Thank you! Your submission has been received!
Oops! Something went wrong while submitting the form.
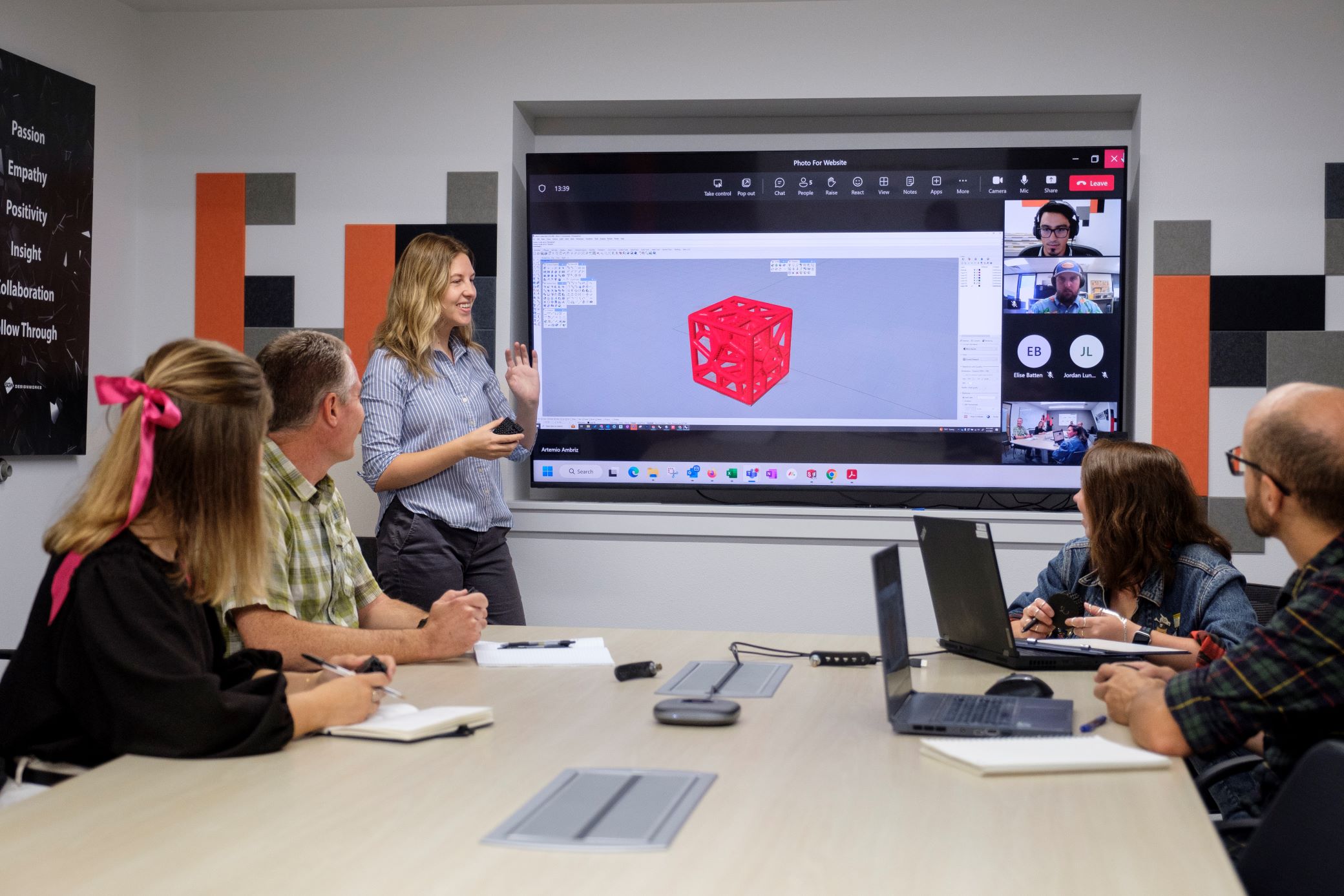
Product Design for Manufacturing: Streamlining for Efficiency and Cost-Effectiveness
How to plan and effectively design a product for manufacturing.
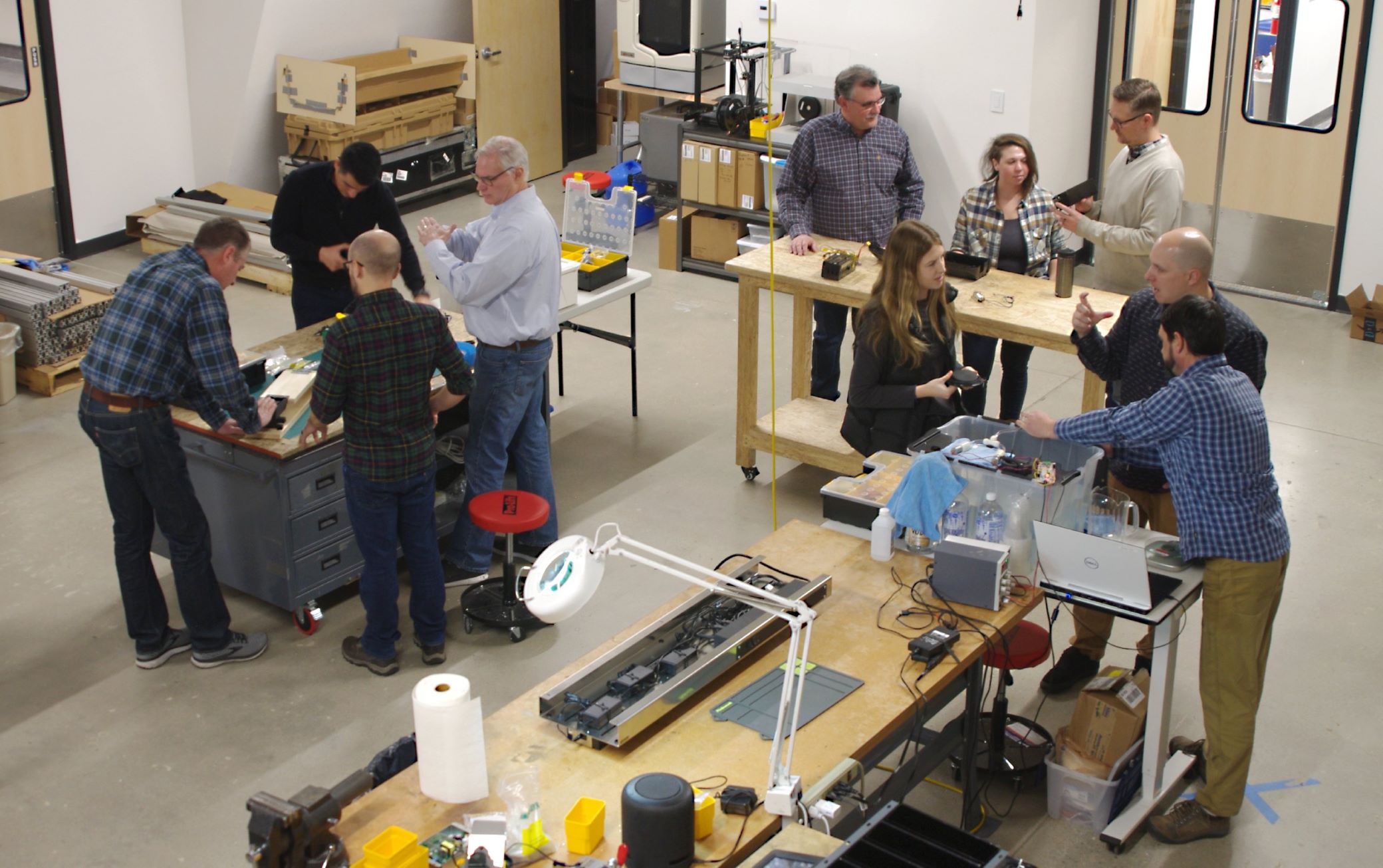
What Is the Engineering Design Process? An In-Depth Guide to Crafting Innovative Solutions
What Is the Engineering Design Process? Learn what it takes to get from concept to prototype.
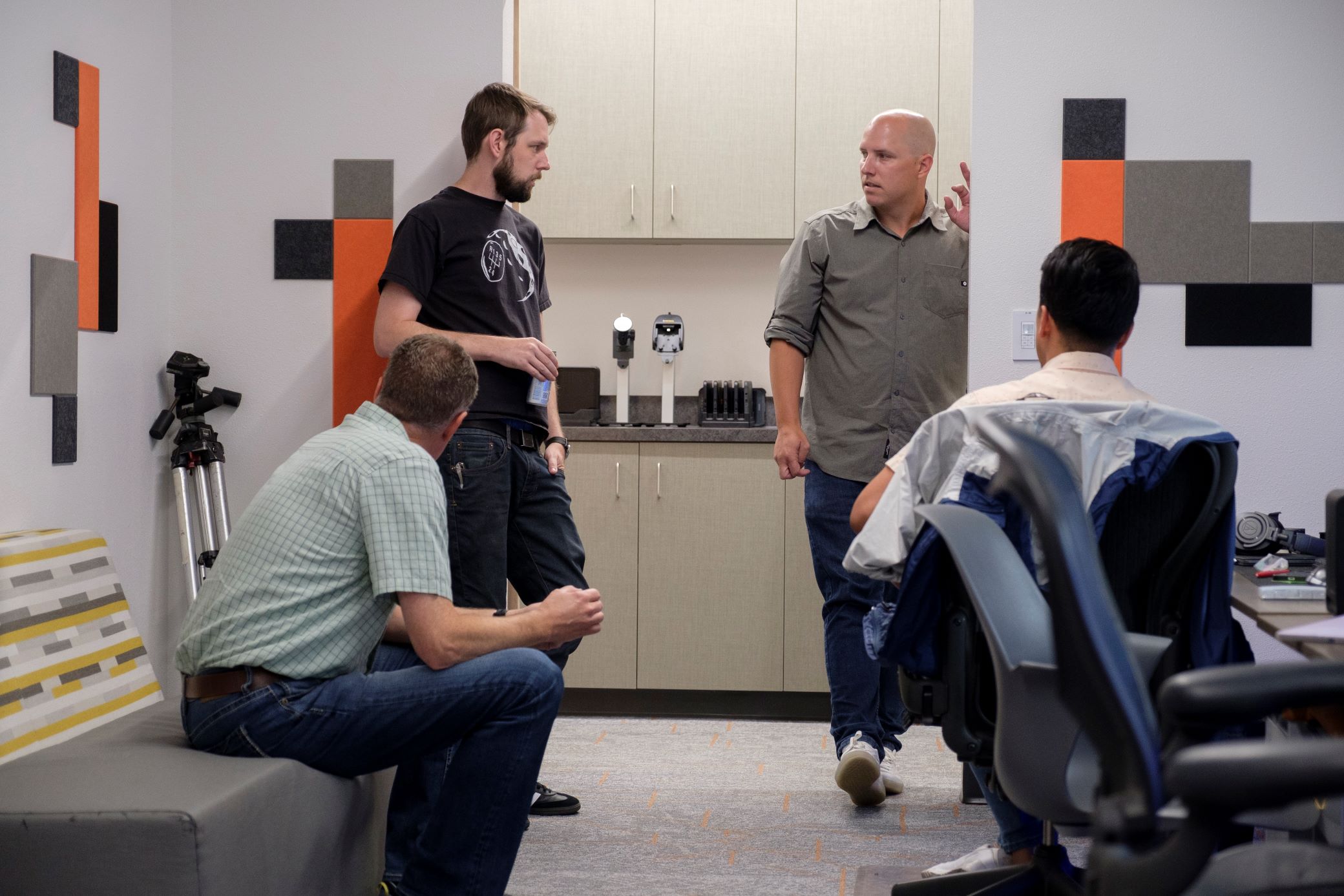
The Benefits of hiring the right Professional Engineering Consultants
What does it take to find the right engineering consultants for my product? Read to learn more.
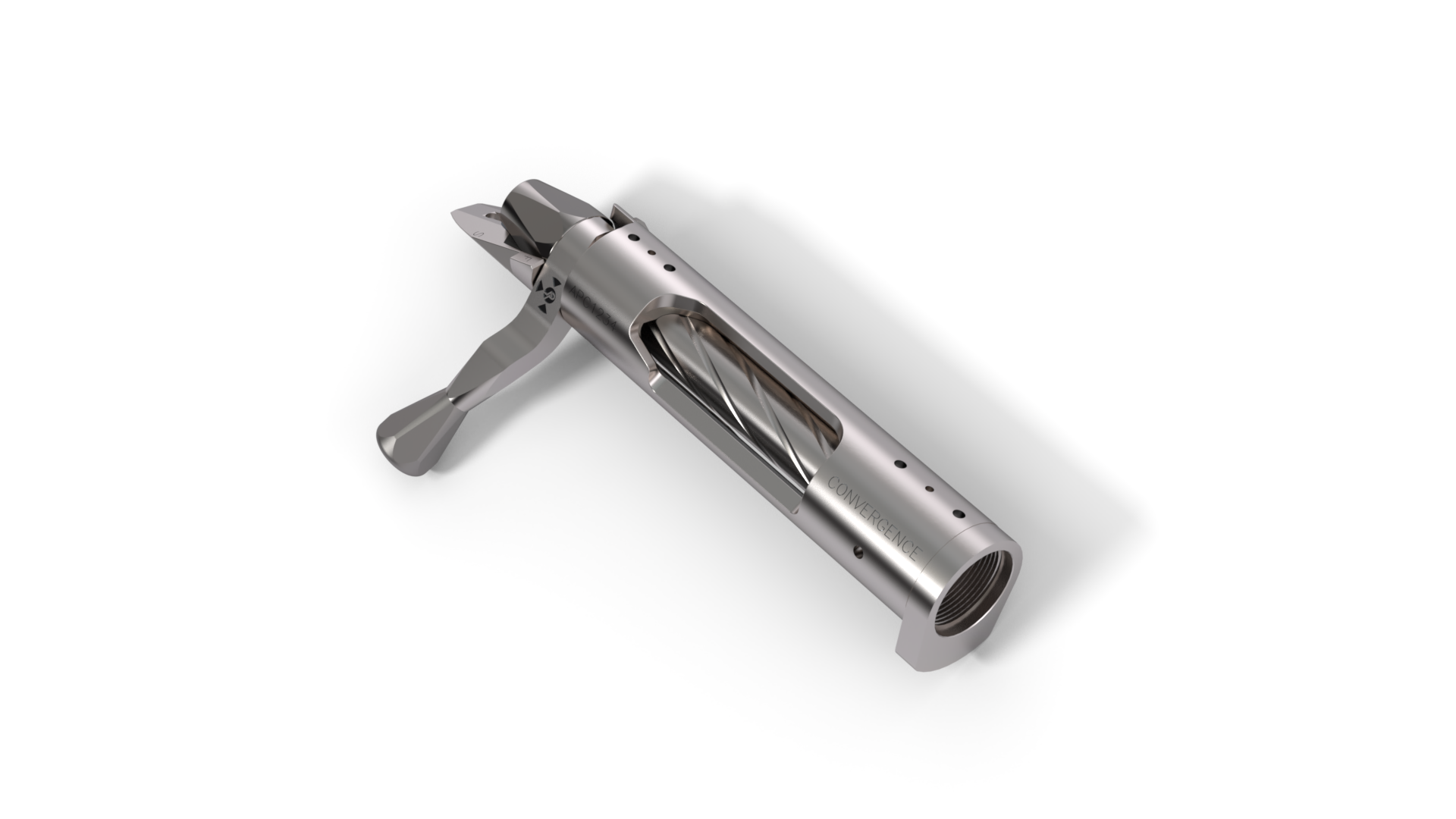
Precision Engineering Meets Innovation in Firearms Development
The unique considerations in firerams design projects, and the types of firearms projects SGW Designworks takes on.
Industrial Design Company: Creating Innovative Products for Modern Needs
Industrial Design Company: Creating Innovative Products for Modern Needs
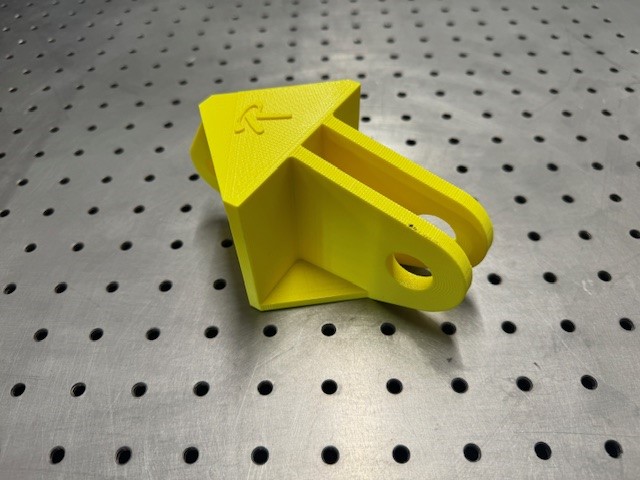
Prototype Development Services: Streamlining Your Product Development Process
Prototype Development Services: Streamlining Your Product Development Process
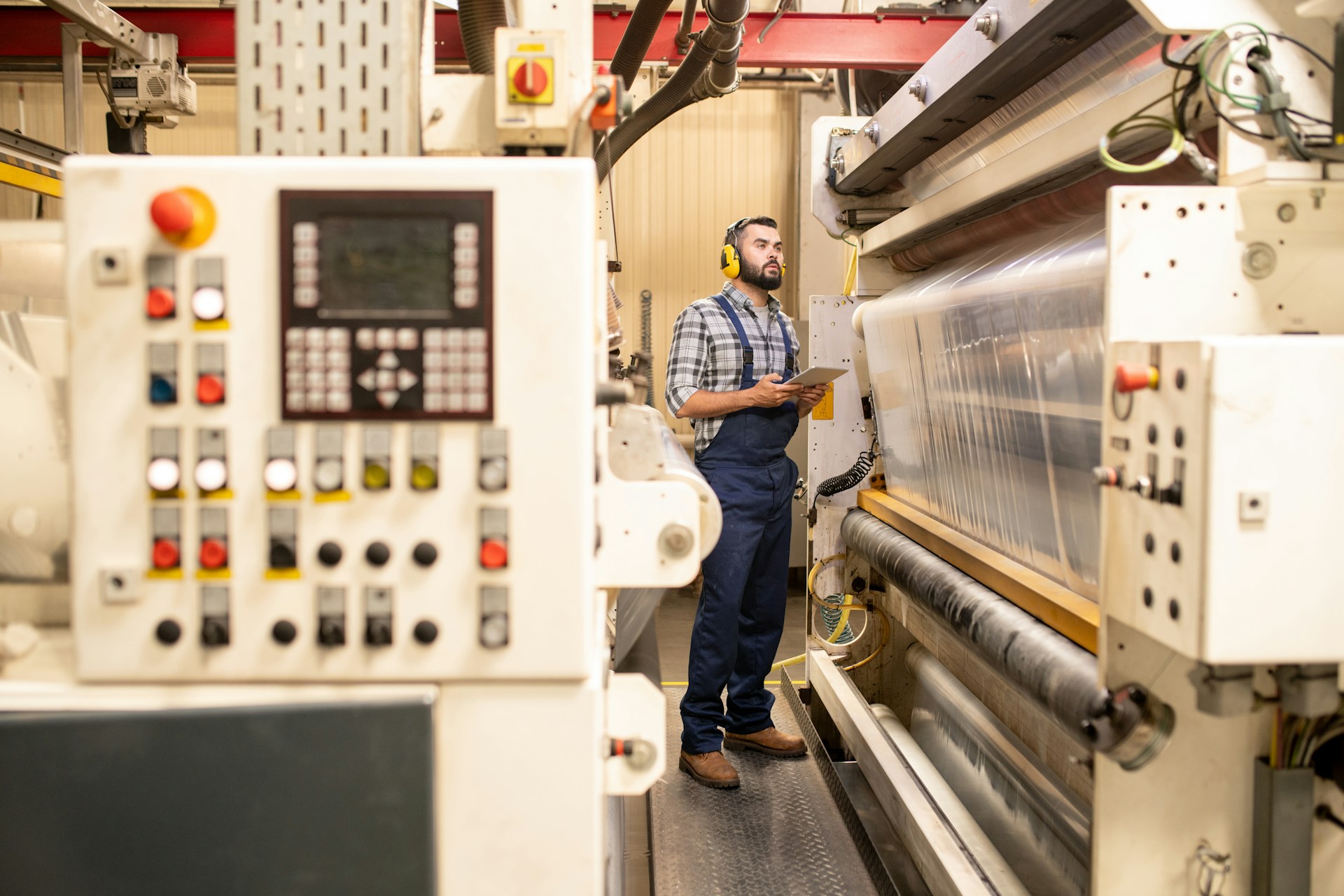
Design for Manufacturability: Streamlining the Production Process
Design for Manufacturability: Streamlining the Production Process
.png)
How to Get Your Product from Concept to Market in 9 Steps
How to Get Your Product from Concept to Market in 9 Steps:
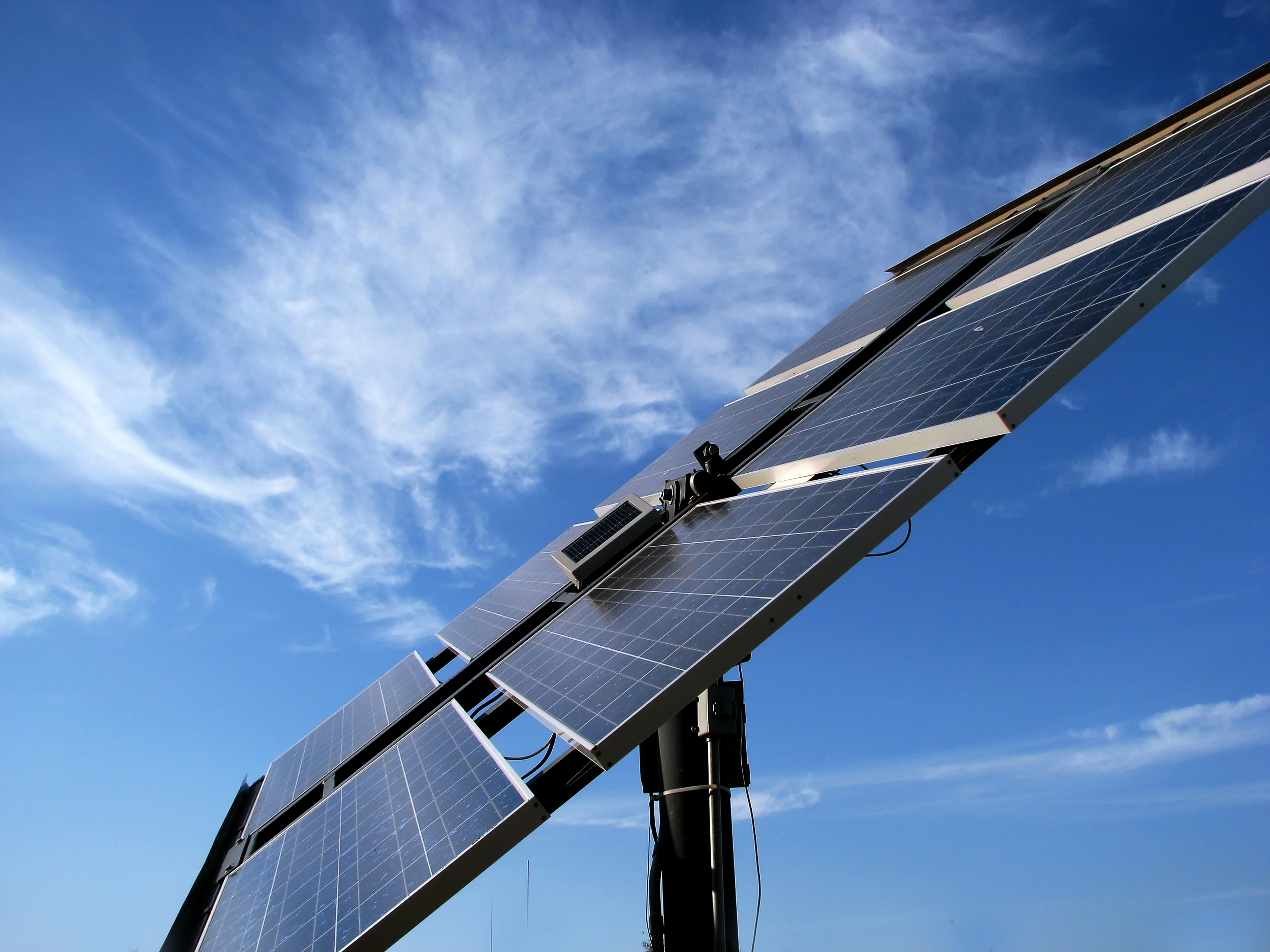
3 Important Factors in Solar Product Development
There has been a surge of interest in solar product development in recent years, driven by the growing demand for sustainable energy solutions.
