the actual load carrying capacity of standard lugs. The engineers then went through conventional analysis as well as Finite Element Analysis to compare the standard geometry with the proposed improved geometry. On top of this, the team calculated the actual forces experienced by the lugs in action, using SAAMI pressure data for the specific cartridges specific by Sharps. Of course, manufacturing tolerance comes in to play as well for this analysis, since dimensional variation can lead to loads being distributed across fewer lugs. The SGW team identified acceptable dimensional tolerance ranges for the bolt, as well as heat-treating call outs that would be incorporated in to the final production drawings.
Sharps Rifle Company successfully launched the ReliaBolt, and the product has gained traction in the market. SGW also designed a Low Mass Bolt Carrier for Sharps in a subsequent project.
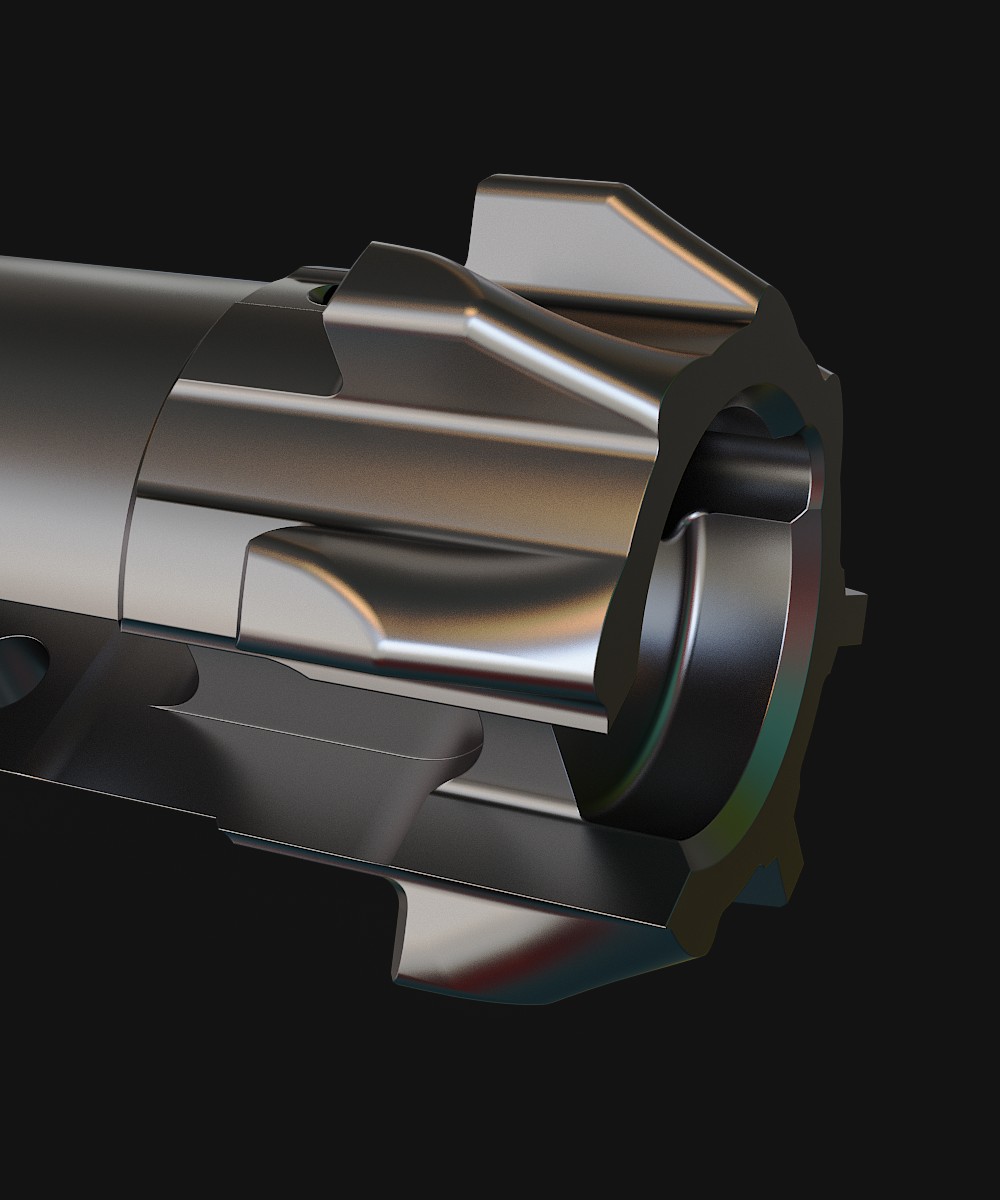
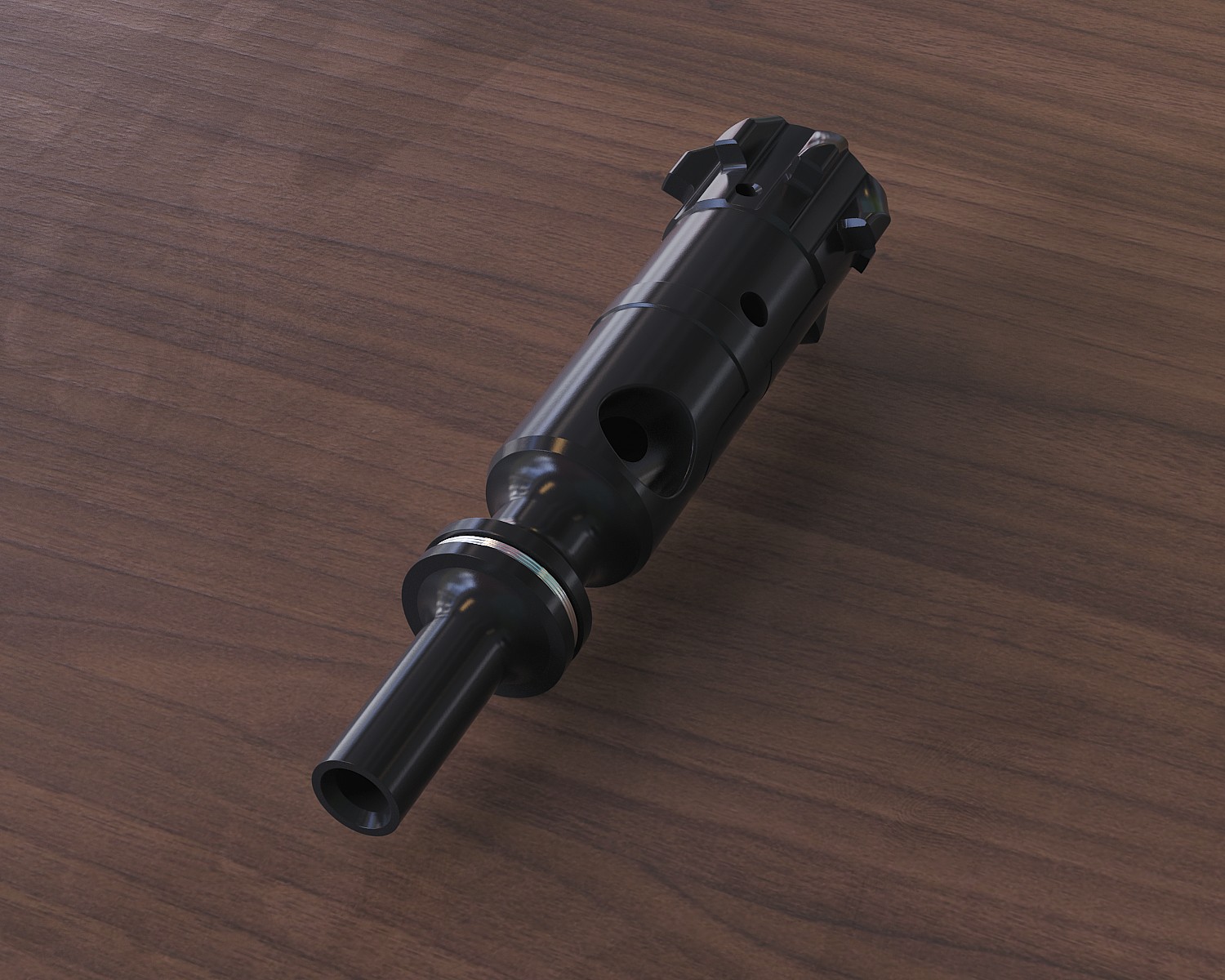
What the client said.
|