Well-designed products make us happy.
The feeling of holding a product and immediately understanding what it is and how we can use it is satisfying. Even more satisfying: having played a part in the process of designing something well and understanding the amount of work it takes to turn a sketch into a real product.

So what exactly makes a well-designed product — and what does building it entail? Here are some key criteria.
Well-designed products are clearly defined at the beginning.
The tendency of designers is to build something. We are supposed to build prototypes, right?
While prototypes are excellent for flushing out a product, the first step in the process must be to clearly define what it is being developed. It’s helpful to ask such questions as, What are the constraints? Size? Environment? Budget? Cost of goods sold? What is its purpose? How do you know when you have developed the correct ‘thing’?
At SGW, we refer to this as Phase 0. This is where we take an idea, clarify what will be developed, and consider practical pathways forward. What is feasible given the constraints, requirements, development budget, and available resources (personnel or equipment)?
They require adequate resources and budget.
Product development is an expensive endeavor. It involves costs related to engineering, prototyping, regulations and testing, tooling, pre-manufacturing, initial manufacturing runs, and supply chain and storage. And this is all before getting the first products ready for the shelf.
Because these realities could present limitations, they need to be accounted for when setting out to develop a product.
Well-designed products require adequate testing, iteration, and validation.
Prototyping is not a one-and-done approach to building a product. To illustrate, the Black Box VR Gym went through six complete and separate system builds, each including a number of smaller sub-system prototyping and testing. In order to ensure a favorable user experience, it was important to iterate with different motors, servos, pads, and shapes.
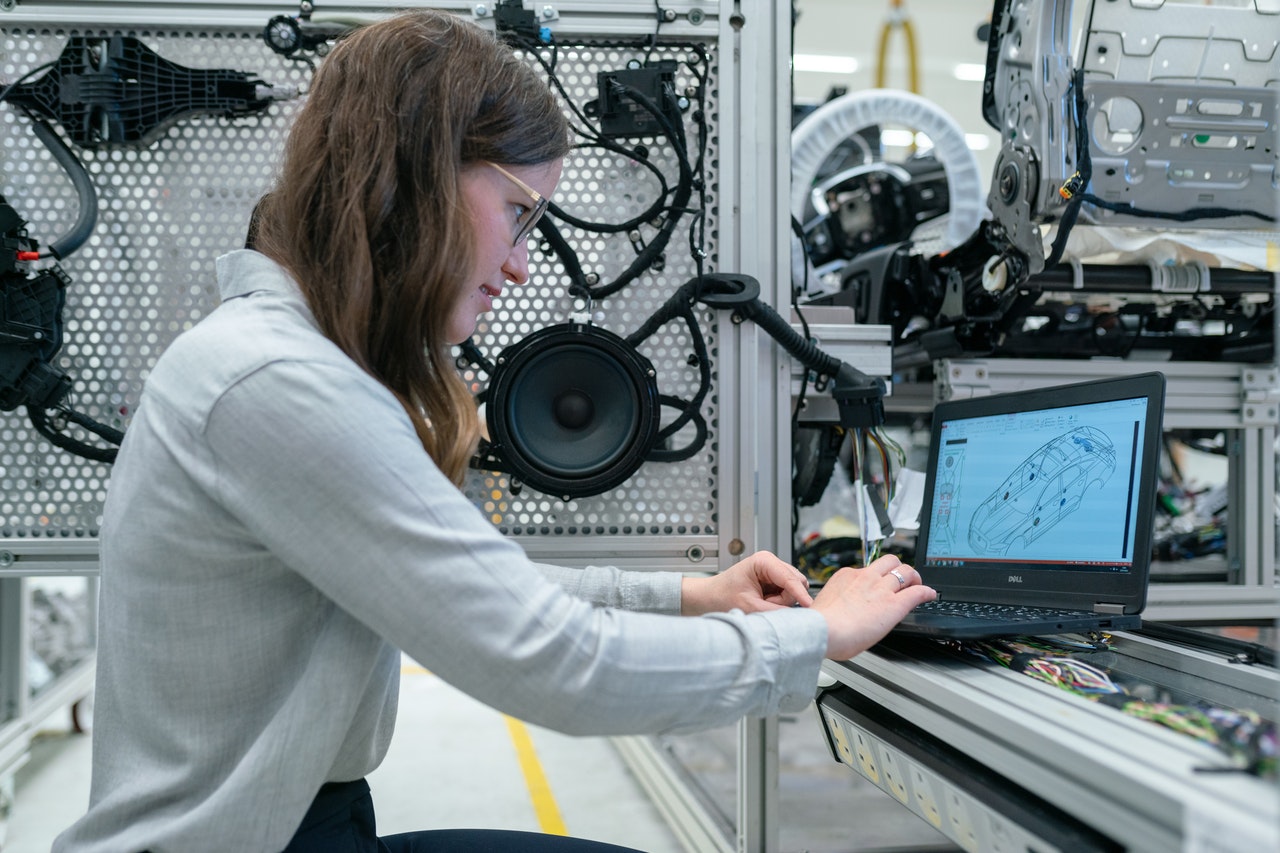
Additionally, GIR’s Voltaire Smart Grinder was subjected to six complete system builds with additional prototype iterations. The purpose? Testing various sub-systems and components.
In the case of Dyson, one product famously had 5,127 prototypes. There are many different types of prototypes and reasons to prototype features, fits, etc.
Well-designed products require a clear stopping point.
We must finalize a product at some point in order for it to be considered ‘well designed.’ Beware the pitfall of perpetual improvement. The product requirements document generated in Phase 0 should be an indicator of when a product has reached a place where the product needs to be launched.
Does your company need help assessing a product before investing a lot of capital? Give us a call and see how we can aid your company in the development process.