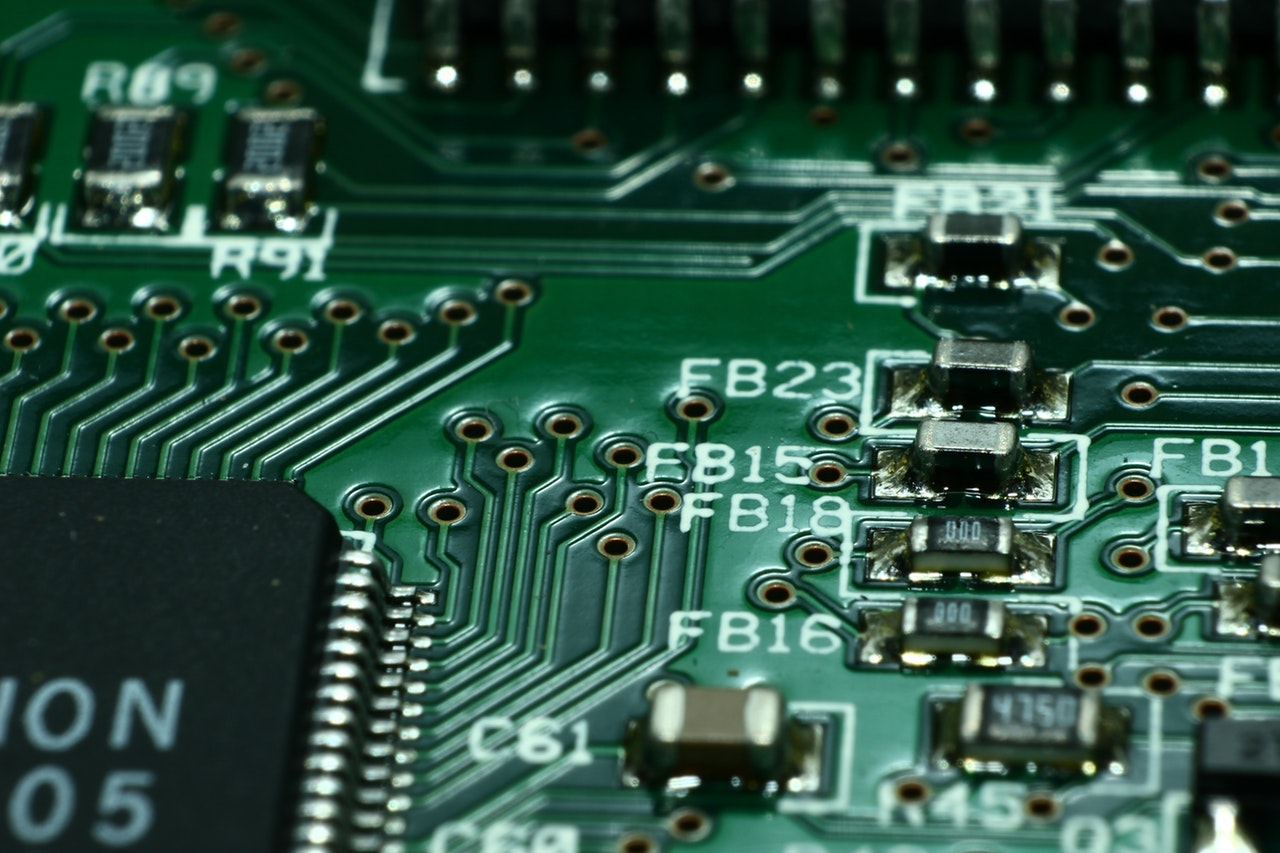
Electronic Product Design — and the Technology That Makes It Possible
As time goes on, more products are designed with integrated electronics to provide specific functionality or connectivity.
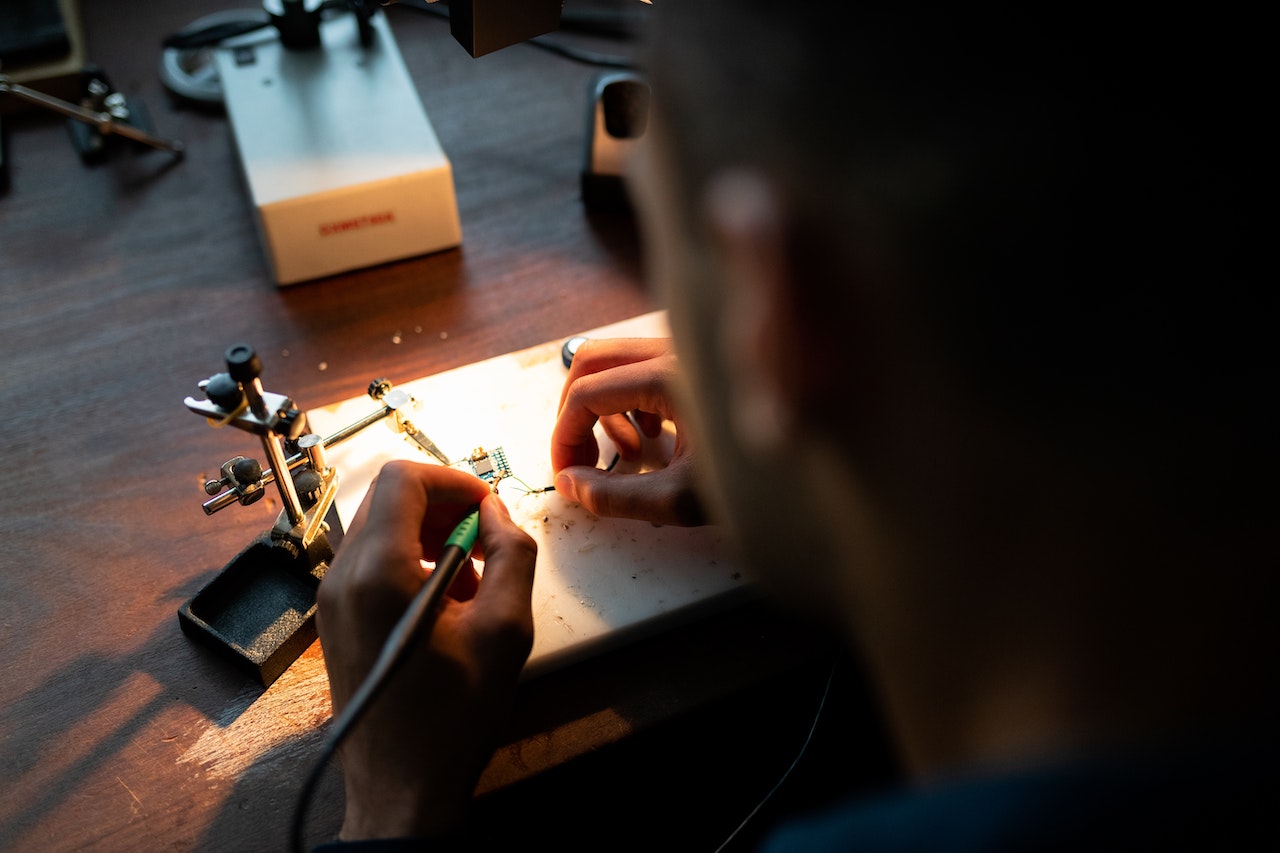
Pros and Cons of Outsourcing Physical Product Development in the U.S.
There are advantages and disadvantages of outsourcing physical / hardware product design and development to a U.S.-based company.
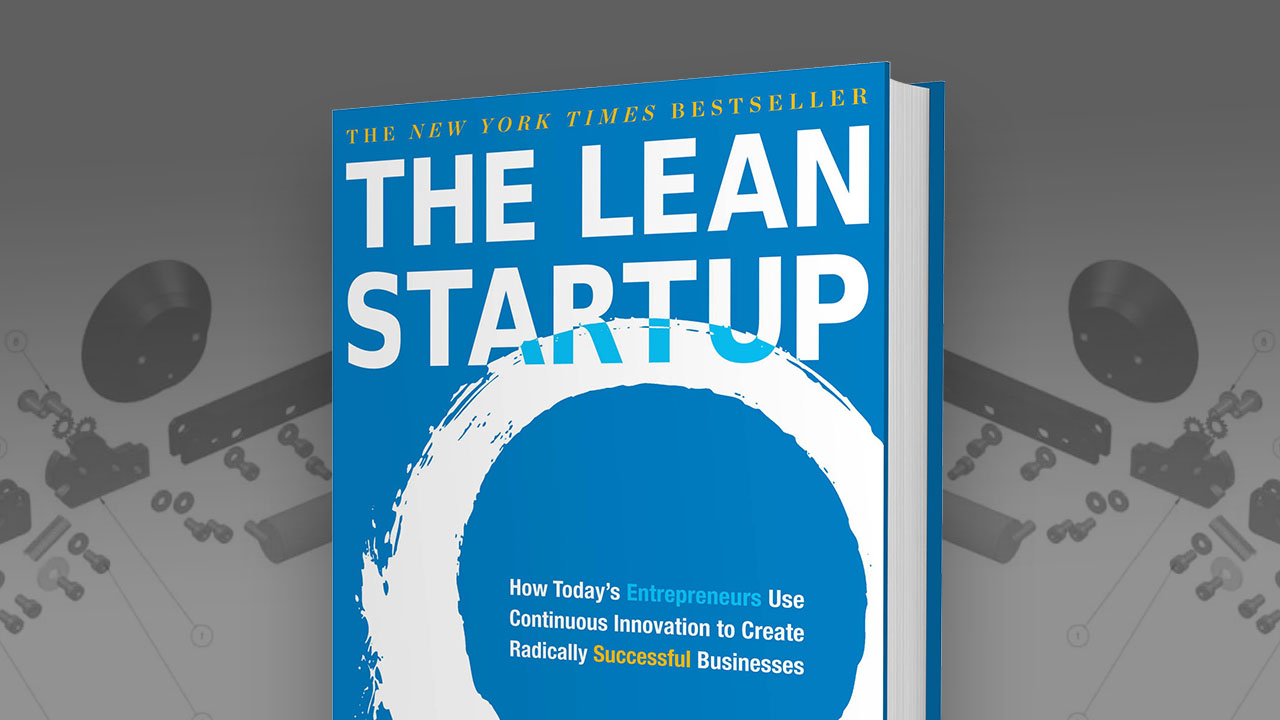
Lean Startup Principles for Hardware Development
True startup productivity requires systematically figuring out the right things to build.
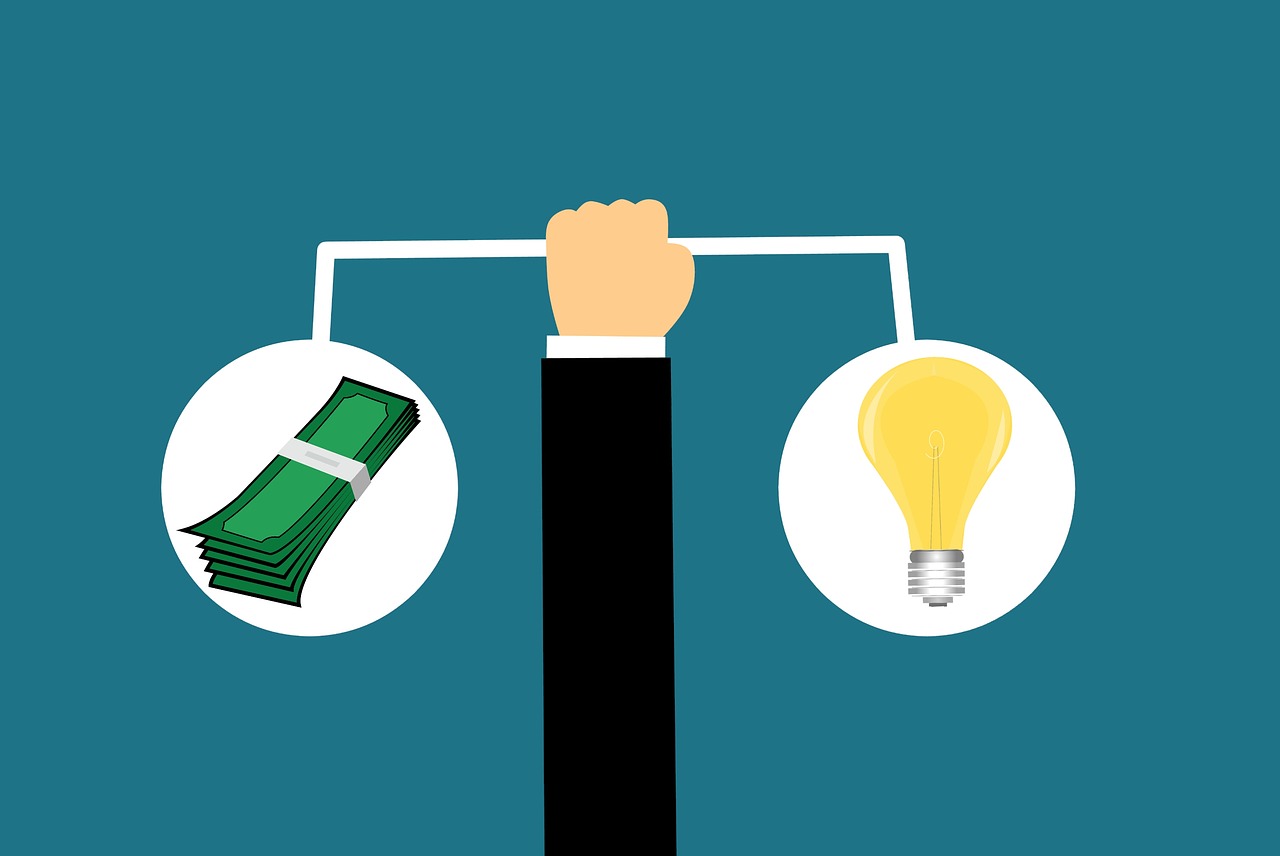
How Product Development Budget Affects a Project
Talking about budgets — and in this case, a product development budget — can be uncomfortable.
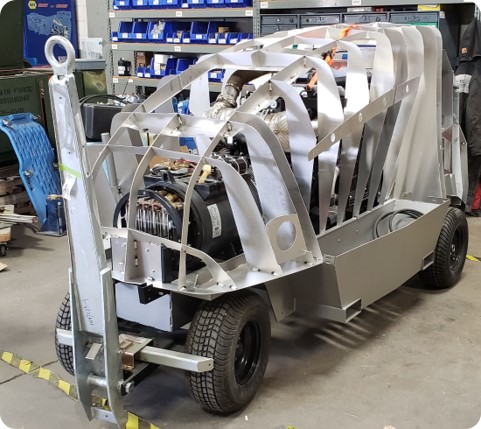
The Cost of Prototyping a Product
To determine the cost to develop prototypes of manufactured products, consider these questions.
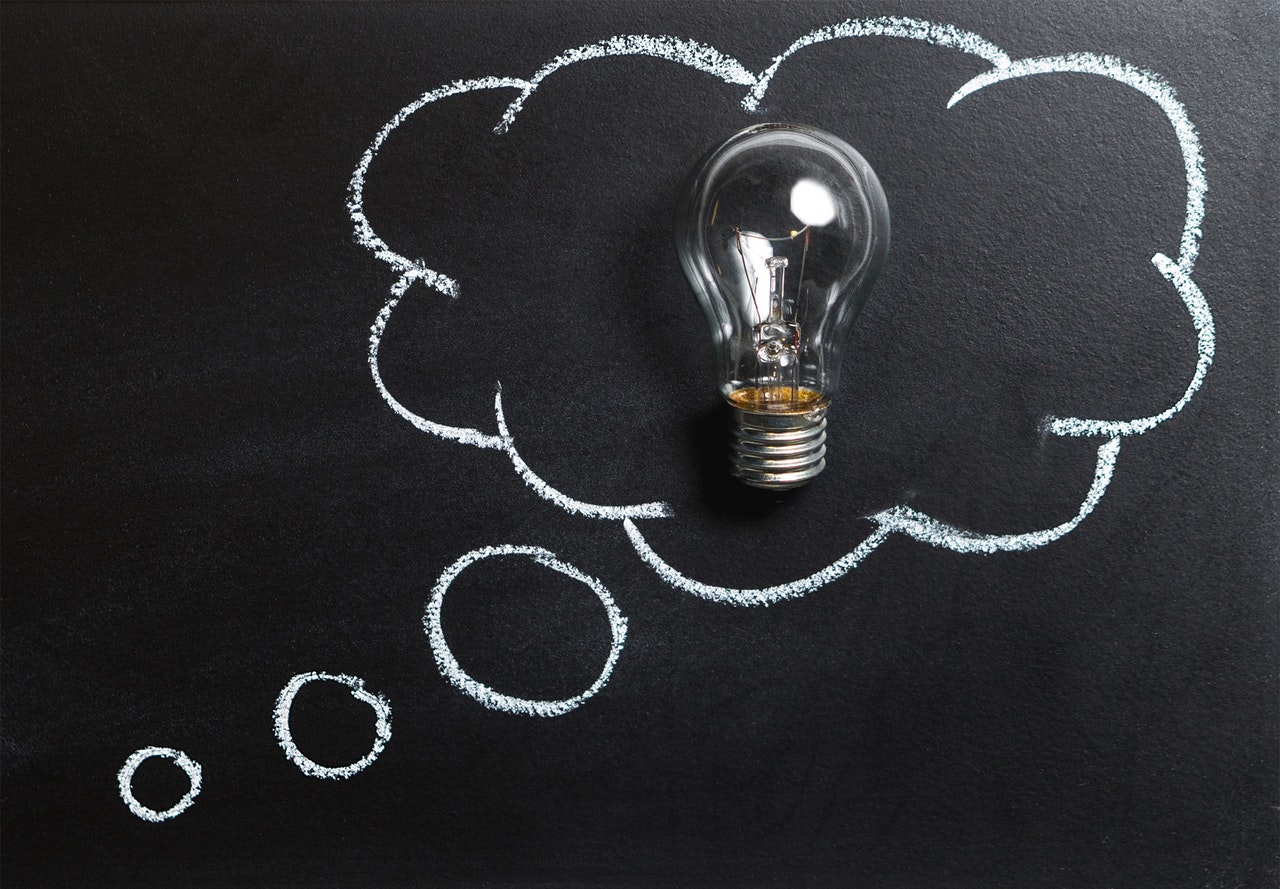
Prototype Development: The 4 Levels to Consider
Different levels of prototyping are appropriate at different stages of development. These are the four levels of product development before reaching a final product.
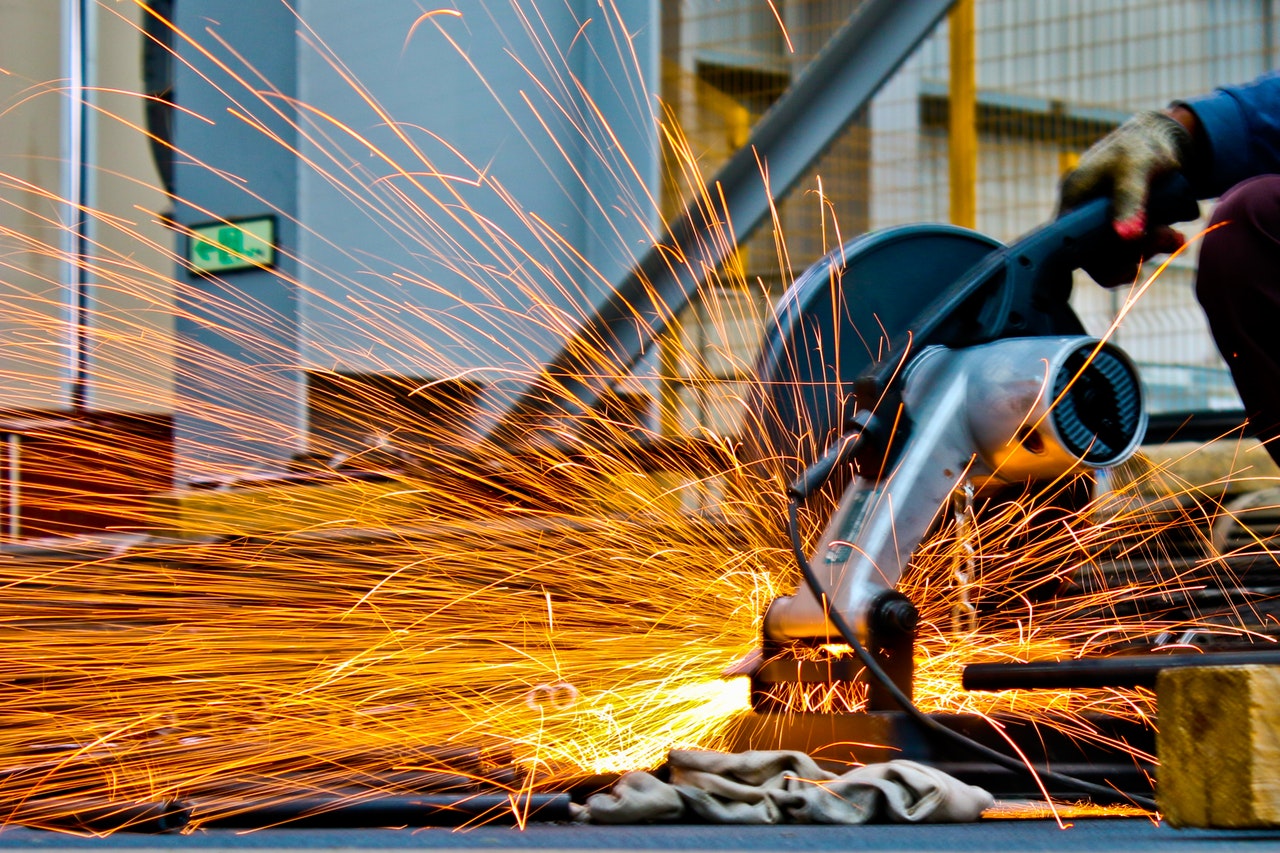
10 Machine Processes Used to Create Product Prototypes
Here's a list of several machine shop tools and processes that we as product developers employ.
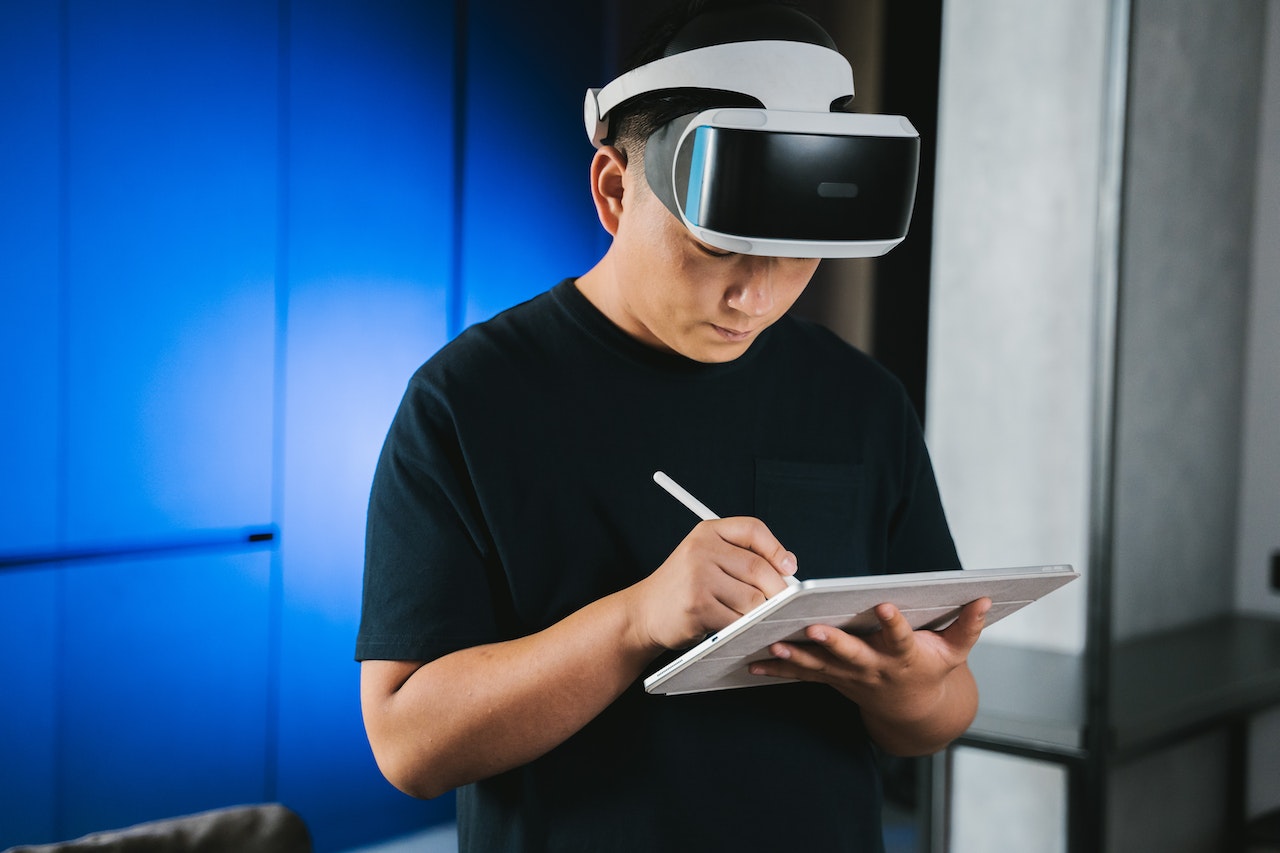
Virtual Reality Prototyping Can Save you Thousands of Dollars
When you hear the term virtual reality prototyping, do you instantly think of gaming?
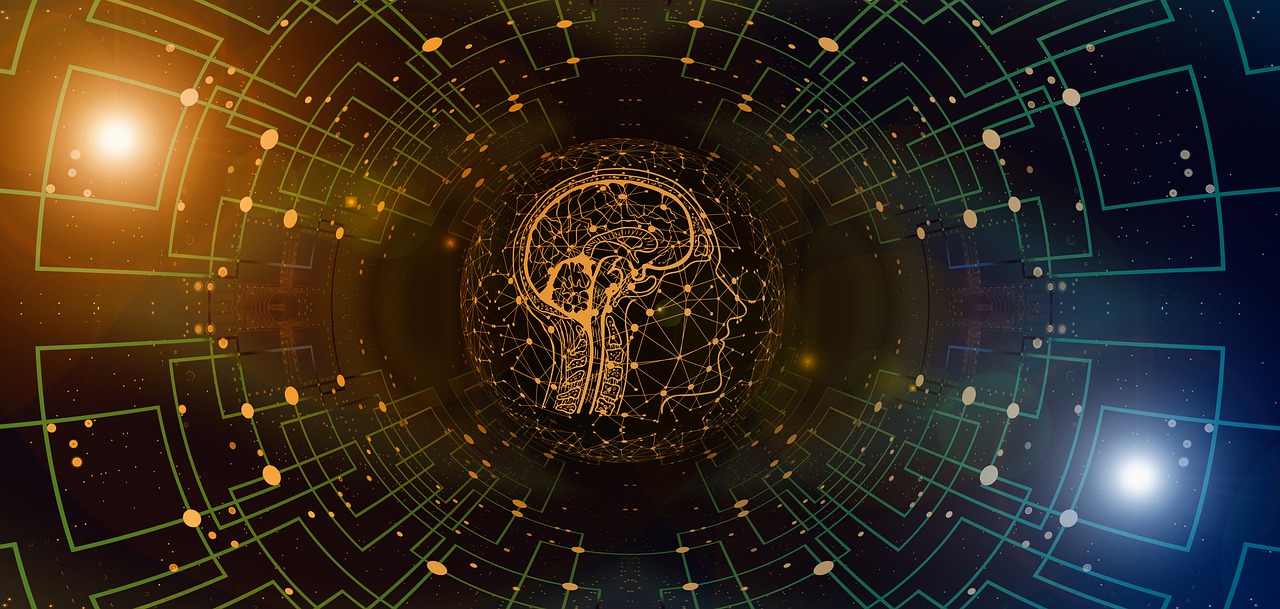
Why UI/UX? Best Practices for Successful Product Development
From the smartphone in your pocket to the vehicle you drive, great products don’t just happen.
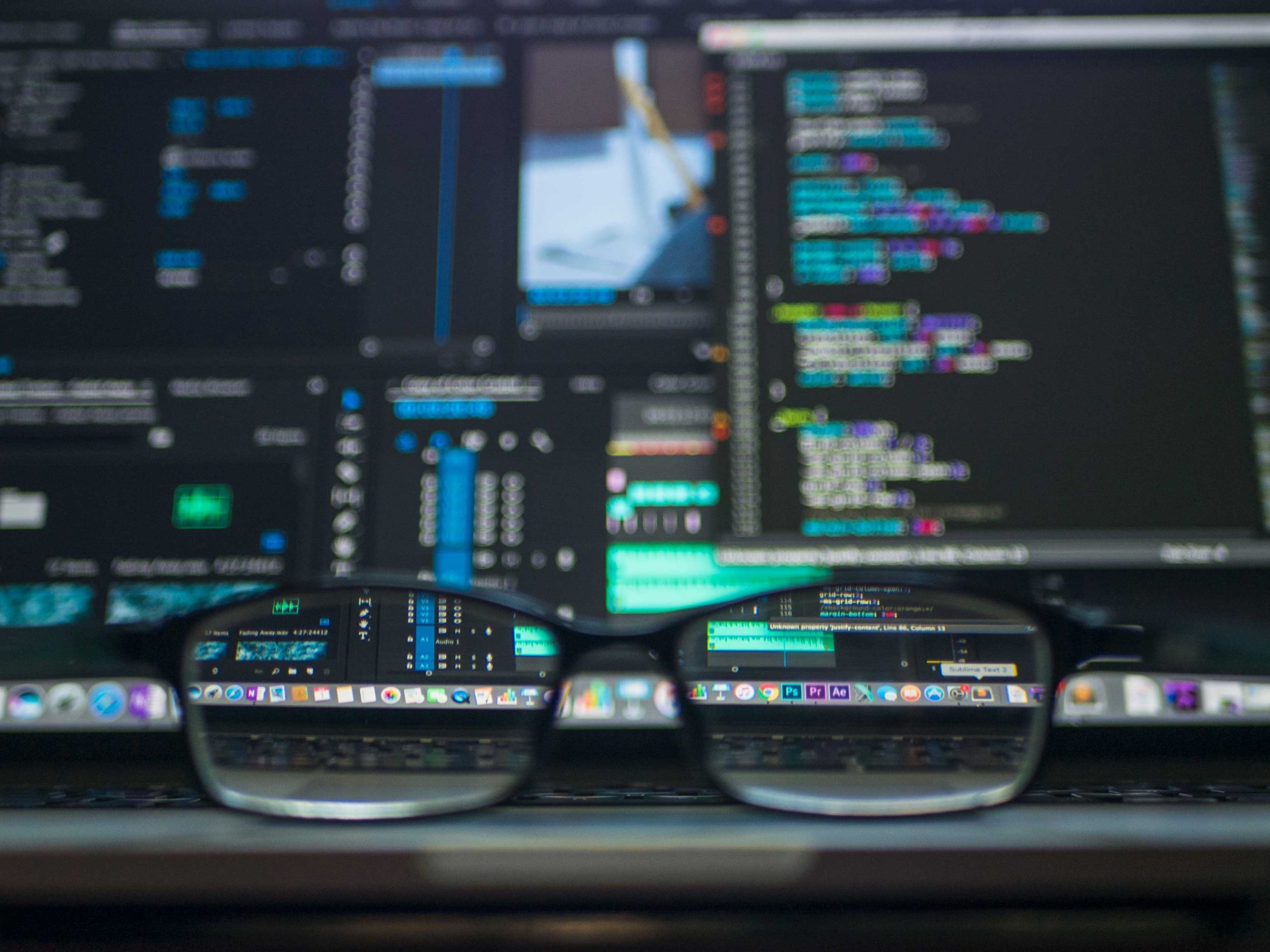
Developing a New Electronic Product in 2023? Avoid These 3 Common Firmware Engineering Problems
The market for connected products and IoT devices continues to grow.
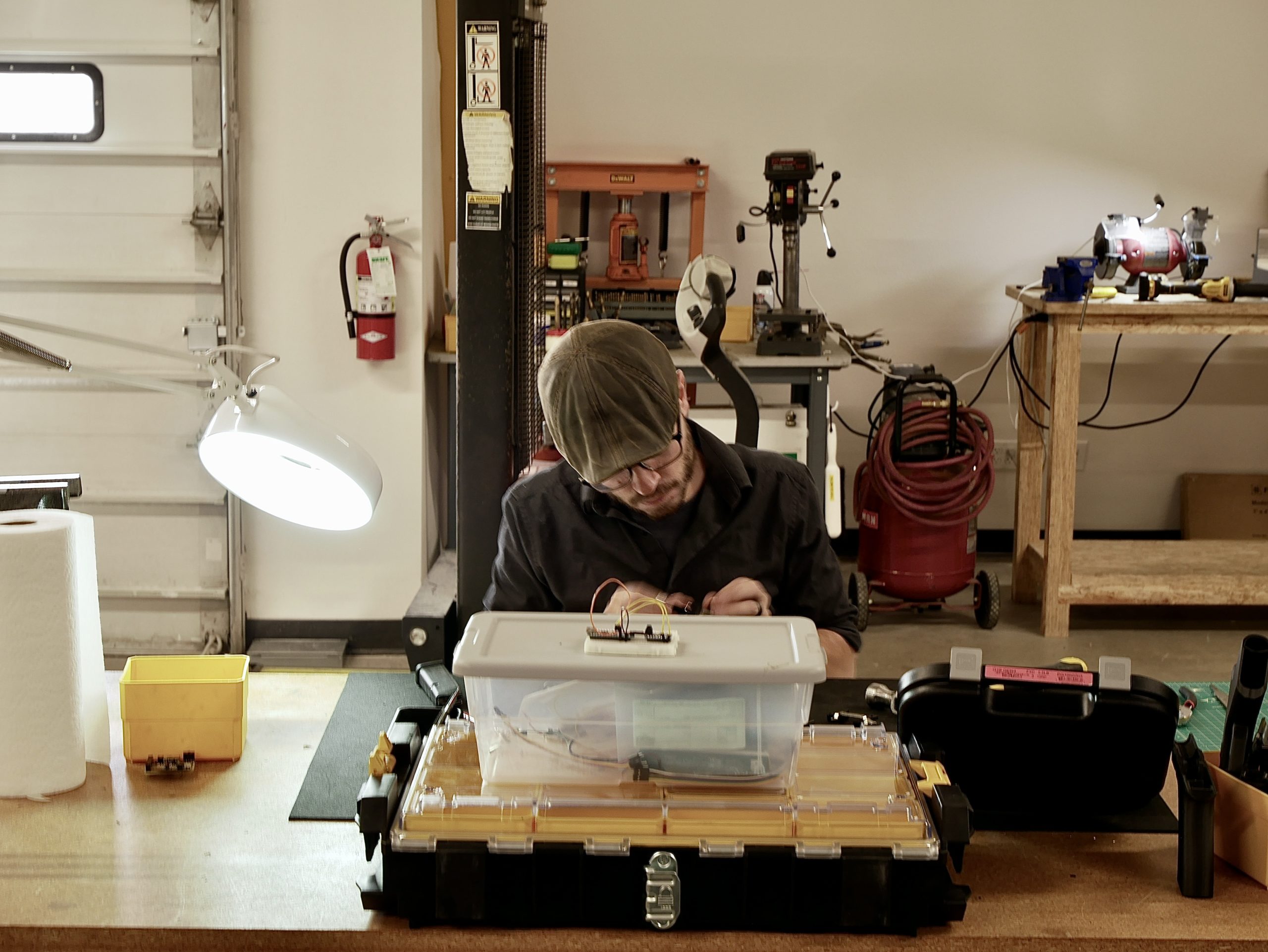
“Amazing People” Key to Our Success: Highlights from The BigTime Podcast
We’ve come a long way since our company’s inception in 2008.
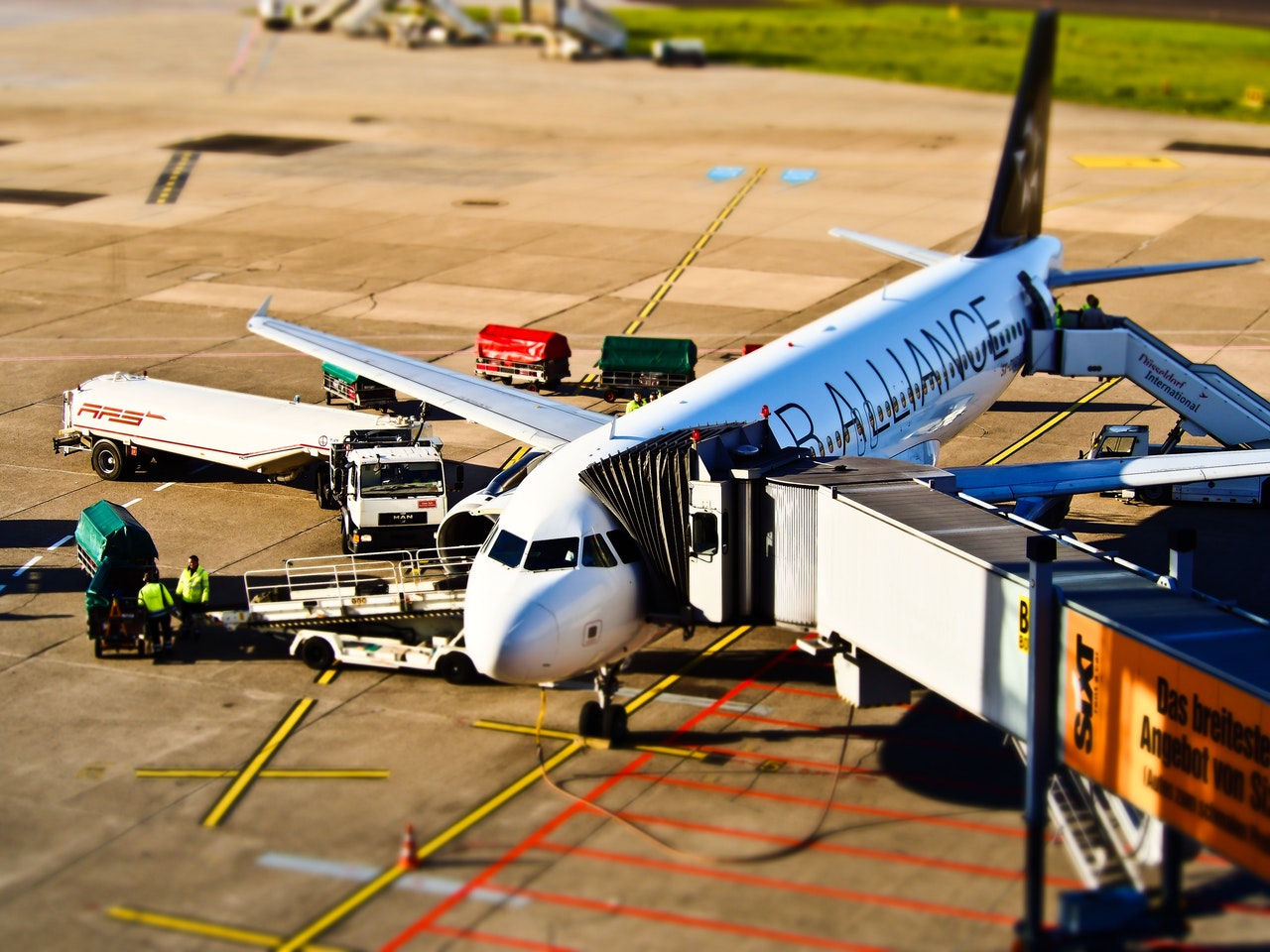
Exceptional Ground Support Equipment Design: The AERO Specialties Story
When AERO Specialties first reached out to us in 2013, we were eager to prove our ability to provide exceptional ground support equipment design.
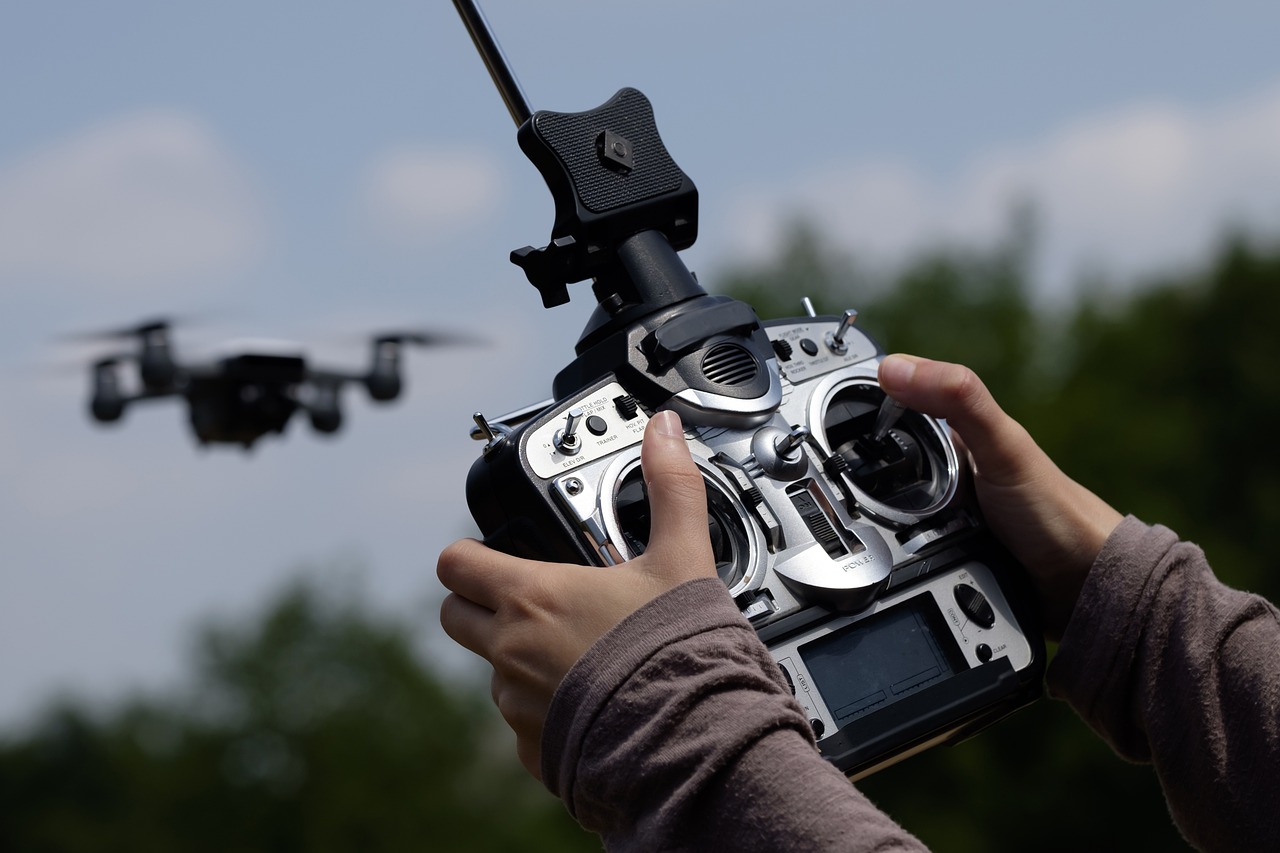
Drone Racing is Here to Stay
August 2016 marked the second annual U.S. National Drone Racing Championships in New York City, the same year the Drone Racing League was publicly launched.
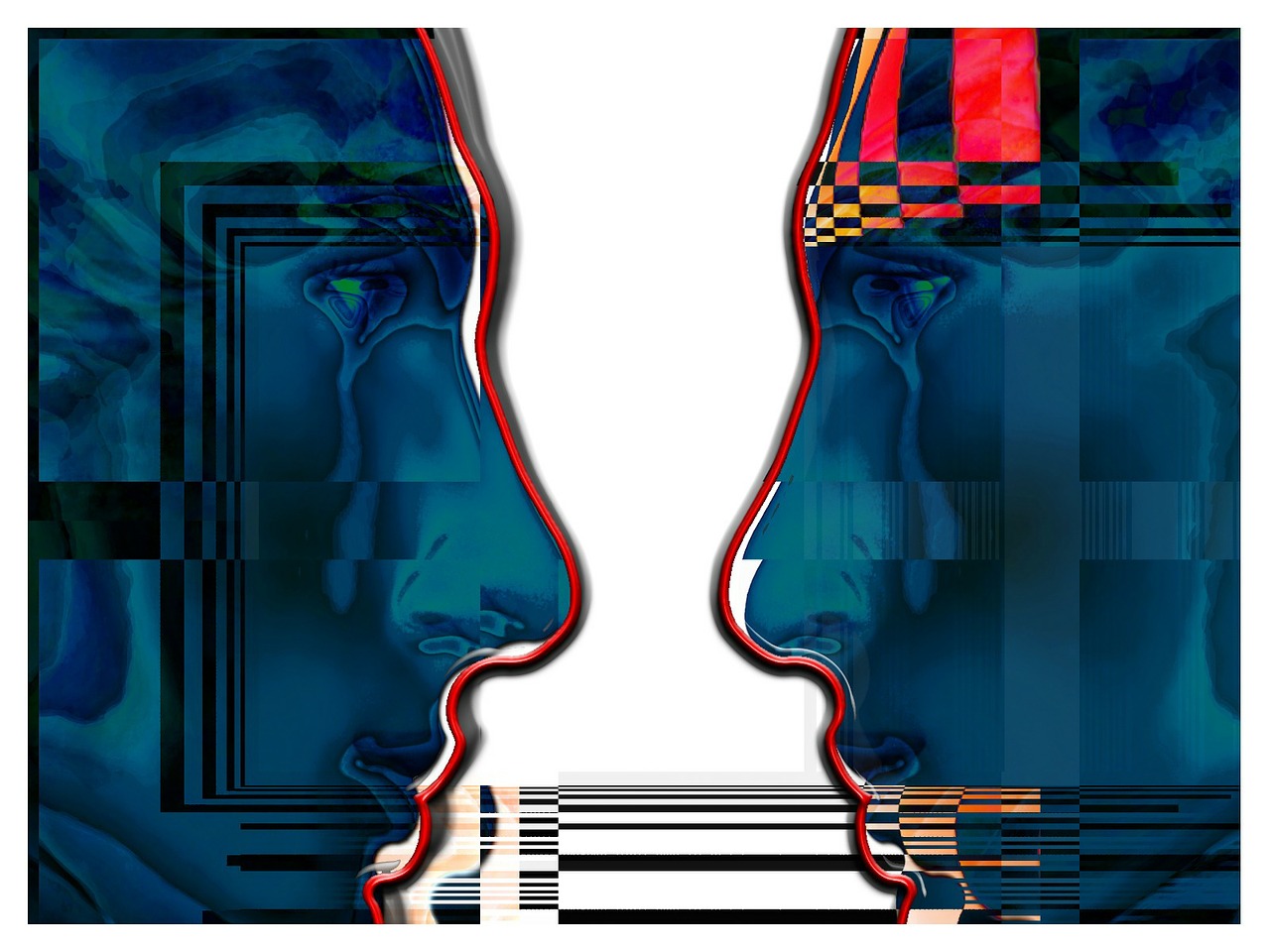
Empathy in Action: An Example of Empathic Product Design
When people hear the word “empathy,” many think of how it affects our interpersonal relationships, specifically how we relate to and connect with other humans.
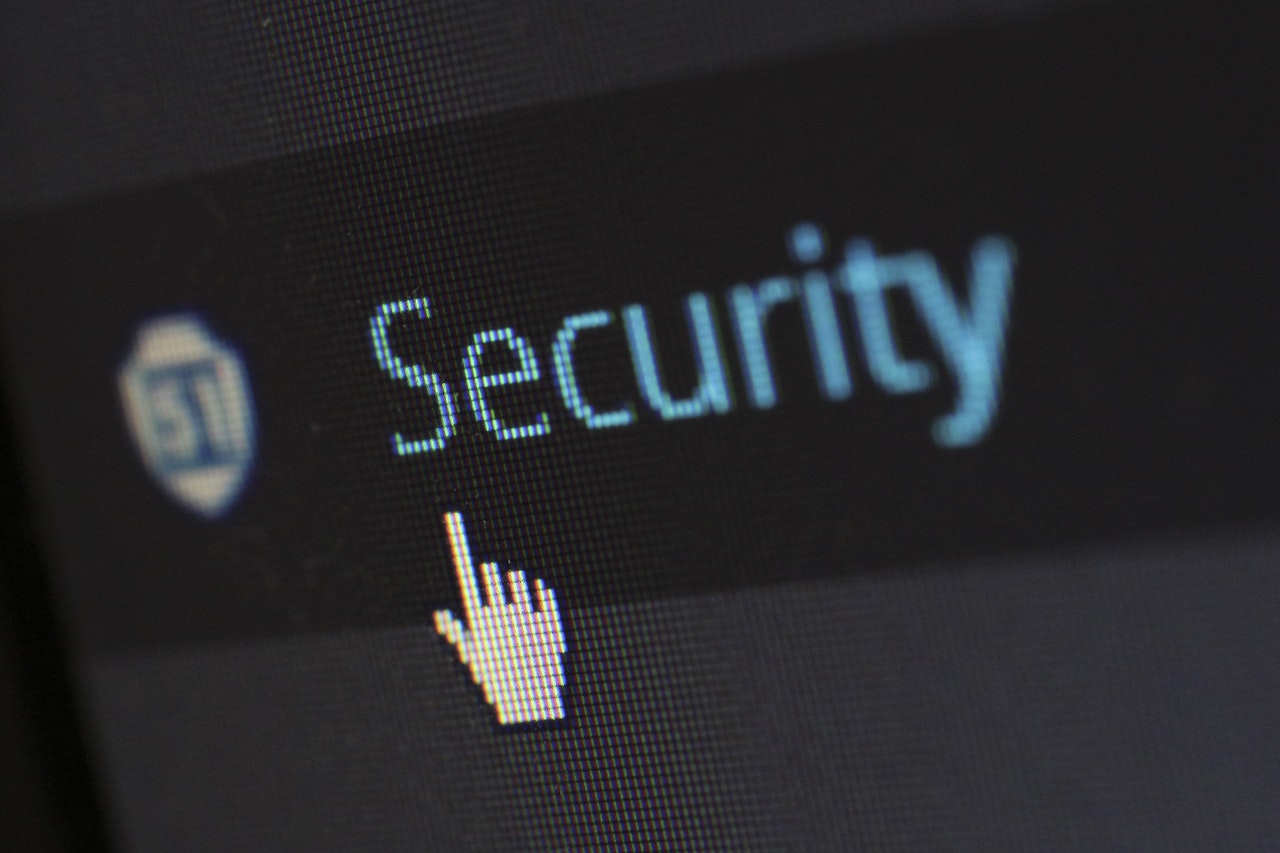
Client Confidentiality in Product Design and Development
If you’ve been acquainted with SGW Designworks for a while, you know we are vocal champions of our clients’ successes.
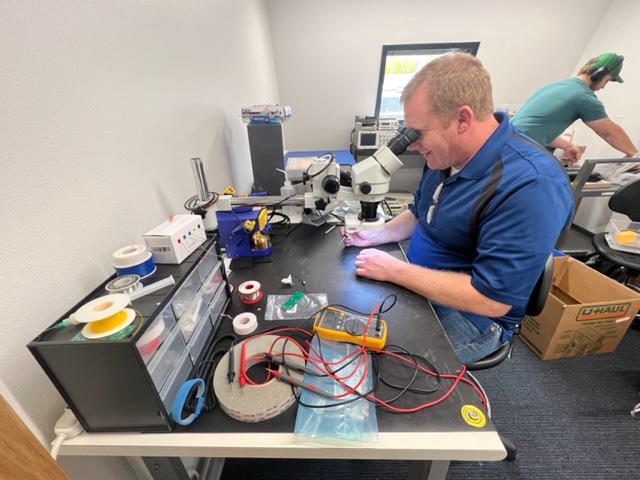
The Build-Measure-Learn Loop: The Linchpin of Successful Product Development
Since its publishing in 2011, Eric Ries’s bestselling book The Lean Startup (along with its principles, like the Build-Measure-Learn feedback loop) has ushered in an entrepreneurial revolution.
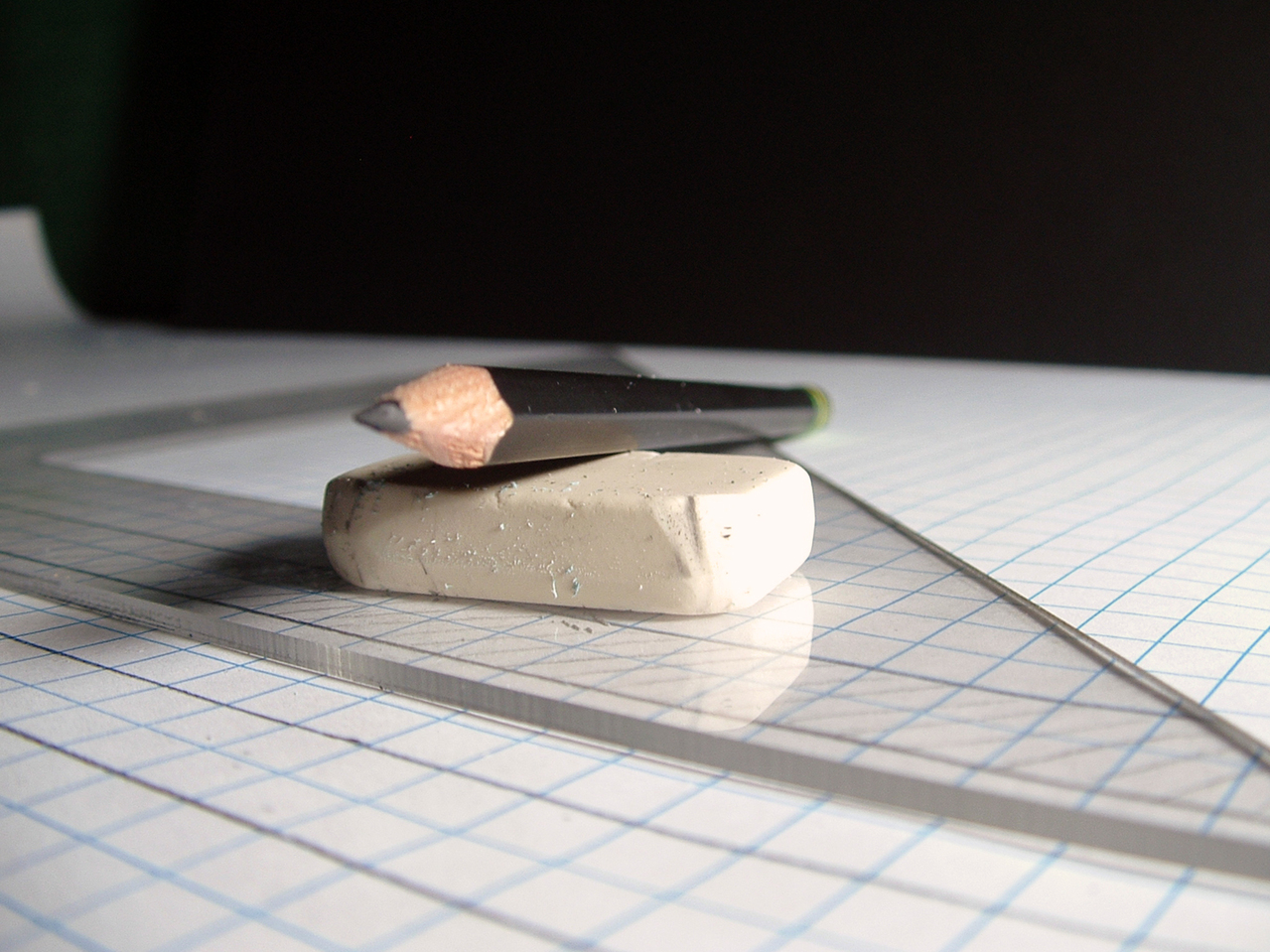
The Engineering Development Process Then and Now
Engineers who have been around pre-CAD remember when sketching their designs on paper was a standard part of the engineering development process.
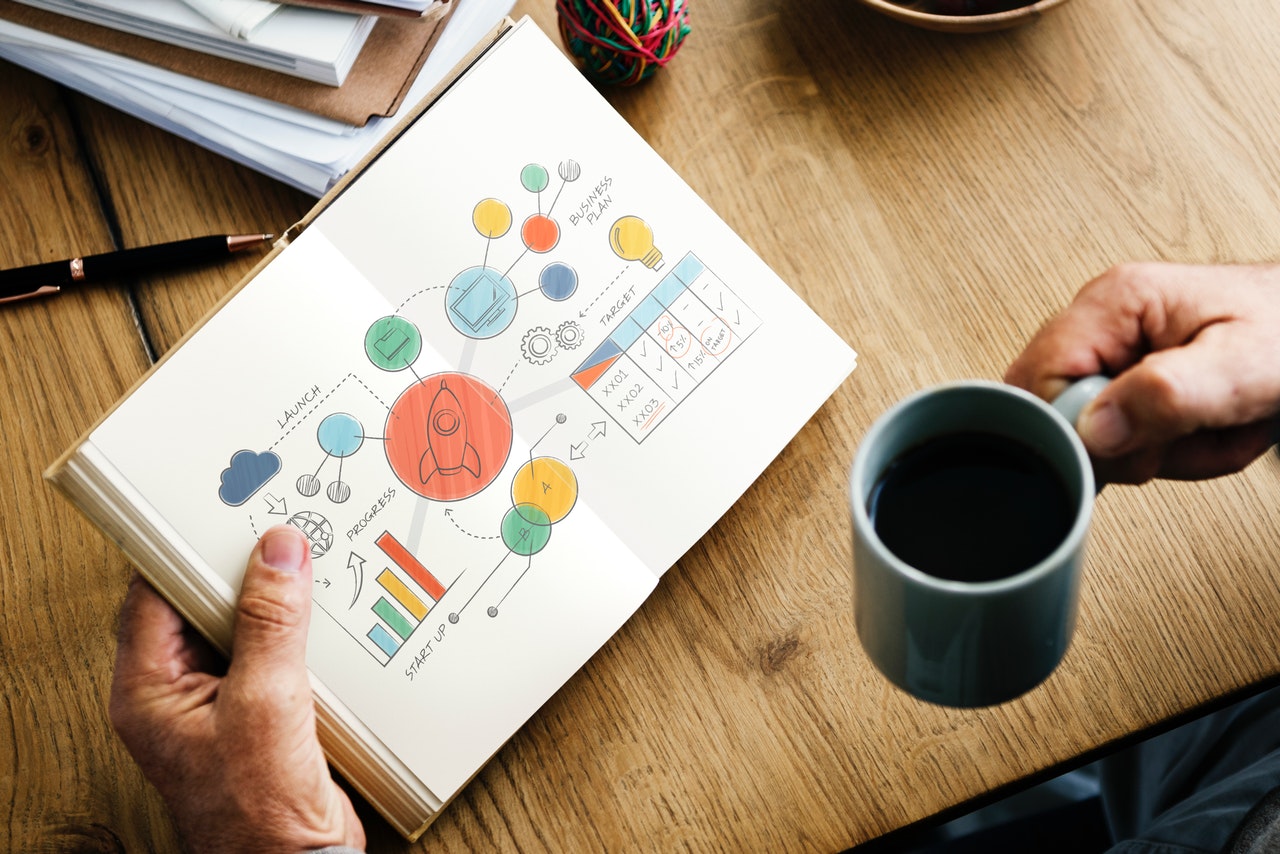
Commercializing an Idea: 9 Steps for Startups and Emerging Businesses
Mature businesses are keenly aware of the resources and investment required when commercializing an idea.
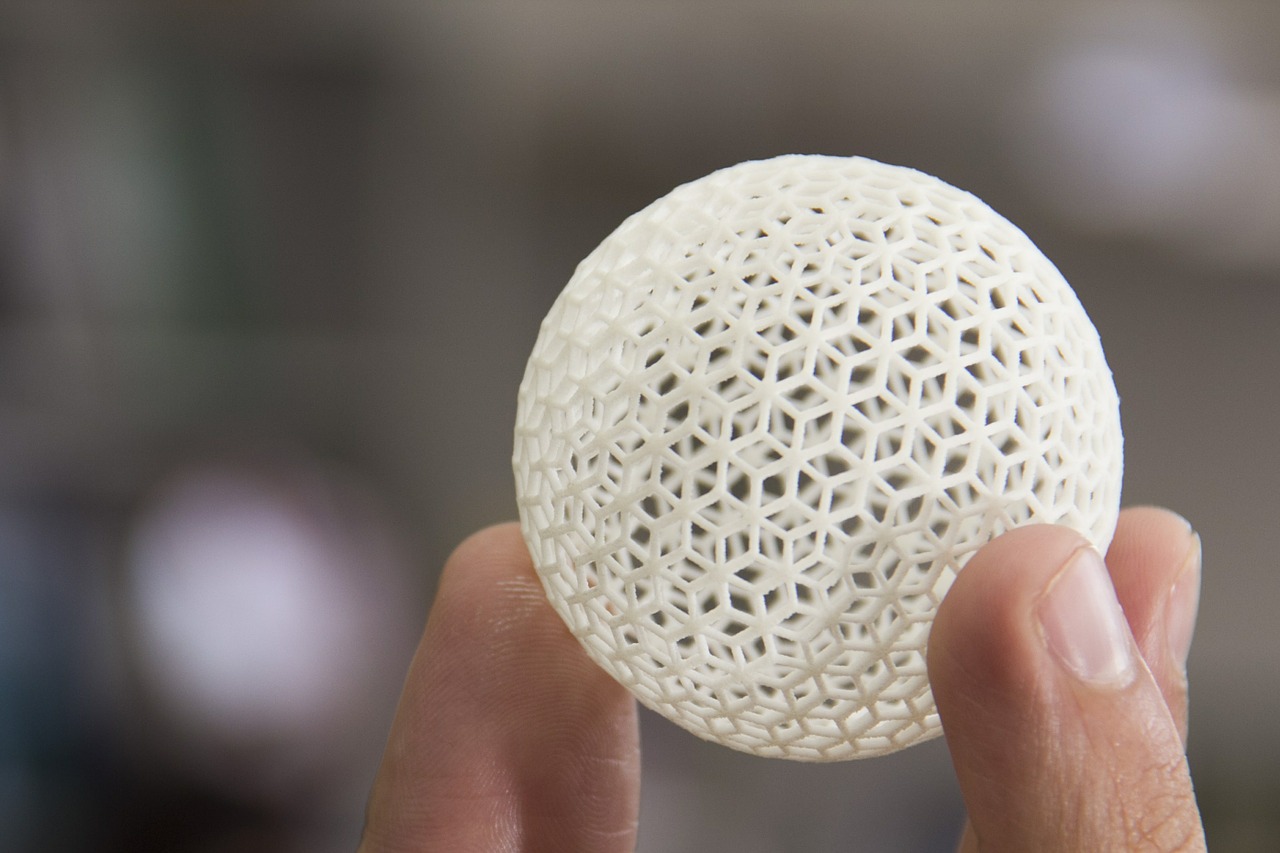
Injection Molding vs. 3D Printing – Which One, When?
As a product development company, we focus on applying lean principles and working with insight.
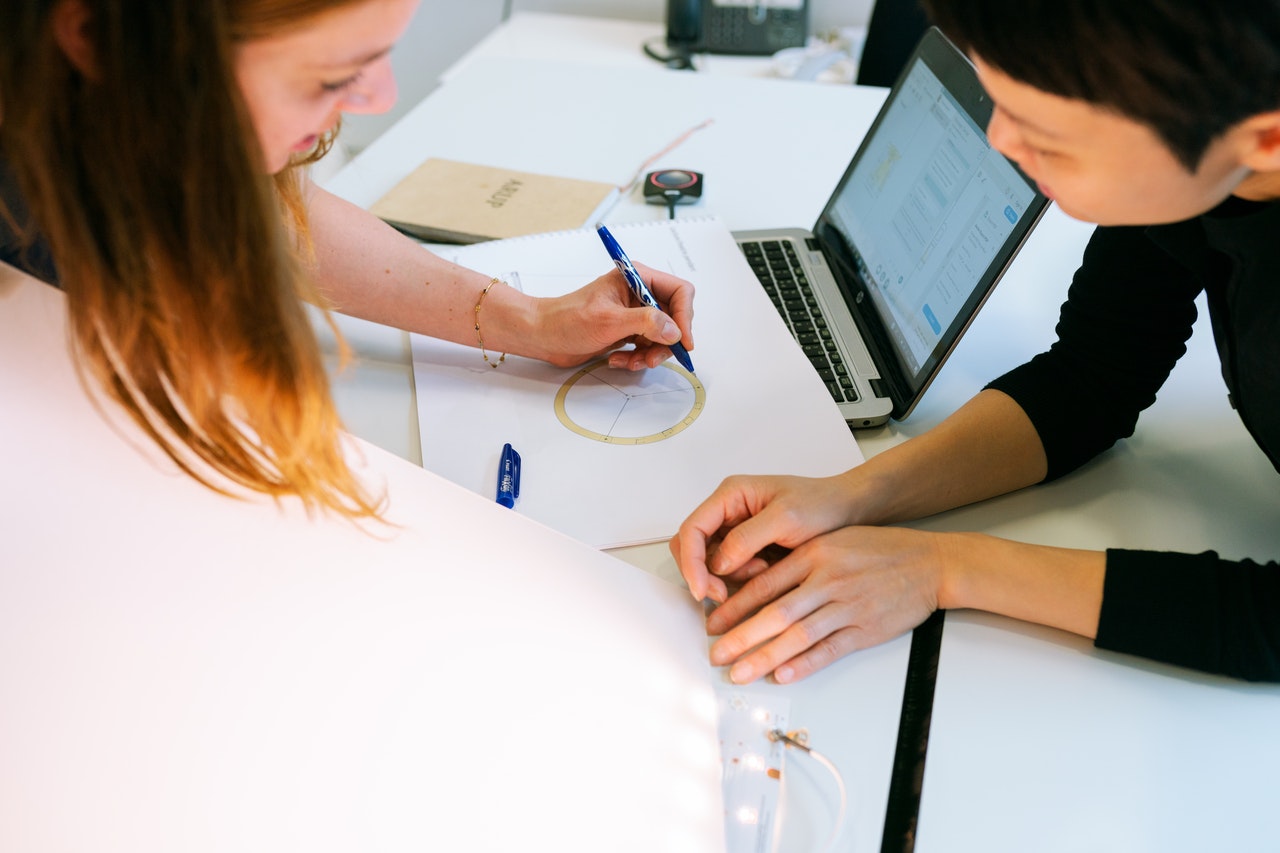
6 Reasons Why Most Products Fail (and 6 Tips for Success)
If you wanted to embark on a new business venture but knew it had only a five percent chance of success, would you proceed?
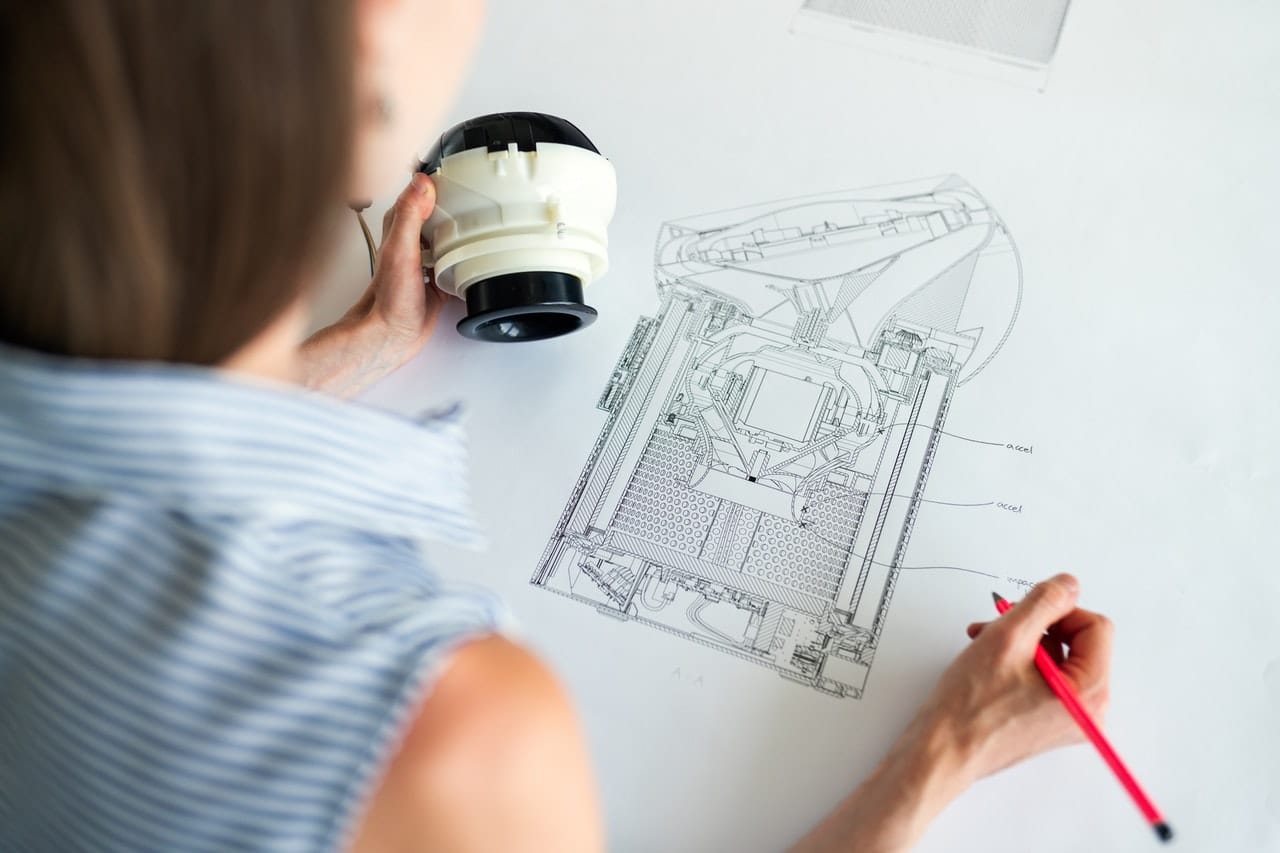
6 Product Development Trends to Expect, Post-Pandemic
A few months ago, several members of the SGW Designworks leadership team convened for a roundtable discussion that served as both a retrospective and a projection of where we see our company going in the months and years to come.
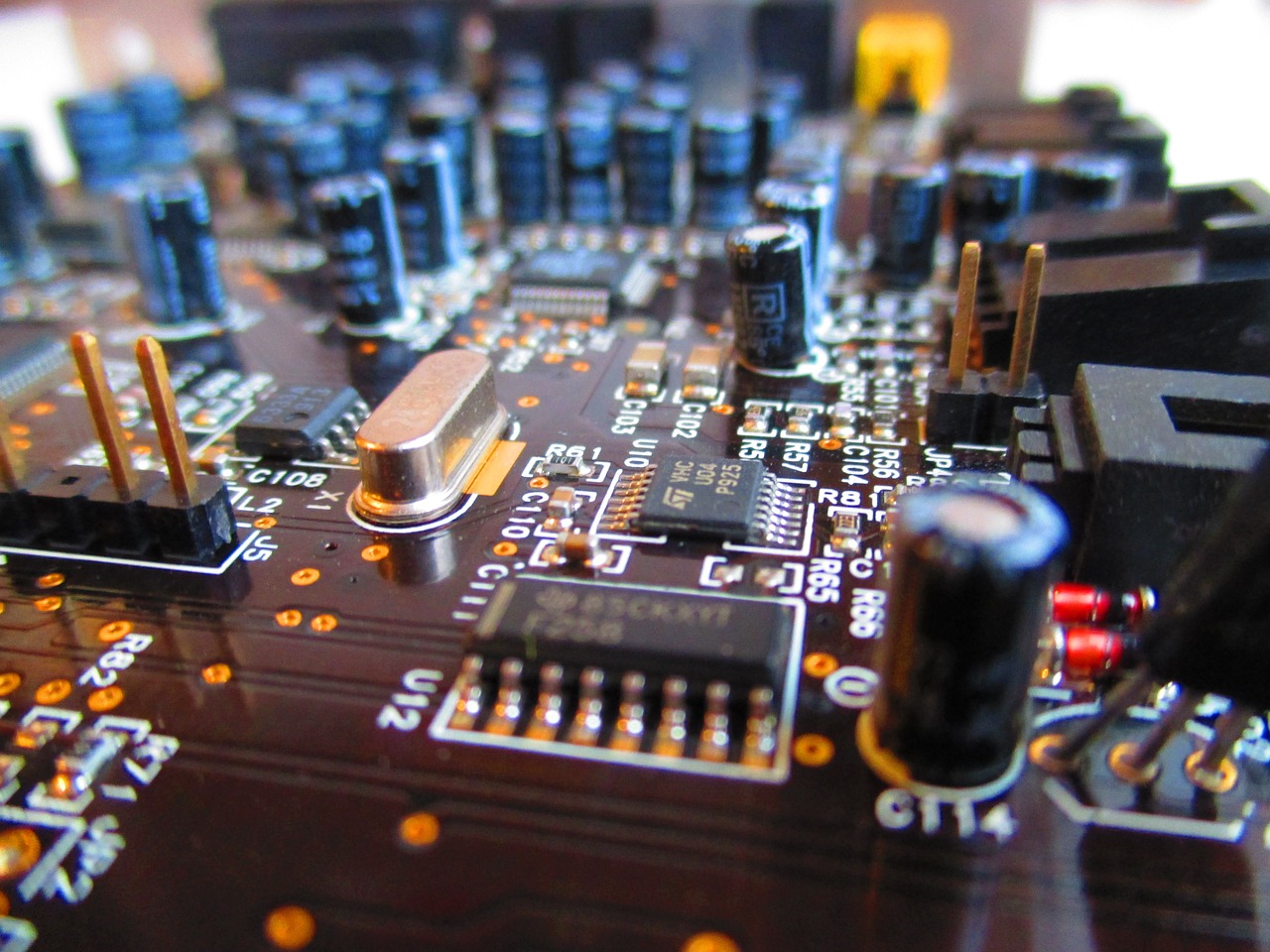
Lean Hardware Development: What’s Working Among Companies Large and Small?
If the terms “feature creep,” “waterfall,” and “agile methodology” are a regular part of your vernacular, it’s safe to assume your career entails lean hardware development.
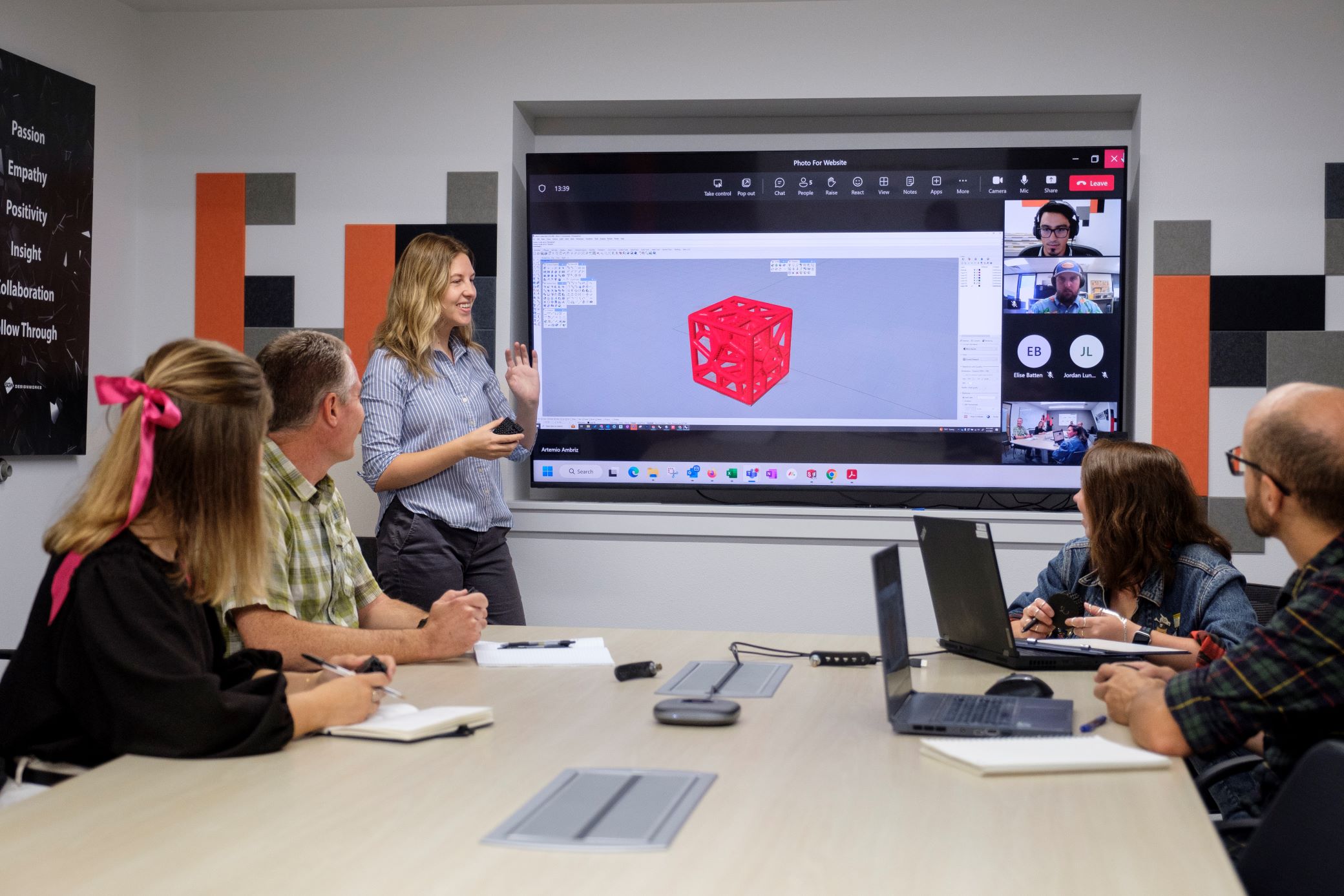
Product Design for Manufacturing: Streamlining for Efficiency and Cost-Effectiveness
How to plan and effectively design a product for manufacturing.
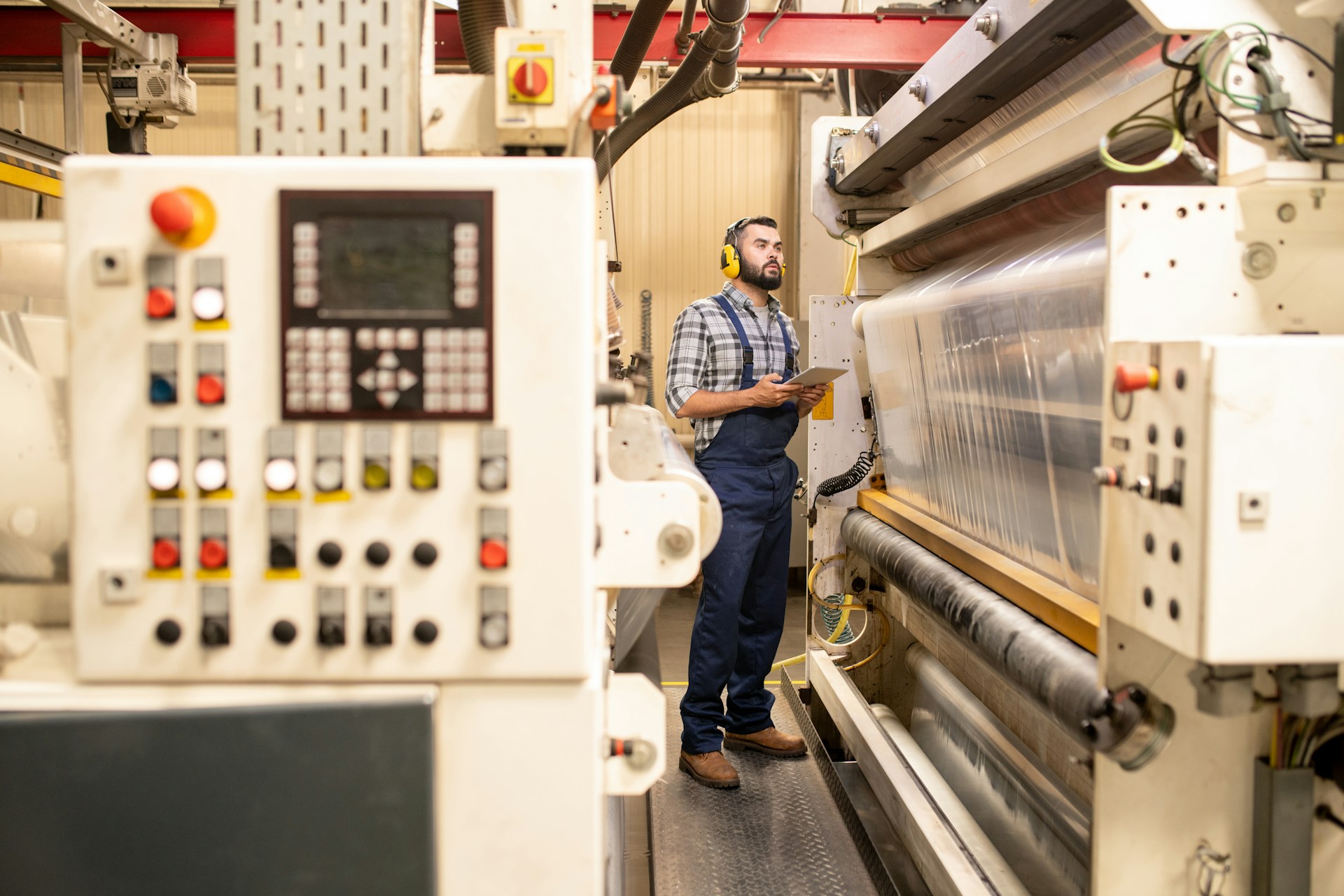
Design for Manufacturability: Streamlining the Production Process
Design for Manufacturability: Streamlining the Production Process
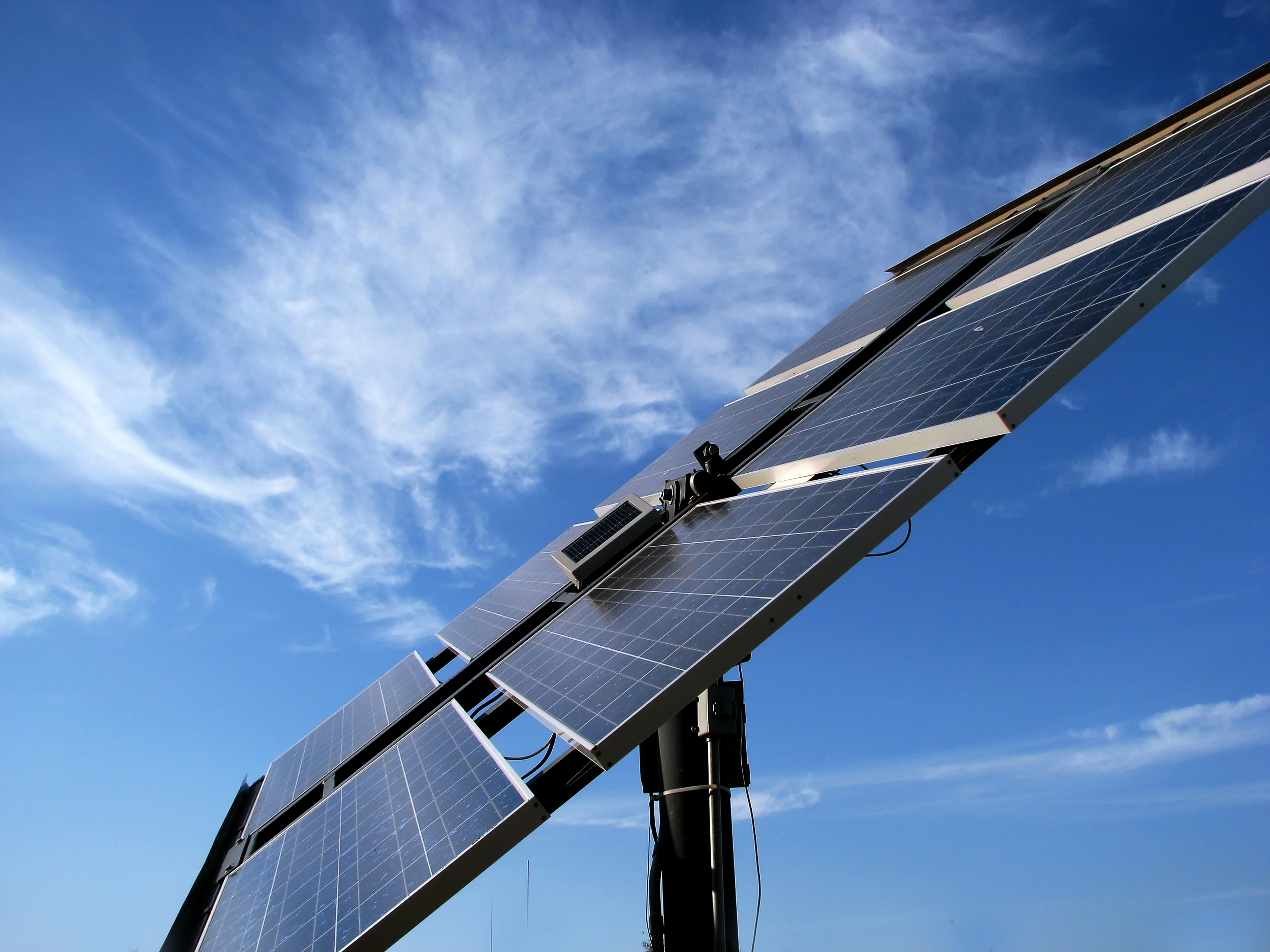
3 Important Factors in Solar Product Development
There has been a surge of interest in solar product development in recent years, driven by the growing demand for sustainable energy solutions.
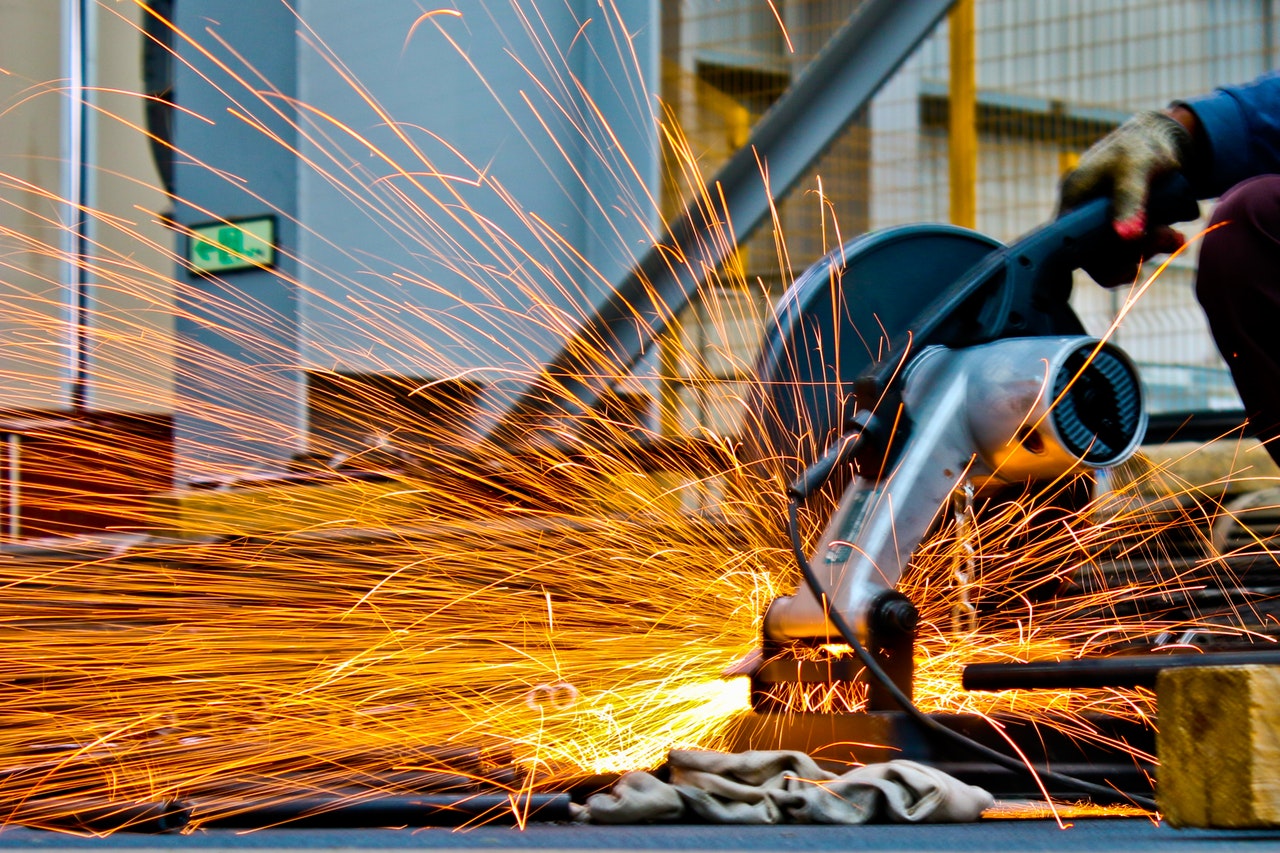
10 Machine Processes Used to Create Product Prototypes
Here's a list of several machine shop tools and processes that we as product developers employ.
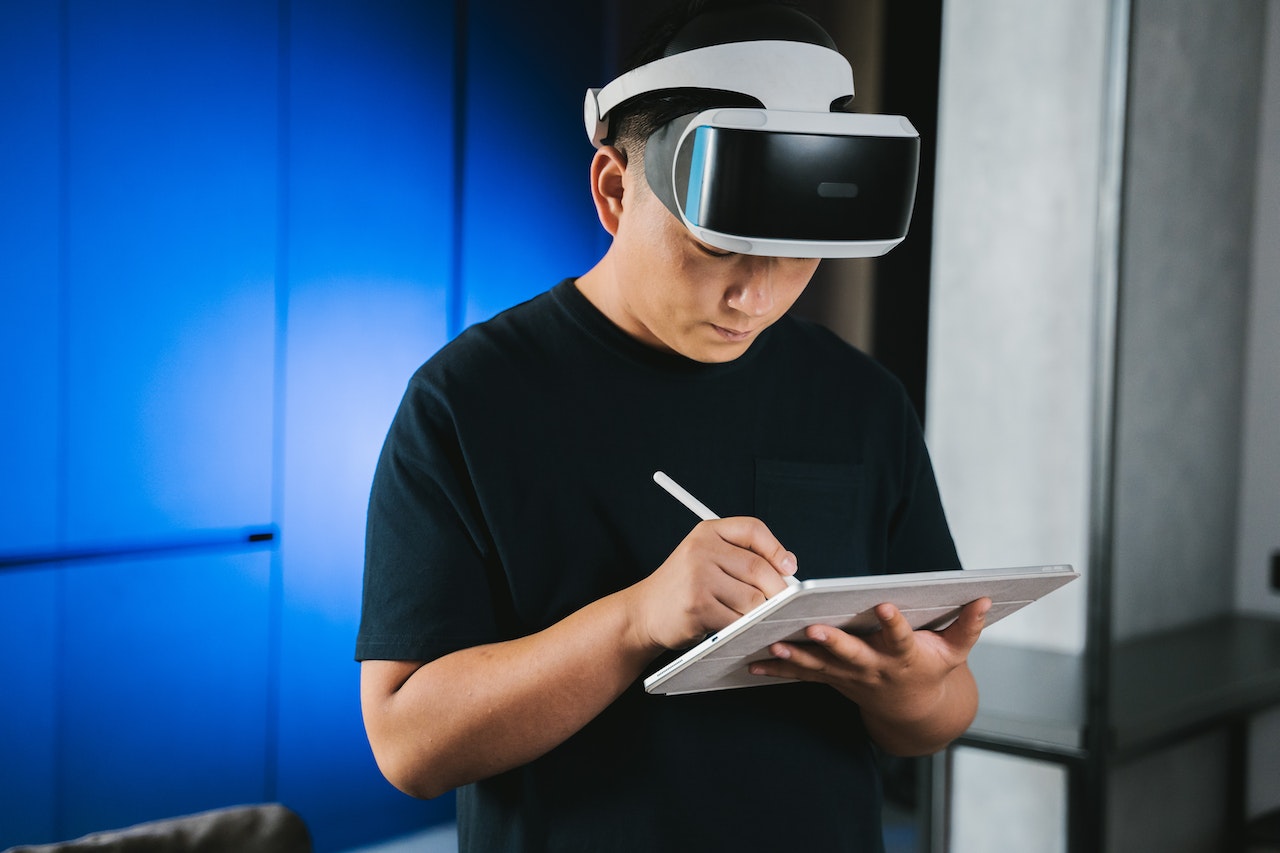
Virtual Reality Prototyping Can Save you Thousands of Dollars
When you hear the term virtual reality prototyping, do you instantly think of gaming?
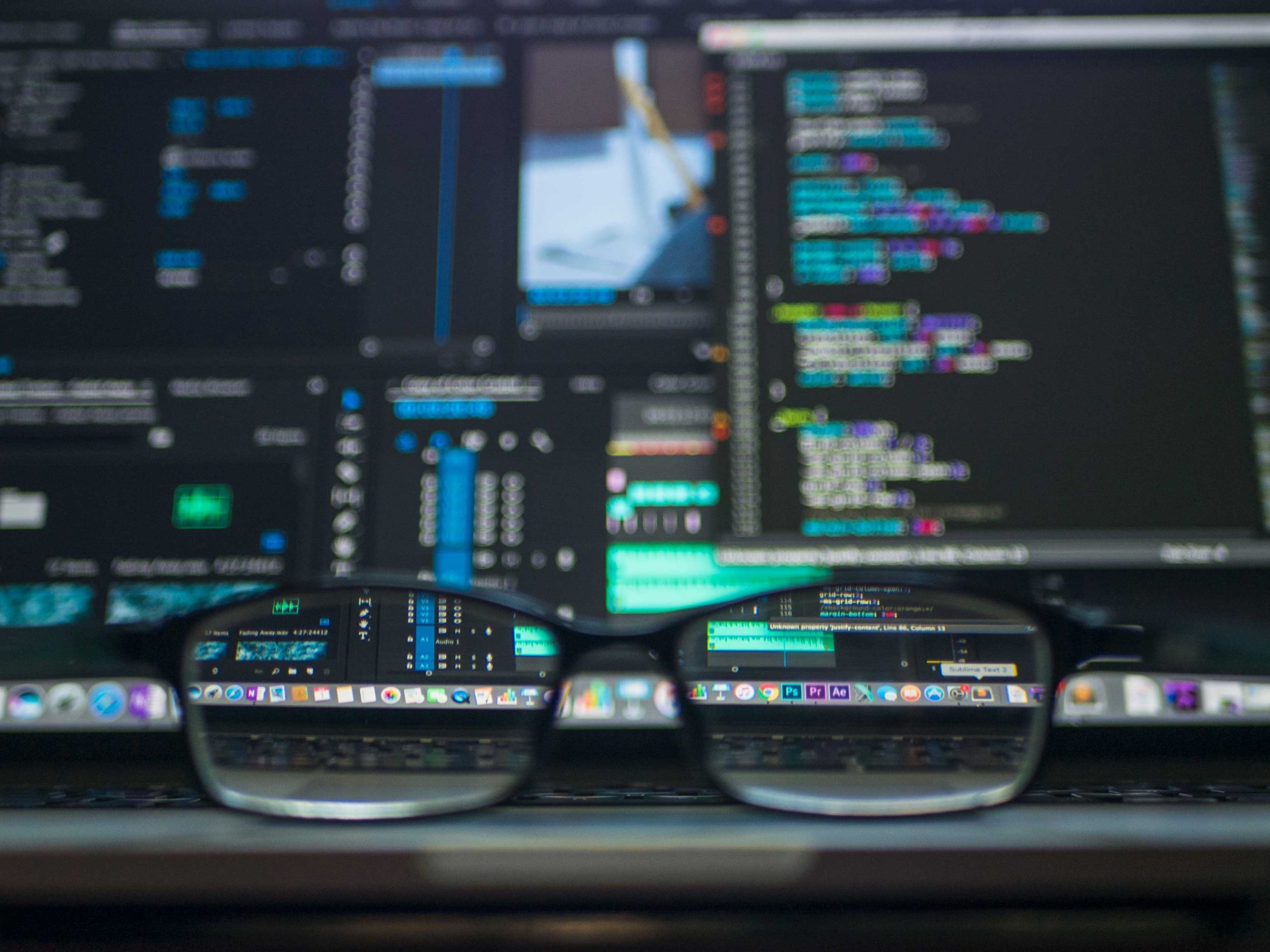
Developing a New Electronic Product in 2023? Avoid These 3 Common Firmware Engineering Problems
The market for connected products and IoT devices continues to grow.
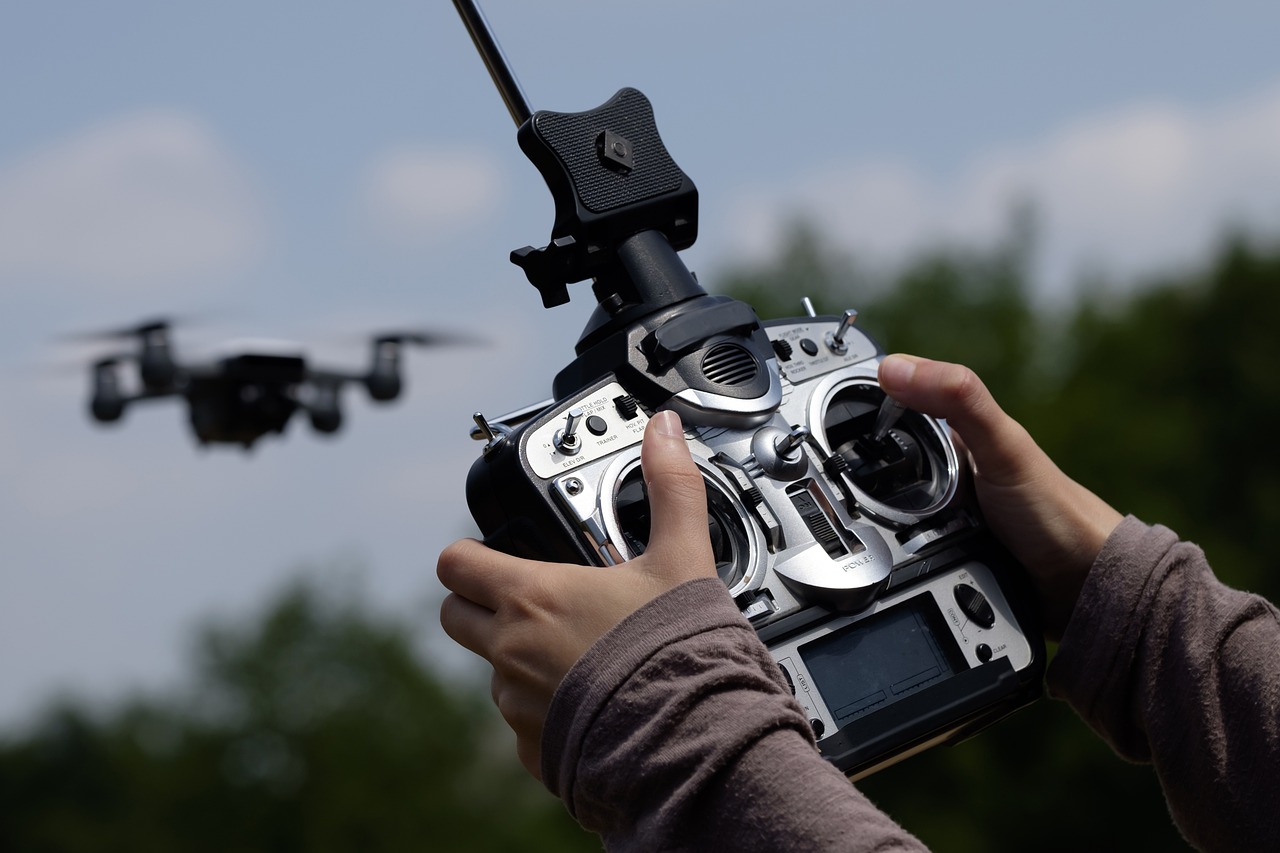
Drone Racing is Here to Stay
August 2016 marked the second annual U.S. National Drone Racing Championships in New York City, the same year the Drone Racing League was publicly launched.
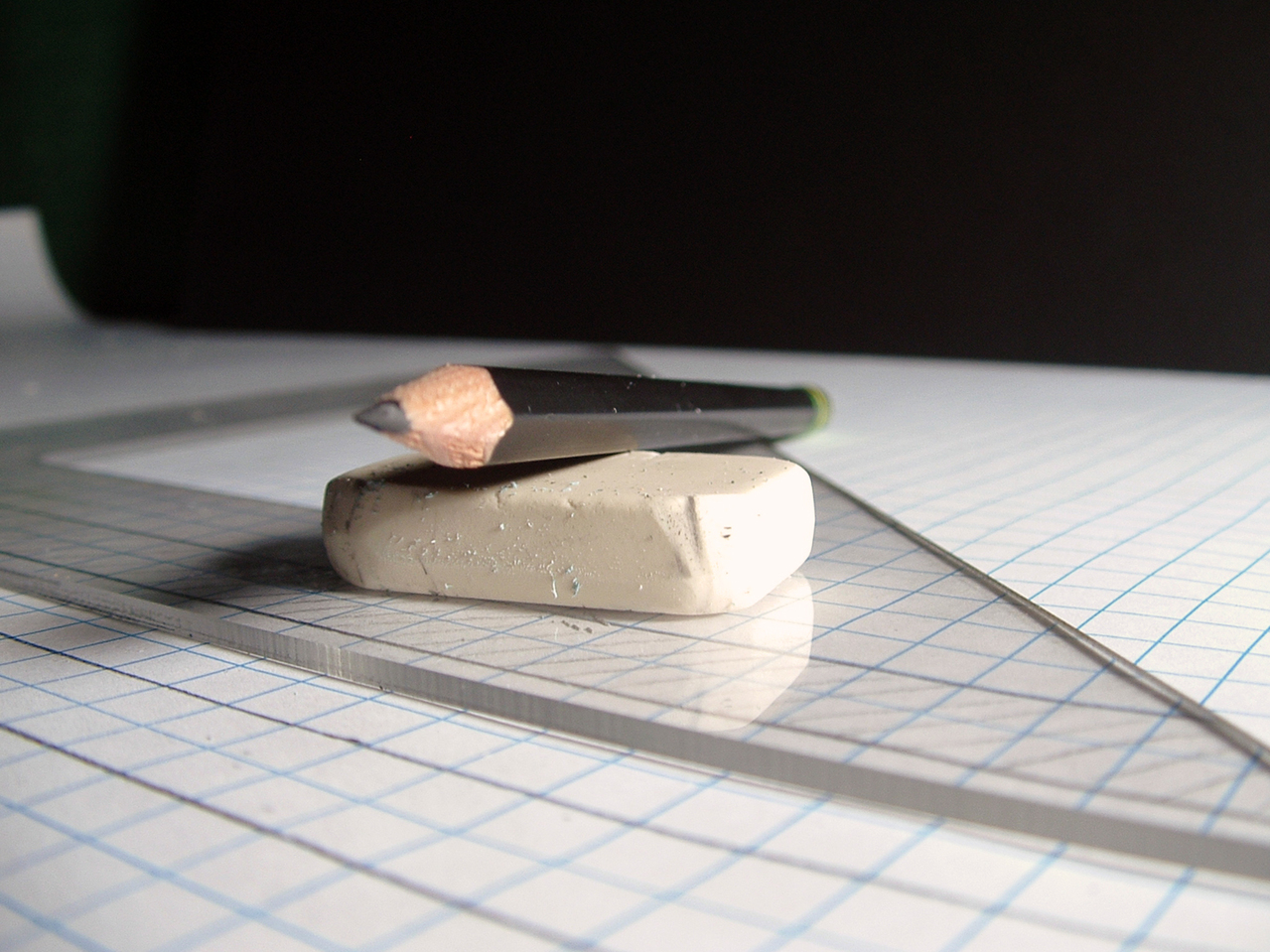
The Engineering Development Process Then and Now
Engineers who have been around pre-CAD remember when sketching their designs on paper was a standard part of the engineering development process.
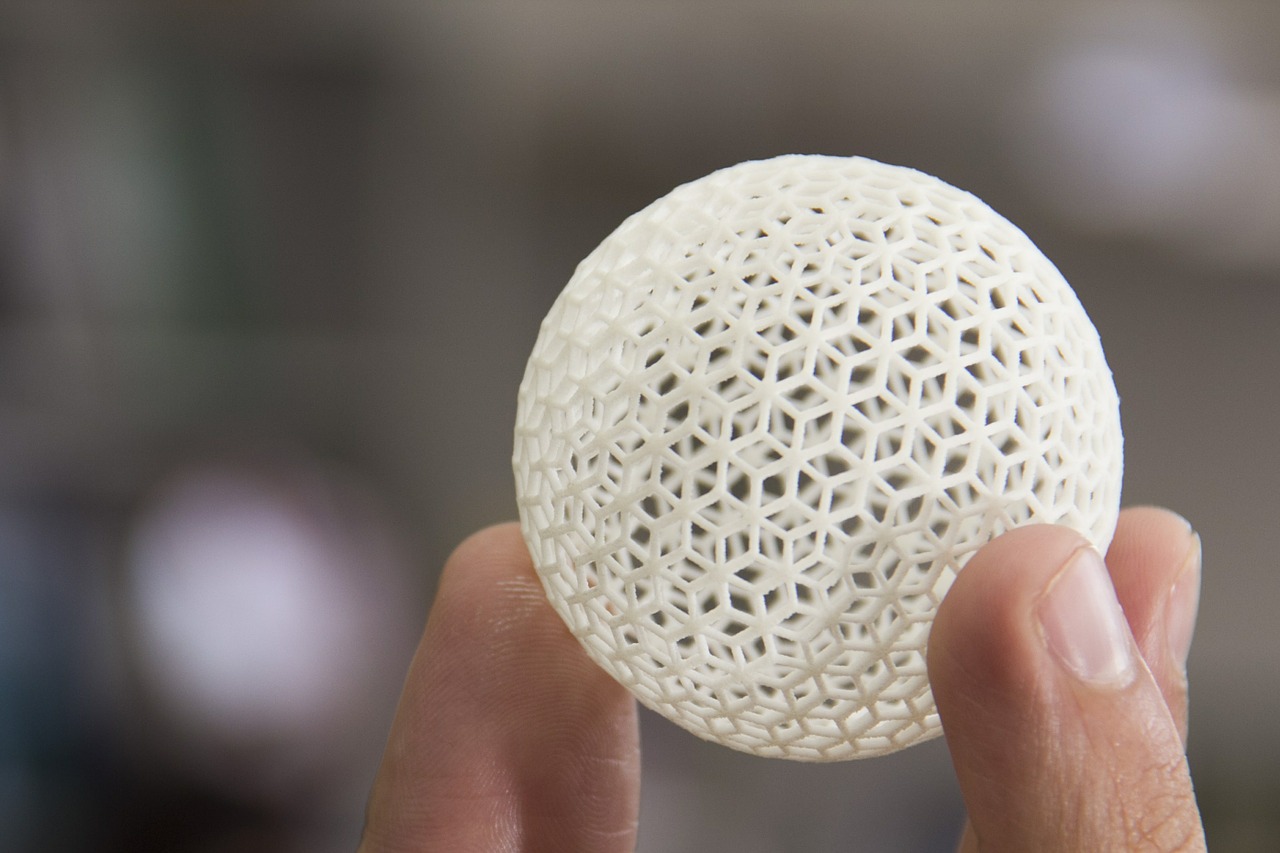
Injection Molding vs. 3D Printing – Which One, When?
As a product development company, we focus on applying lean principles and working with insight.
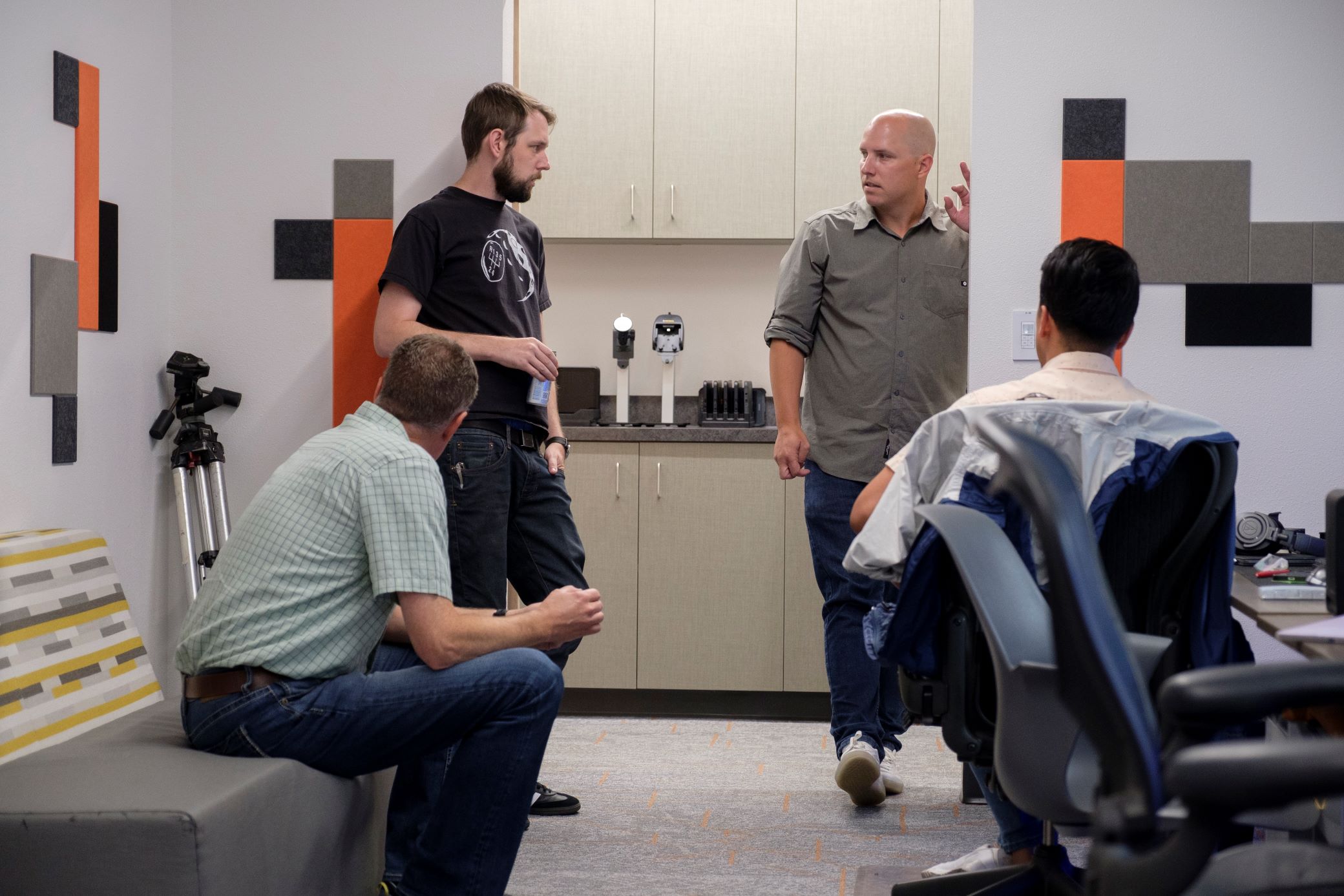
The Benefits of hiring the right Professional Engineering Consultants
What does it take to find the right engineering consultants for my product? Read to learn more.
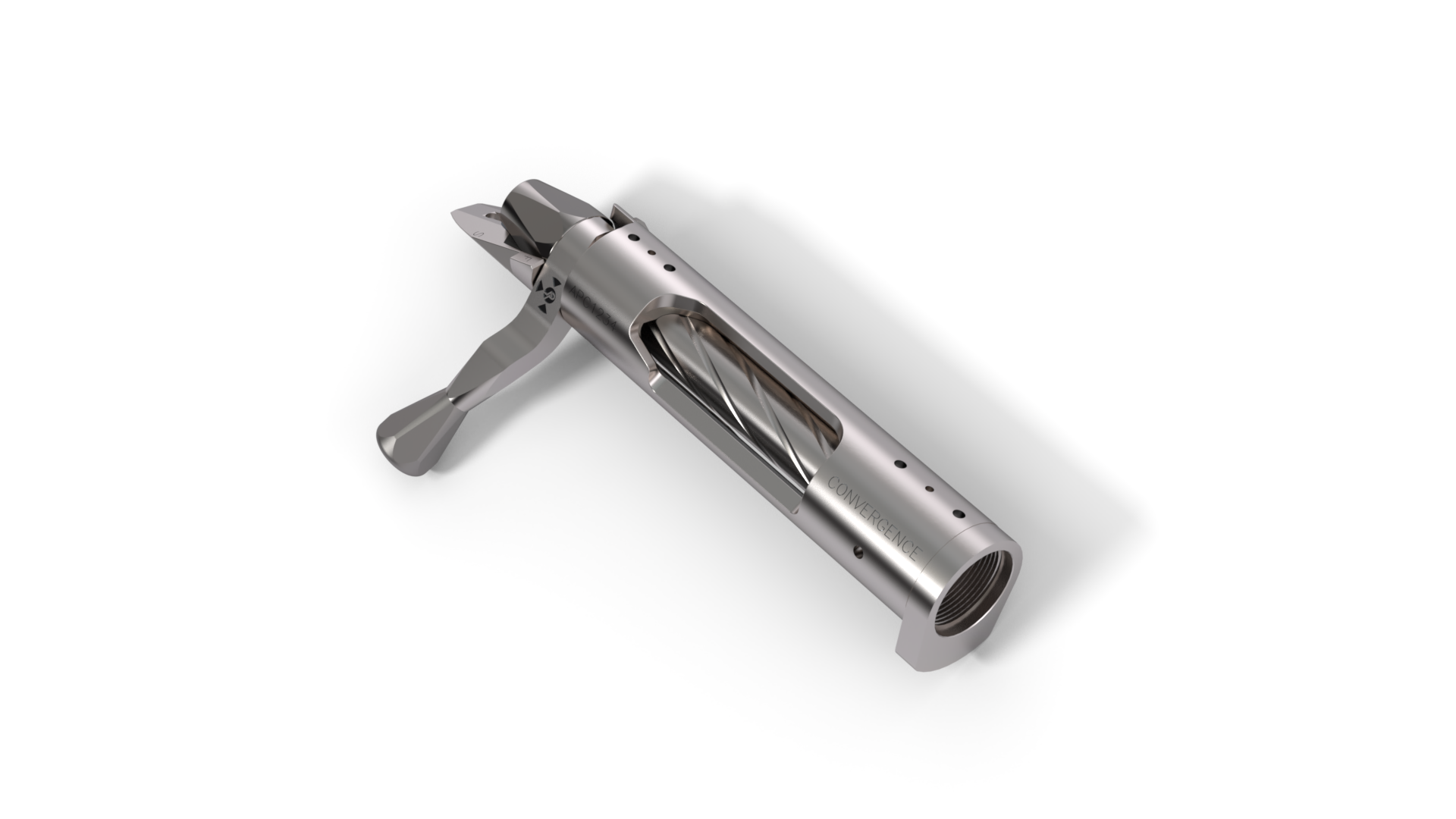
Precision Engineering Meets Innovation in Firearms Development
The unique considerations in firerams design projects, and the types of firearms projects SGW Designworks takes on.
Industrial Design Company: Creating Innovative Products for Modern Needs
Industrial Design Company: Creating Innovative Products for Modern Needs
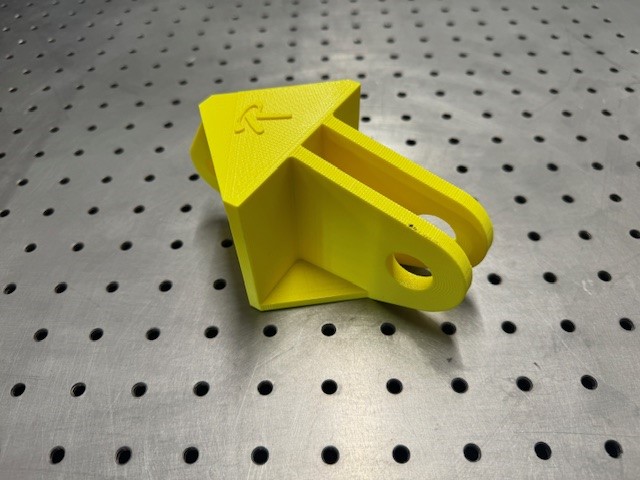
Prototype Development Services: Streamlining Your Product Development Process
Prototype Development Services: Streamlining Your Product Development Process
.png)
How to Get Your Product from Concept to Market in 9 Steps
How to Get Your Product from Concept to Market in 9 Steps:
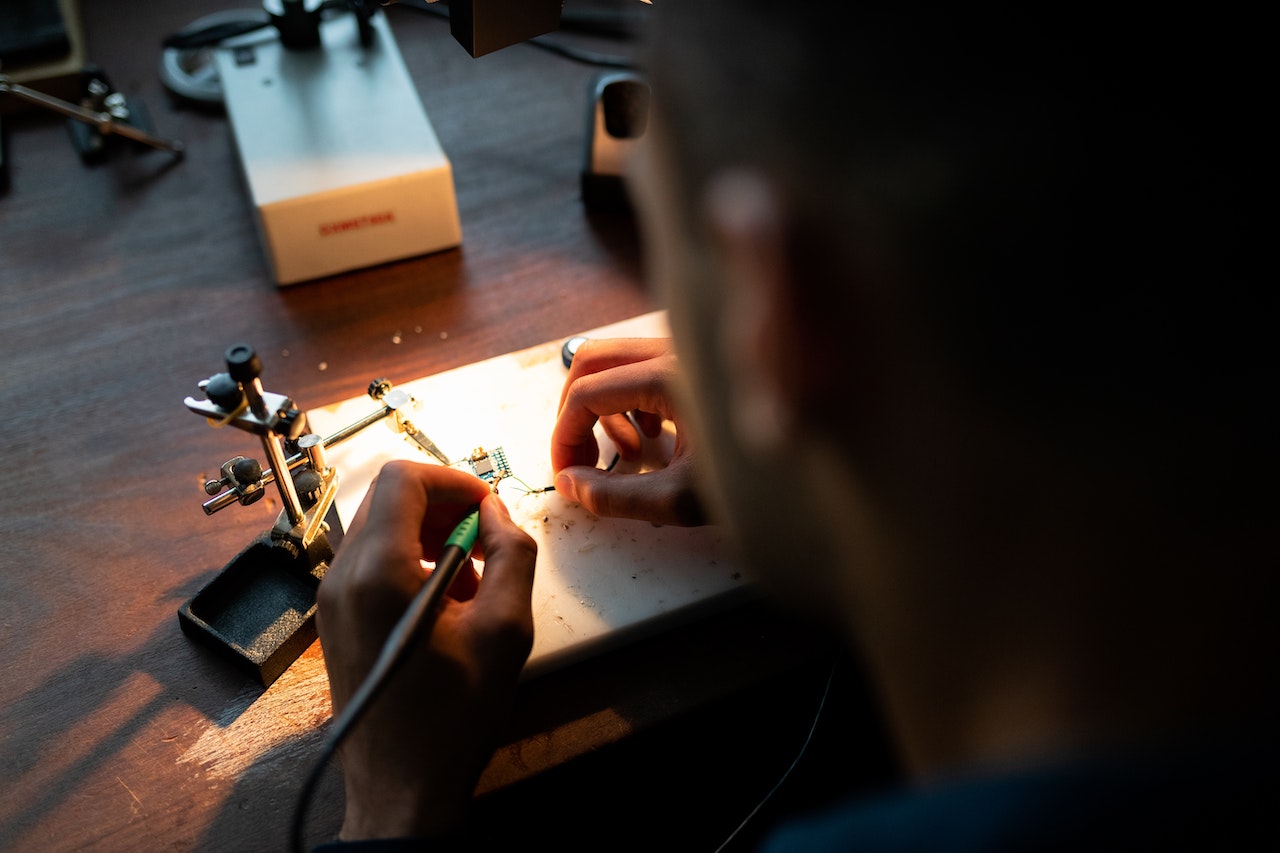
Pros and Cons of Outsourcing Physical Product Development in the U.S.
There are advantages and disadvantages of outsourcing physical / hardware product design and development to a U.S.-based company.
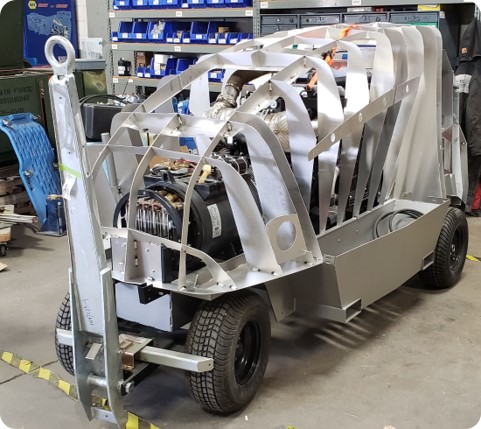
The Cost of Prototyping a Product
To determine the cost to develop prototypes of manufactured products, consider these questions.
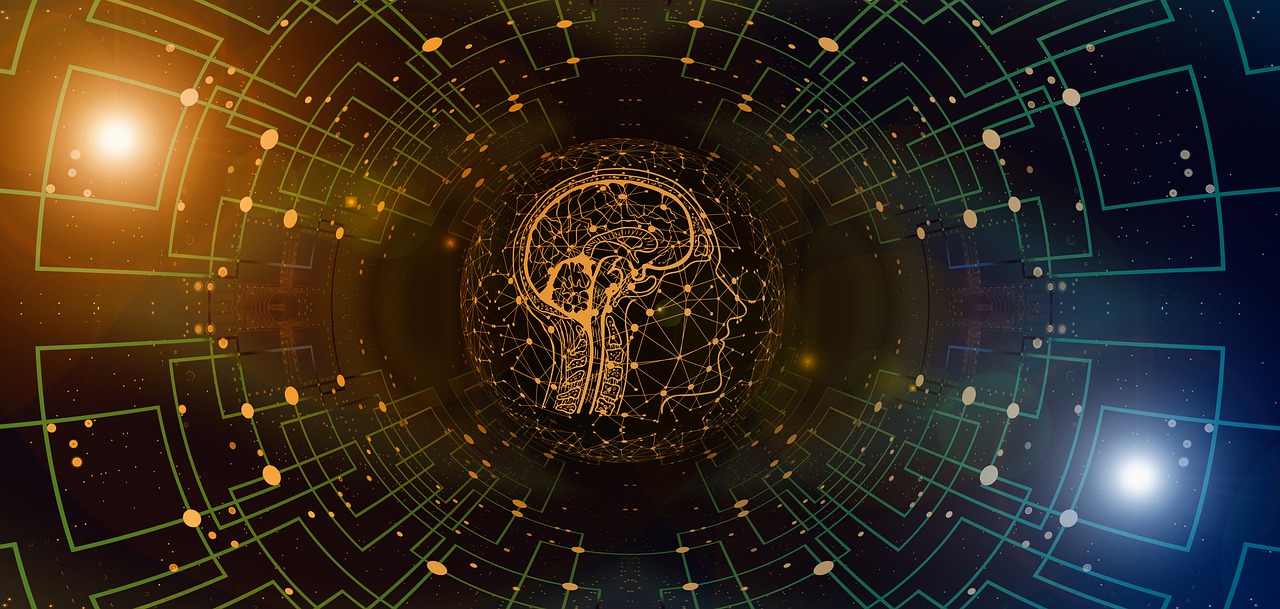
Why UI/UX? Best Practices for Successful Product Development
From the smartphone in your pocket to the vehicle you drive, great products don’t just happen.
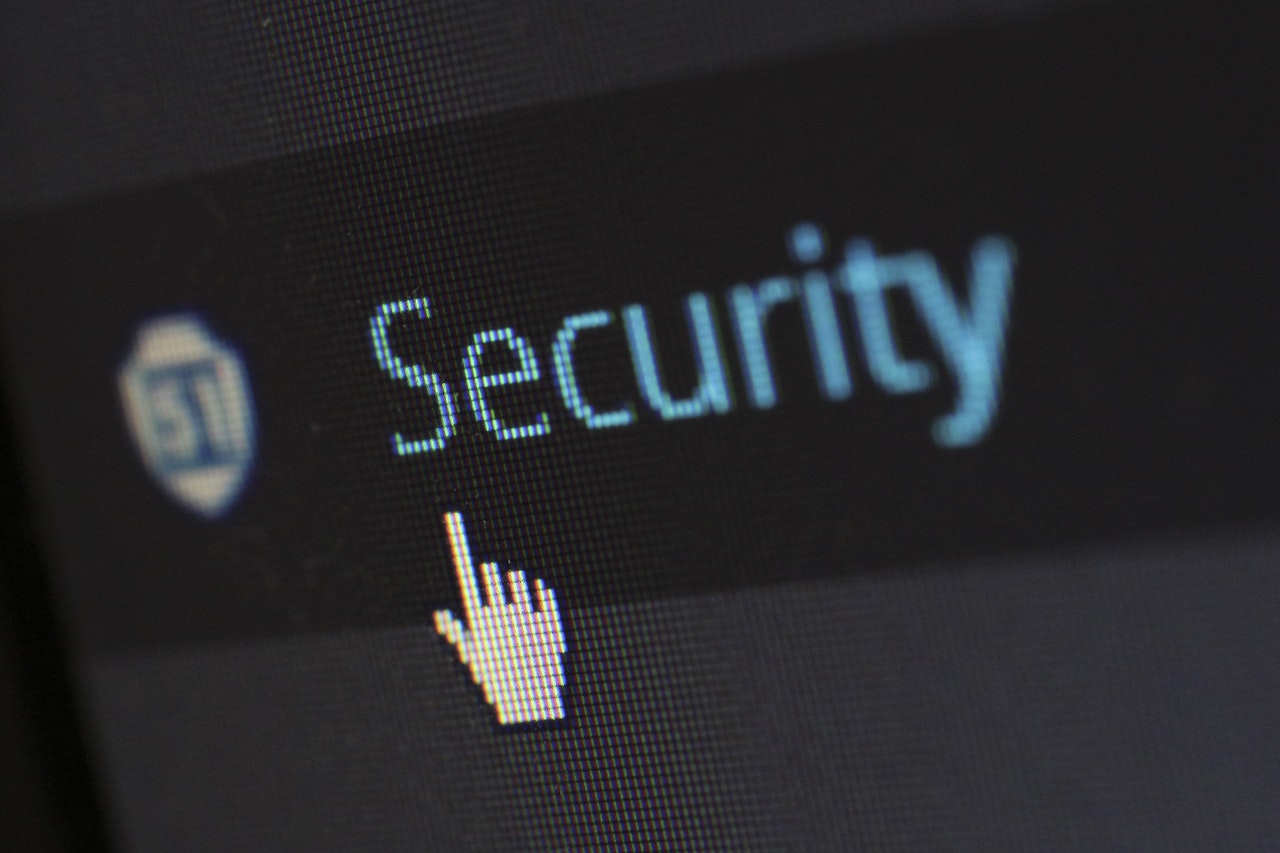
Client Confidentiality in Product Design and Development
If you’ve been acquainted with SGW Designworks for a while, you know we are vocal champions of our clients’ successes.
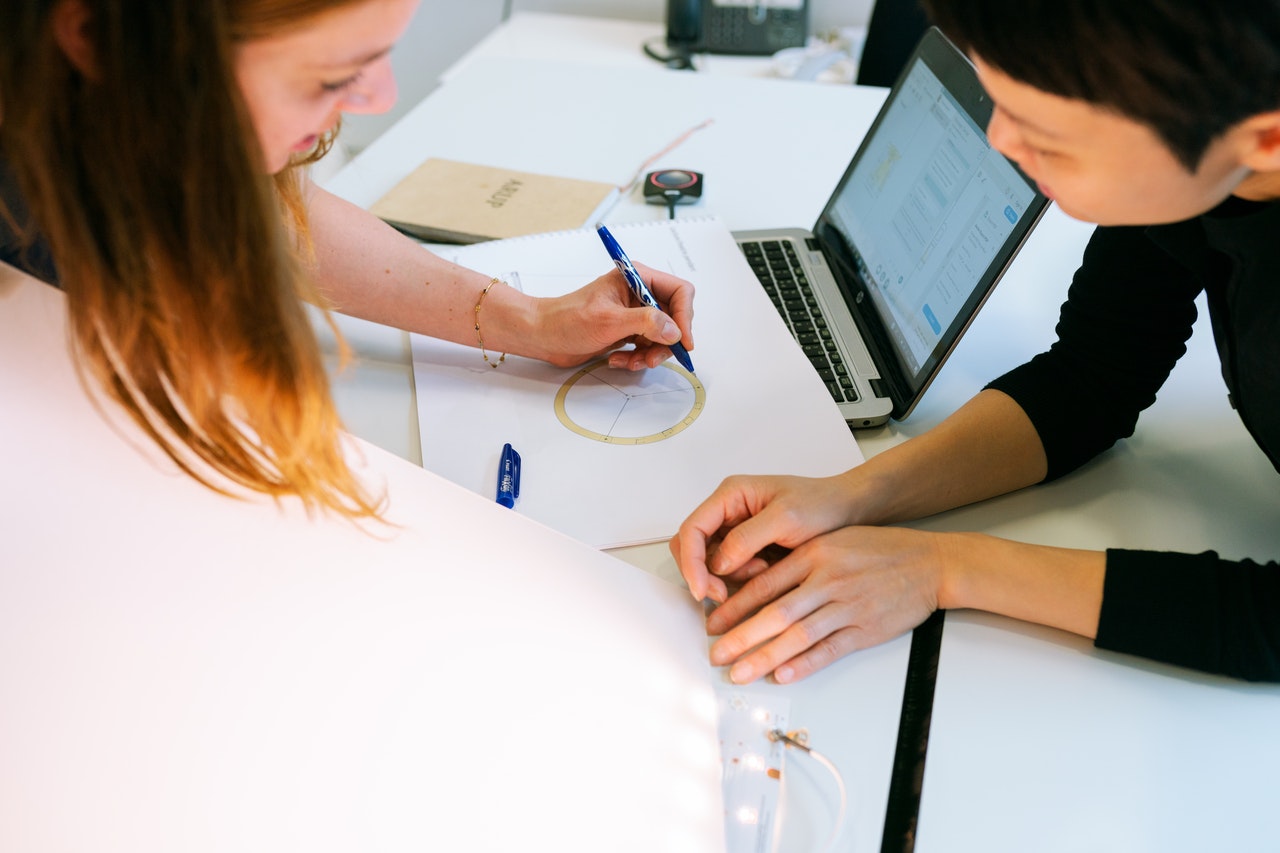
6 Reasons Why Most Products Fail (and 6 Tips for Success)
If you wanted to embark on a new business venture but knew it had only a five percent chance of success, would you proceed?
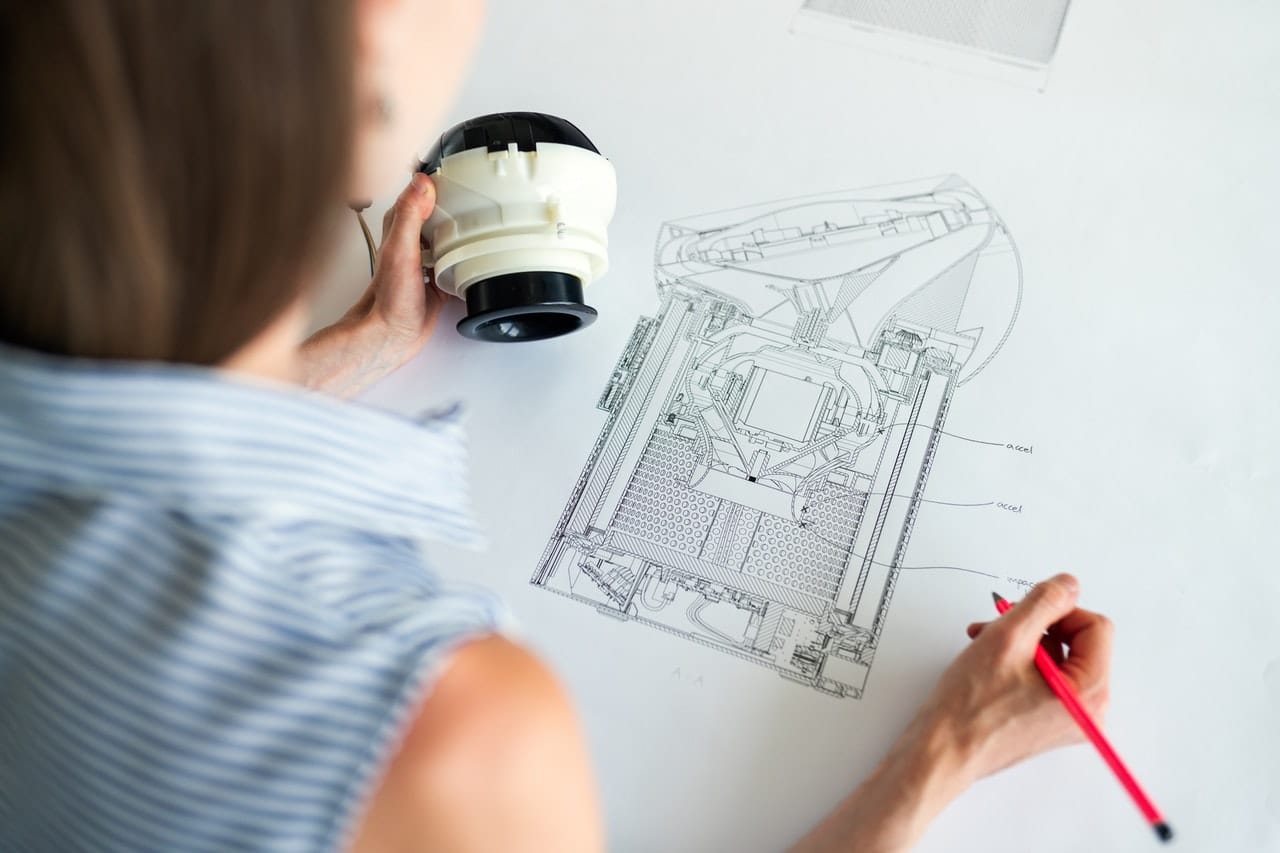
6 Product Development Trends to Expect, Post-Pandemic
A few months ago, several members of the SGW Designworks leadership team convened for a roundtable discussion that served as both a retrospective and a projection of where we see our company going in the months and years to come.
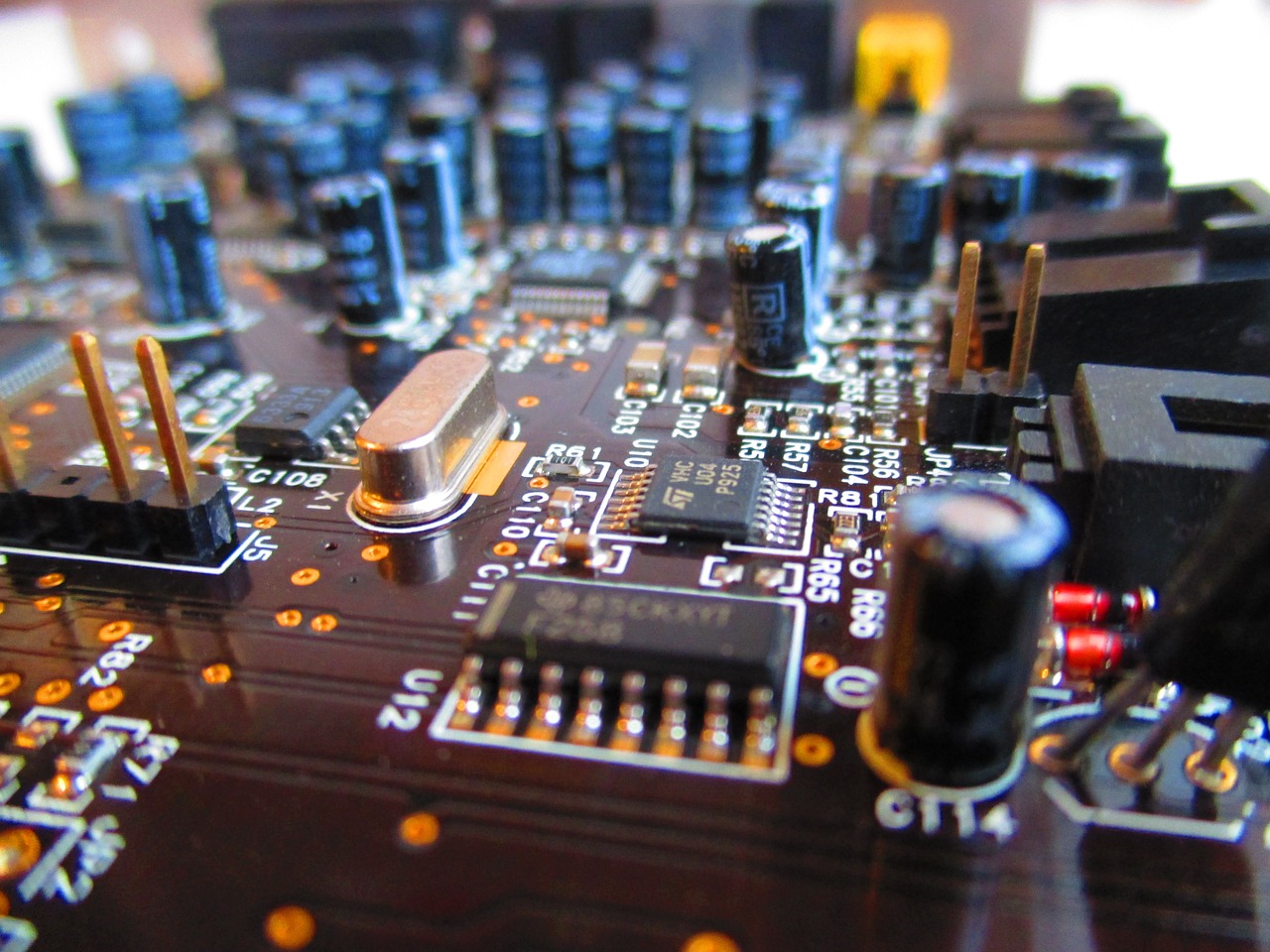
Lean Hardware Development: What’s Working Among Companies Large and Small?
If the terms “feature creep,” “waterfall,” and “agile methodology” are a regular part of your vernacular, it’s safe to assume your career entails lean hardware development.
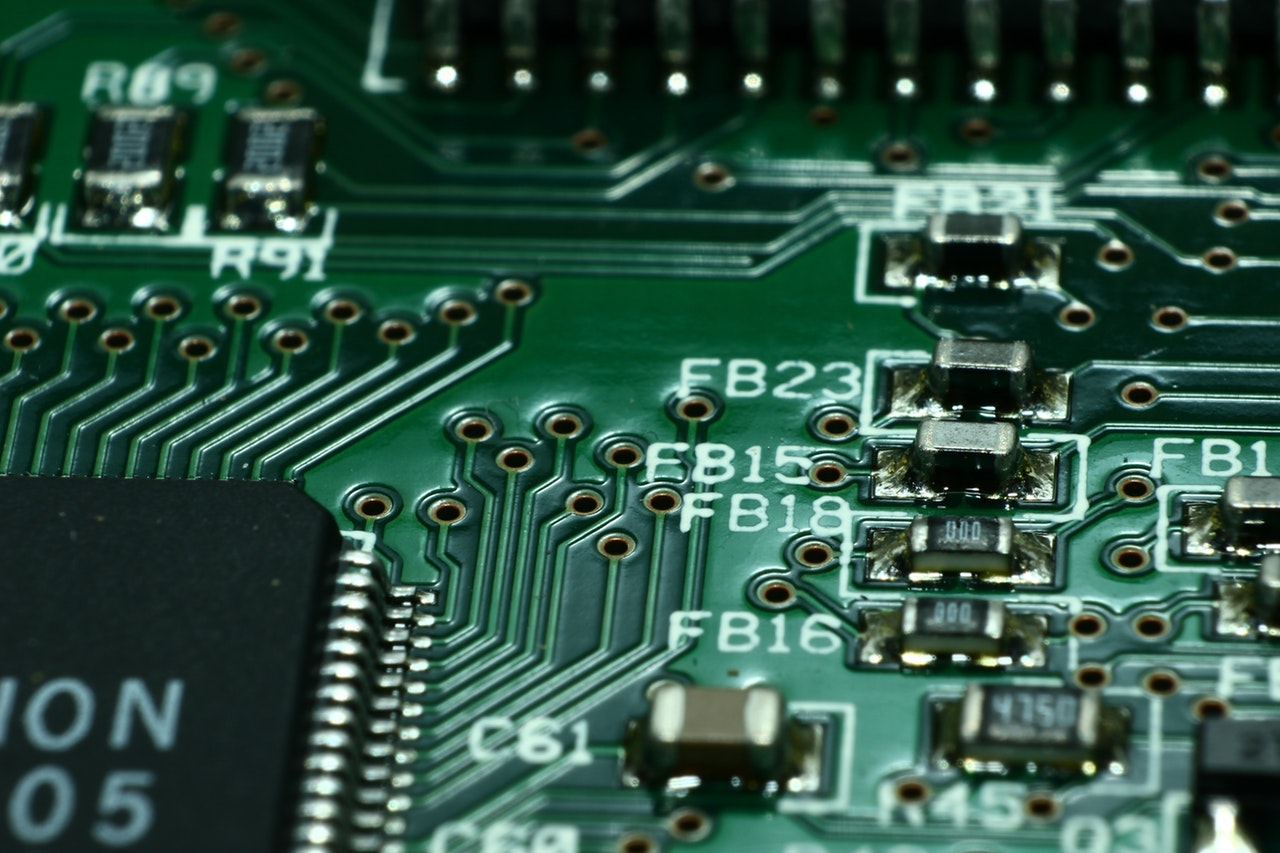
Electronic Product Design — and the Technology That Makes It Possible
As time goes on, more products are designed with integrated electronics to provide specific functionality or connectivity.
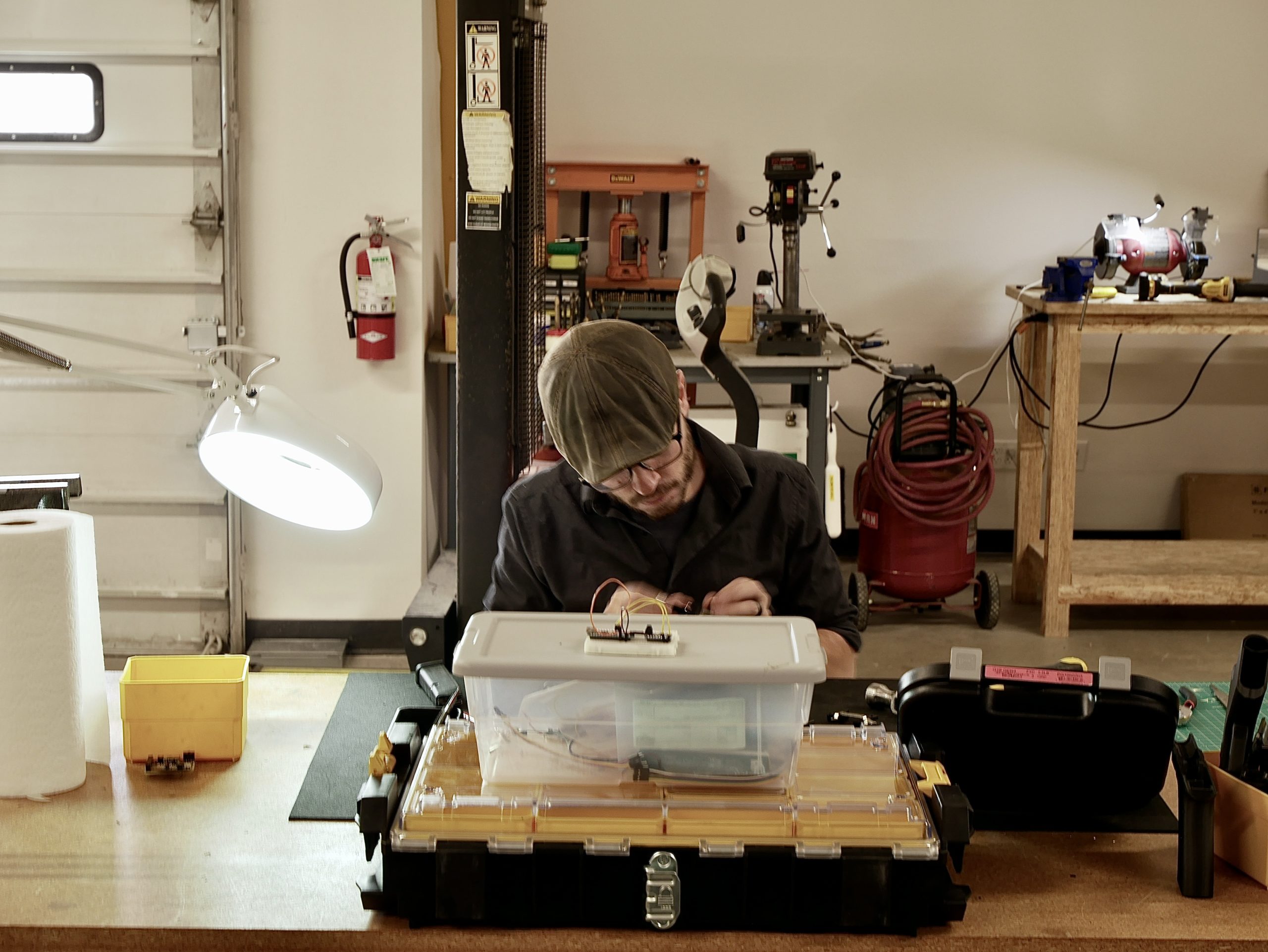
“Amazing People” Key to Our Success: Highlights from The BigTime Podcast
We’ve come a long way since our company’s inception in 2008.
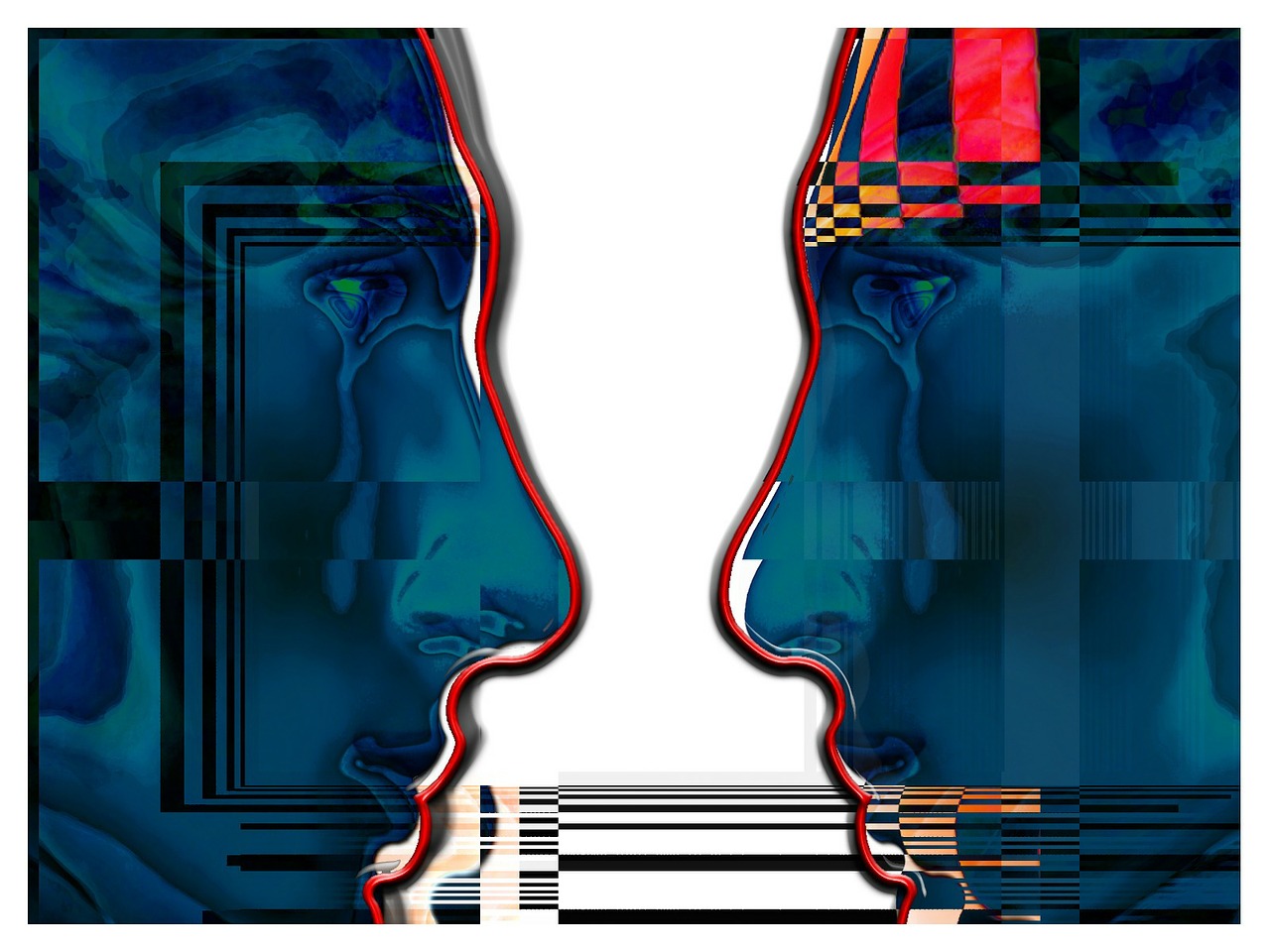
Empathy in Action: An Example of Empathic Product Design
When people hear the word “empathy,” many think of how it affects our interpersonal relationships, specifically how we relate to and connect with other humans.
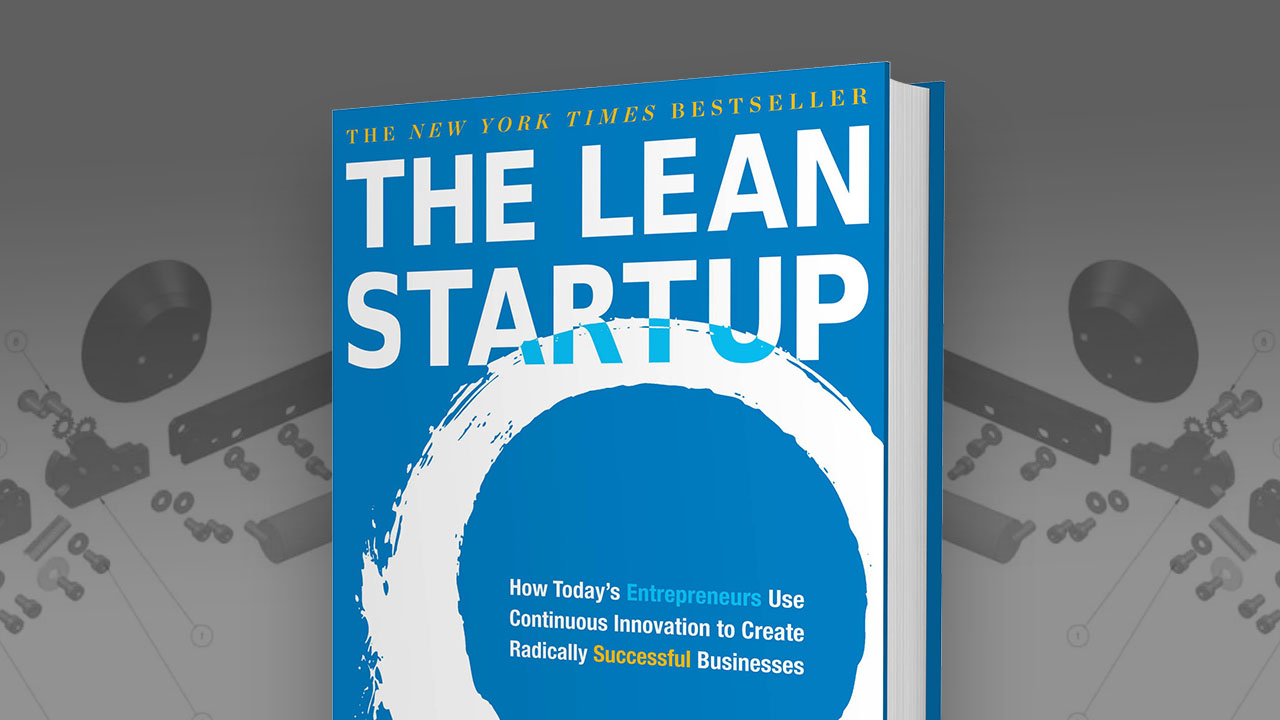
Lean Startup Principles for Hardware Development
True startup productivity requires systematically figuring out the right things to build.
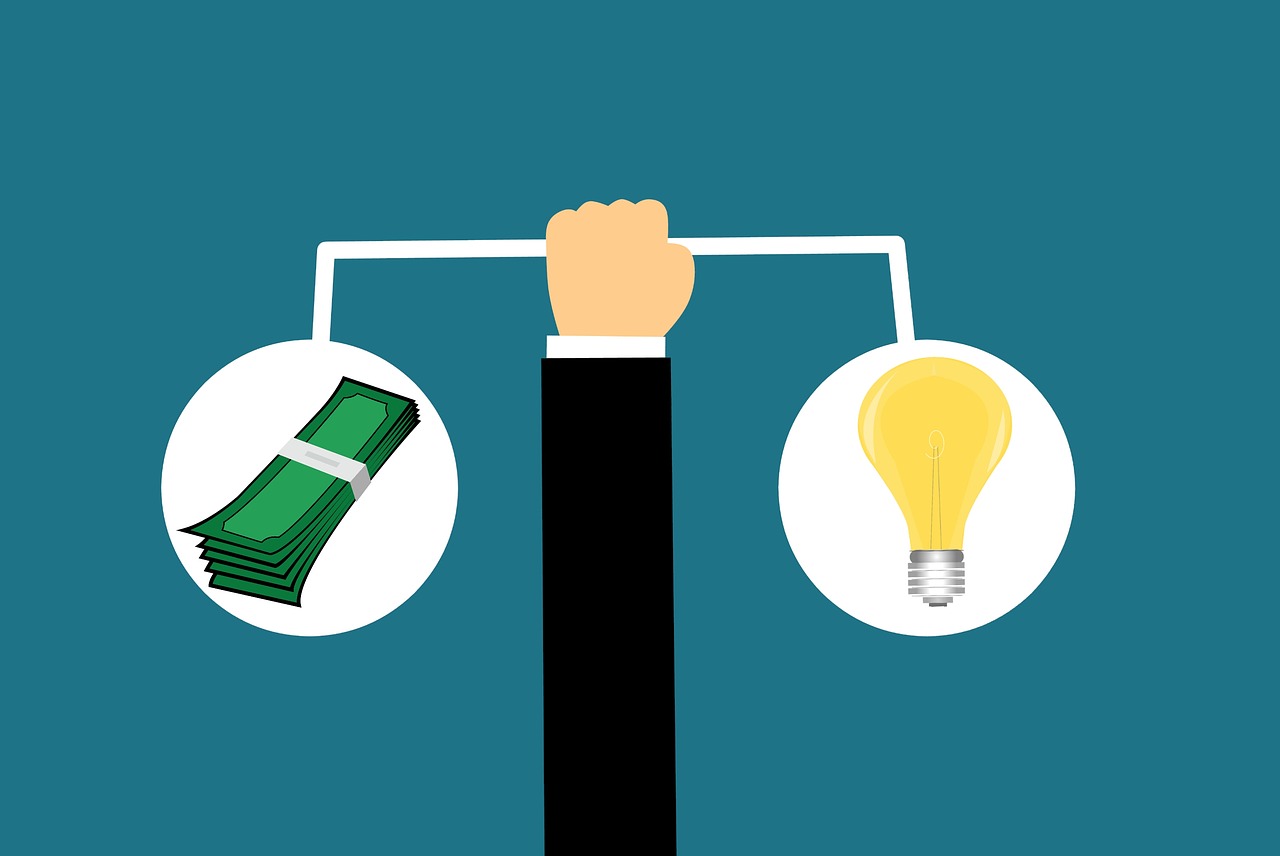
How Product Development Budget Affects a Project
Talking about budgets — and in this case, a product development budget — can be uncomfortable.
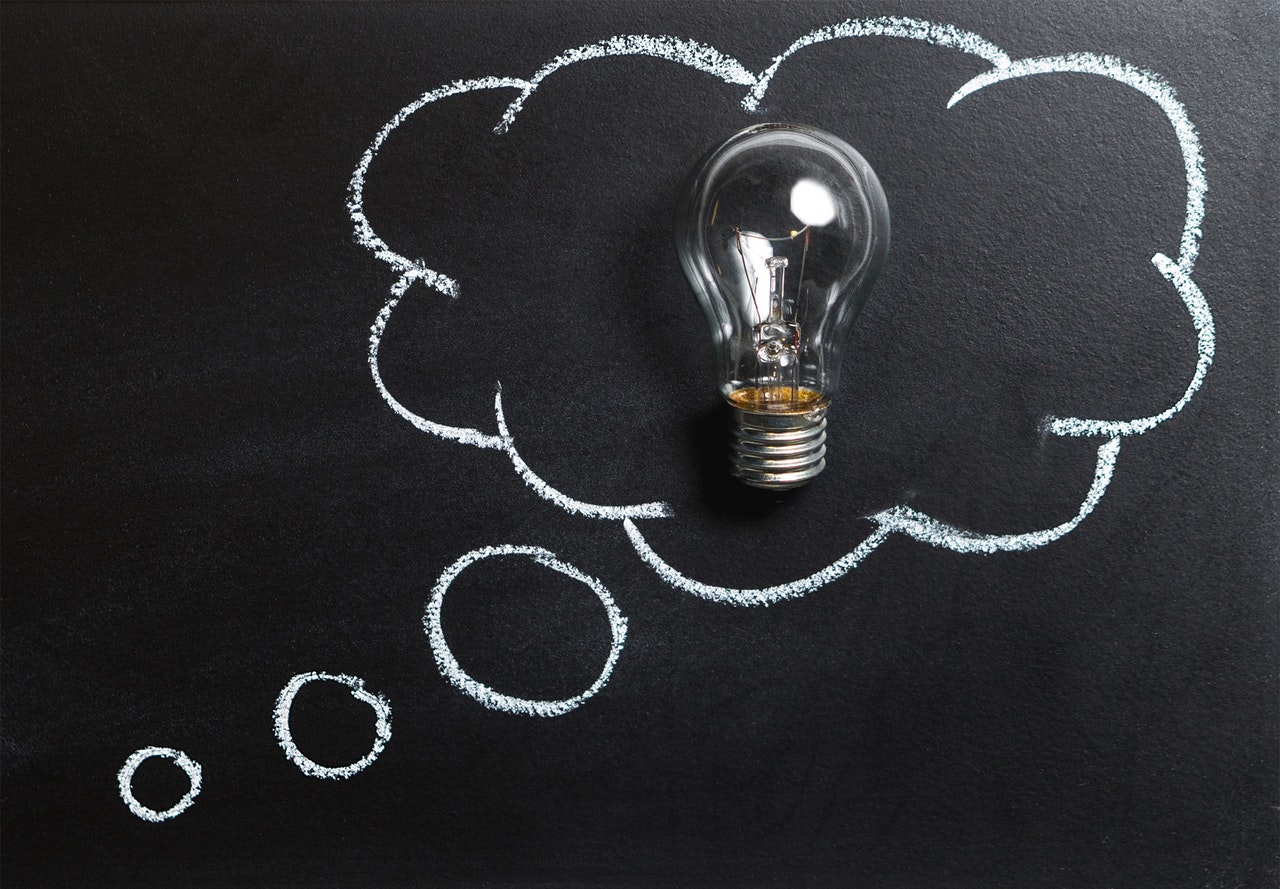
Prototype Development: The 4 Levels to Consider
Different levels of prototyping are appropriate at different stages of development. These are the four levels of product development before reaching a final product.
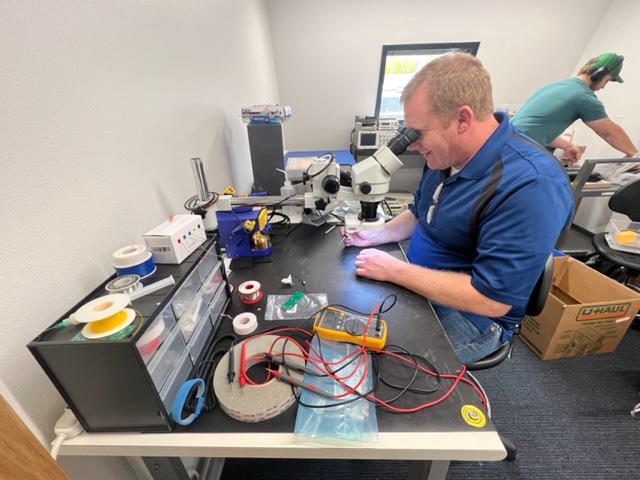
The Build-Measure-Learn Loop: The Linchpin of Successful Product Development
Since its publishing in 2011, Eric Ries’s bestselling book The Lean Startup (along with its principles, like the Build-Measure-Learn feedback loop) has ushered in an entrepreneurial revolution.
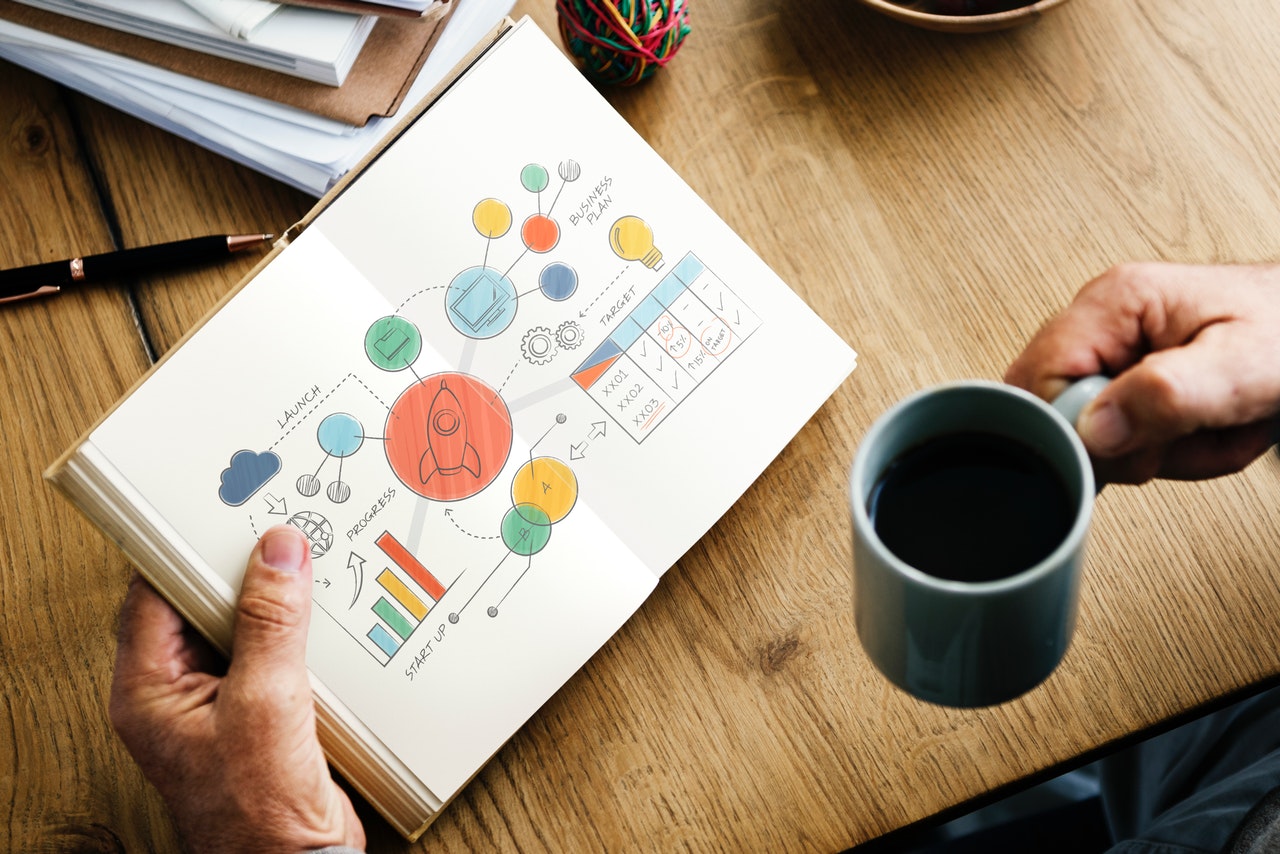
Commercializing an Idea: 9 Steps for Startups and Emerging Businesses
Mature businesses are keenly aware of the resources and investment required when commercializing an idea.
No items found.
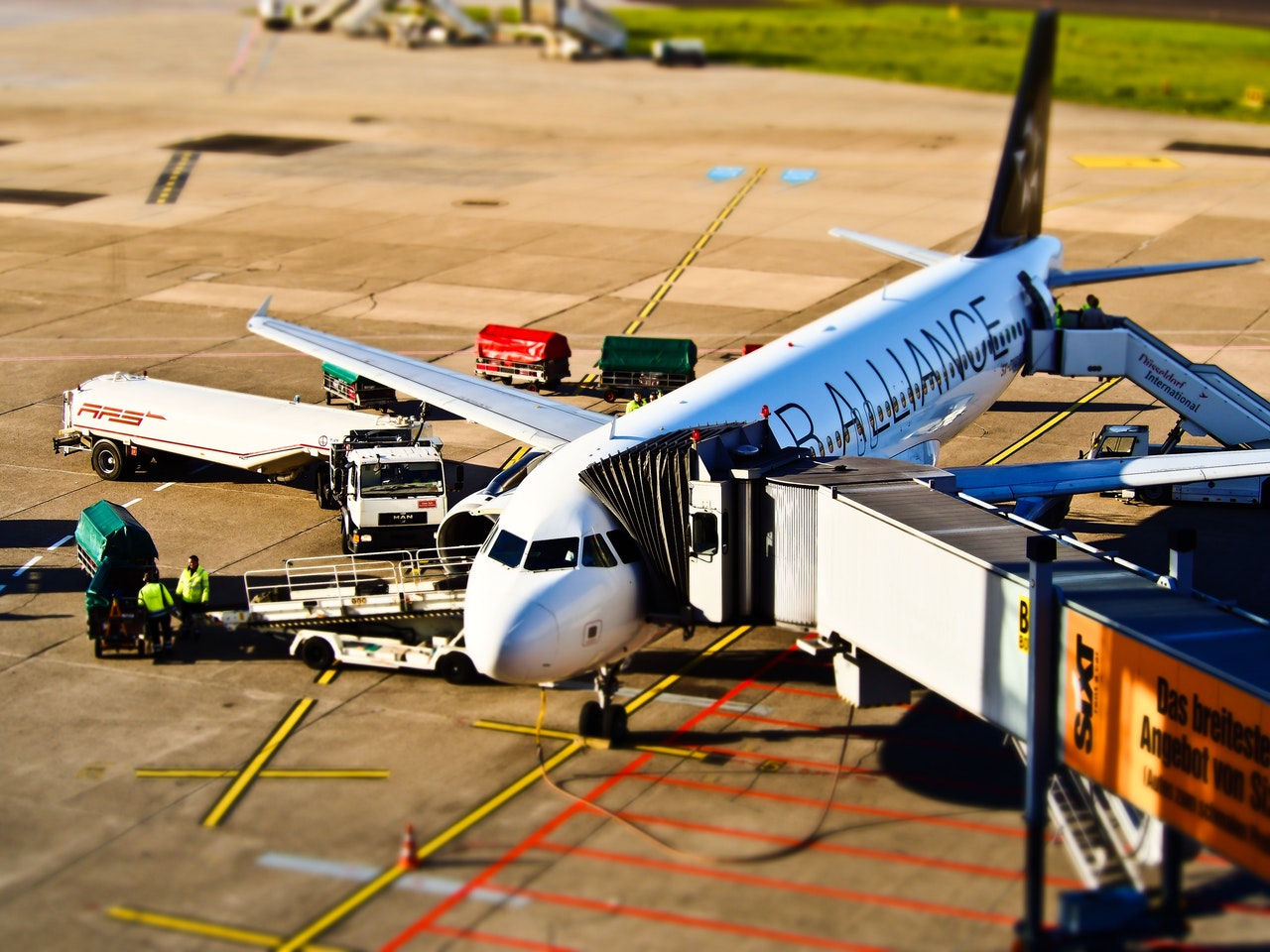
Exceptional Ground Support Equipment Design: The AERO Specialties Story
When AERO Specialties first reached out to us in 2013, we were eager to prove our ability to provide exceptional ground support equipment design.